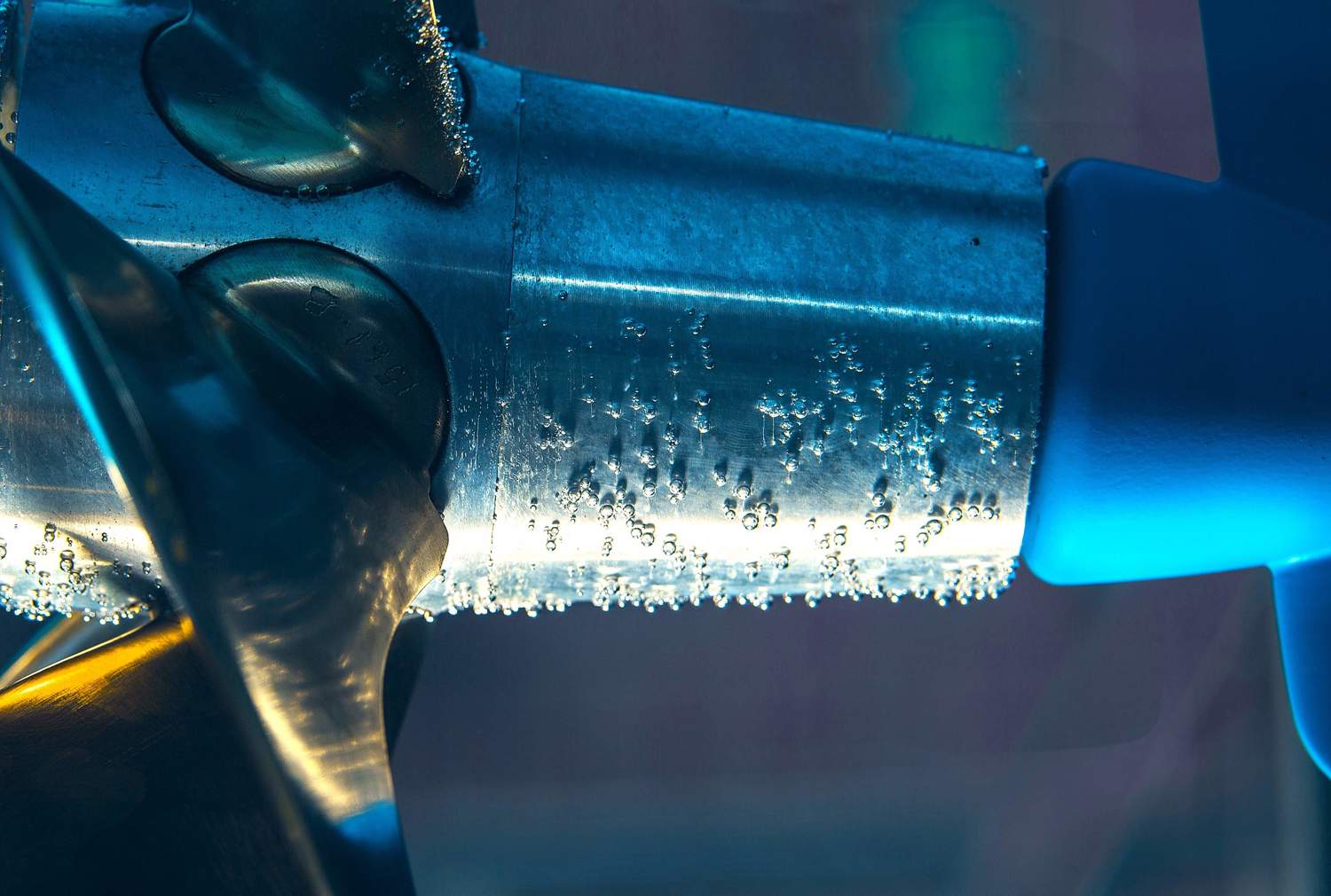
Kongsberg Hydrodynamic Research Centre
Over 80 years of testing, research, and design on the hydrodynamics of propellers, waterjets, and hulls
Kongsberg Maritime is the only marine engineering company with in-house hydrodynamic research and testing facilities – the Hydrodynamic Research Centre (HRC). Established in 1942, the HRC is comprised of engineers and hydrodynamicists. We uniquely combine computational fluid dynamics (CFD) and cavitation tunnel testing to deliver unmatched hydrodynamic solutions and designs that reduce fuel consumption and emissions on any vessel project, new build or refit.
Why we lead in hydrodynamic research
-
We have over 80 years of data on a range of projects, so we can provide data-driven guidance on new projects for quicker completion
-
Our hydrodynamicists work closely with product and sales managers for research that directly answers client needs
-
We have years of experience handling highly restricted naval projects for top tier blue water navies
-
We work with maritime universities and research institutes, including the Norwegian University of Science and Technology and SINTEF, one of Europe's largest research institutes
-
We use cavitation tunnels to physically verify computer simulations, a unique ability for solving complex hydrodynamic challenges
See the Hydrodynamic Research Centre
Find out how our global team of hydrodynamic experts solve key challenges for improved efficiency, reduced noise, and better seakeeping and manoeuvrability.
Our services and solutions
We provide a range of hydrodynamic tests and services for our clients, ensuring the highest quality standards on hull and propulsion efficiency for fuel savings, noise reduction, and reduced Opex.
How our hydrodynamic services benefit clients
FAQs: Propeller Design and Cavitation
For each vessel, the team adapts and optimises the propeller blades to a vessel's specifications to achieve highest possible performance based on key requirements, such as efficiency or noise levels.
The team collects information about the vessels’ mission, operational profile, and machinery system and then develops the propeller design. The designs are analysed using the latest simulation techniques in combination with the cavitation testing capabilities of Kongsberg.
The propeller design capability at Kongsberg is unique not only for its long experience but also wide-ranging experience. Designing propellers for fishing or cargo vessels is a different story from design propellers for the worlds’ most advanced Naval, Cruise, and RoPax vessels. We have done them all.
For example, the Naval segment is characterised by large programmes with extensive model testing and analysis. This is combined with strict requirements for efficiency, cavitation erosion, and cavitation inception speed (CIS), which drive the development of new designs and analysis methods.
The experience and knowledge gained from these naval programmes are applied to commercial projects where similar requirements can be seen, for example with ocean research vessels or superyachts. This makes our propeller designs best-in-class, regardless of vessel segment.
We also have extensive expertise in the design of underwater appendages to achieve good inflow to the propeller (wake field) which further boosts propeller performance. By involving us at the earliest stages of design, you can guarantee the most benefit over the long run.
Computational fluid dynamics (CFD) is a branch of fluid mechanics analyses and solves problems related to the flow of water or fluids. Computers simulate fluid mechanics, allowing researchers to assess the effect of various shapes in water.
High speed computers allow for better results and are needed to solve more complex problems. Continuous research using CFD results in better, more accurate software. When CFD results are combined with physical testing, as HRC can do with its cavitation tunnels, the resulting software becomes even more accurate.
Our unique ability to combine in-house experimental testing and numerical simulations builds confidence in our CFD models. We have also arranged High-Performance Computer Clusters (HPCCs) to speed up our CFD simulations for faster design service.
Performance predictions and CFD simulations are important elements of the hydrodynamic capabilities at Kongsberg supporting both internal and external customers. We perform simulations and predictions in an iterative process that results in the best performing hull and propulsion integrated solution.
Cavitation is generated when the pressure in the water around a propeller blade becomes lower than the water’s vapour pressure. The water is then broken up into cavities, or cavitation bubbles.
The picture shows a propeller of a typical RoPax ferry at medium speed. A tip vortex is seen coming off the propeller tips. This is the same kind of vortex that could be seen from airplane wings at take-off.
The vortex is generated by the pressure difference between the suction (front-facing) and pressure (back-facing) sides of the blades. The water is coming over the tip from one side to the other and generates a vortex. As the strength of the vortex increases with increasing propeller loading, the pressure drops and the vortex starts to cavitate and generate more noise.
On the blade at the top position there is a sheet cavitation, which is caused by load variations on the blade during the propeller rotation. Theses variations care caused by variations of water velocities coming into the propeller disc due to disturbances from the hull and shaft line.
While spinning, propeller blades have variations in loading that can be compared to an aeroplane flying in turbulence, all the time! Sheet cavitation increases pressure pulses towards the hull.
Cavitation is source of noise, specifically a cavitating tip vortex. If the tip vortex cavitation (the first cavitation to occur on a propeller) can be suppressed, the radiated noise levels is kept low even at higher ship speeds.
Another problem with cavitation is erosion or damage to the propeller. When the pressure in the water increases and comes above the water’s vapor pressure, cavitation bubbles around a propeller implode very quickly. If the implosion happens close to a surface, the energy could be directed into the surface causing high pressure loads to the material. This causes material fatigue and erosion over time. The material deteriorates and holes in the blade will appear if this process is allowed to continue over a longer period.
Unlike other propulsor suppliers, Kongsberg Maritime has a marine propulsion laboratory in Kristinehamn, Sweden, equipped with two cavitation tunnels, one free-surface and one conventional tunnel, giving a unique capability of Kongsberg to combine in-house experimental testing and numerical simulations build confidence in CFD models used for design and optimisation.
Both tunnels were built in 1970 and are housed in a special lab facility. Each tunnel holds a large volume of water that is driven in a large loop by a drive motor. These tunnels allow the HRC to build scale models of propellers and underwater profiles and insert them into the tunnel to measure exactly how they perform.
A schematic of the Cavitation Testing Tunnels used by the HRC The free surface tunnel is used for testing propellers in partially or fully submerged conditions behind a hull dummy. This allows verification of water flow around the hull and into the propeller. This tunnel is suited for testing waterjet units as a complete system with inlet, pump and steering/reversing unit as well as hydrofoil configurations.
In addition, a special test station in the large de-aerating section enables various interaction phenomena between propulsors and hull structures, at or near bollard pull conditions, to be investigated.
The second tunnel is used for testing propellers, waterjet pumps and thrusters in “open water conditions”, i.e. homogenous inflow with or without the effects of cavitation. The upstream drive unit is adapted for various shaft, hub and blade dynamometers, allowing measurement of torque and thrust of the entire propeller or, alternatively, forces acting on an individual blade.
Special tests can be performed, such as measurement of velocity distribution and propeller, rudder or nozzle combinations, or any kind of test with underwater objects, when the presence of a free surface is not required.
About 40 propellers are tested every year in our cavitation tunnels.
Kongsberg has long term relationships with partners in several countries through different projects, as well as our University Technology Centers (UTC) programme. We currently run two UTCs in Scandinavia to support strategic research. One is at Chalmers University of Technology in Gothenburg, Sweden; the other is at Norwegian University of Science and Technology, Trondheim.
The UTC-model creates a long-term mutual engagement, and within that framework, researchers and PhD students can work on topics that address the future needs of Kongsberg’s hydrodynamic capabilities and the entire maritime industry.
Our researchers are studying the hydrodynamic performance of vessels both in calm water and in their real operating conditions at sea, including wind, waves and currents. We are also developing simulation tools for cavitation and underwater radiated noise (URN).
The hydrodynamicists at Kongsberg collaborates closely with the university staff to guide the research and make sure results are being implemented and made available to designers at Kongsberg.
Brilliant research will not benefit vessel owners and clients unless it is integrated into our sales, design, and engineering tools. Our clients and our own product developers need to benefit from our latest research.
To ensure this, we developed our own proprietary information framework and software, PropCalc, which stores the results of experiments and simulations in a common database. That data is easily transferred from project to design, with different engineers entering the system at different stages, all using the same interface and the same data. PropCalc is also integrated into other Kongsberg tools and guidelines to allow sales and product development teams to benefit from new knowledge.
Common sales and design tasks are automated, while the production of diagrams, reports, and technical specifications for the manufacture of propellers has been automated.
This allows our sales and design engineers to focus on our customers rather than data handling and repetitive tasks. At the same time, we can produce state of the art material to help our customers find optimised solutions easily.