New product!
We have just added this product to our product portfolio.
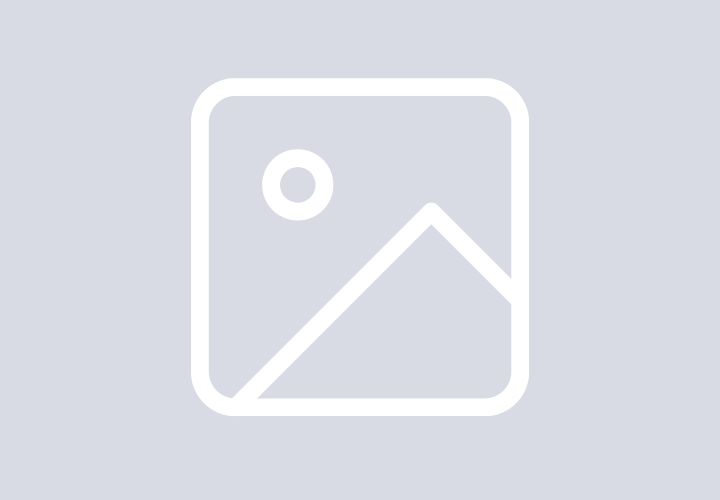
K-Sim® Cargo Product Carrier
Our Product Carrier model is based on a real double hull vessel. The model includes seven tank pairs, where one pair is SLOPs.
K-Sim® Cargo Product Carrier
Our Product Carrier model is based on a real double-hull vessel. It features seven pairs of cargo tanks, including one pair designated for slops. Each tank pair is equipped with its own independent loading and discharging lines, as well as dedicated systems for Vapour Emission Control (VEC) and inerting. Submerged, hydraulically driven cargo pumps are installed in each tank, enabling efficient cargo handling operations.
STCW Requirements
The LNG-M model meets the STCW requirements for sections A-II/1, A-II/2, A-II/3, A-III/1, A-III/2, and A-V/1, which cover:
- Safe loading and planning
- Cargo care during the voyage and unloading
- Trim, stability, and stress management to maintain seaworthiness
DNV GL Certification
This model is certified and approved according to DNV’s Standard for Certification of Maritime Simulator Systems ST-033.
Ship size and main details
- Deadweight: 83,890 GRT
- Length overall: 228.60 m
- Length between points: 218.70 m
- Width (moulded): 32.24 m
- Depth (moulded): 21.60 m
- Summer draught: 16.06 m
Tanks and pumps
- Cargo tanks: 14 (2 are SLOPs)
- Discharge rate: 860 m³/h
- Ballast pump rate: 1,100 m³/h
- Vapour control system: Yes
- Cargo manifolds: 7
- Vapour control manifolds: 7
Training Objectives
The main aim of this model is to provide a full understanding of cargo-handling operations. Specific learning goals include:
- Getting familiar with all parts of the cargo system
- Planning cargo loading or discharge using the LoadMaster load computer
- Lining up for loading and ballast handling at the same time (with atmosphere checks)
- Using vapour emission control (VEC) during operations
- Controlling cargo flow into each tank and managing the ship’s trim and list
- Completing topping up and final loading
- Preparing and lining up for discharge, including inert gas system use
- Starting discharge from one or more tanks with different cargo types
- Tank washing, with correct pressure and spray angles
- Draining and emptying final tanks
- Final ballast adjustment for departure
- Heating cargo during the voyage
- Venting tanks for inspection or dry docking, using explosion diagrams for each tank (included in the model)
Note: Specifications may change without notice.
Lifecycle support for your vessel
-
24/7 Technical support
Our 24/7 technical support team is there to help at any time, day or night, wherever your vessel is.
-
Conversions, retrofit and refit
Upgrading and enhancing your vessel’s performance.
-
Training
Maximise crew efficiency and reduce downtime with expert training.