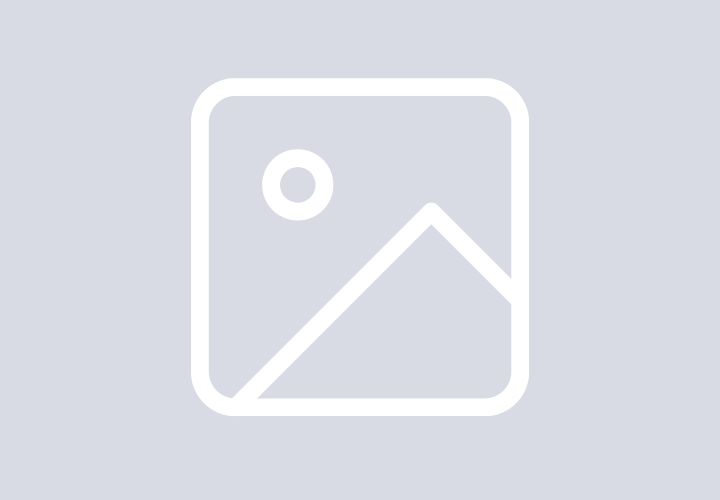
Process Automation, K-Pro
Process Automation, K-Pro
Our process control system provides you with robust and reliable solutions for the automation and safety for production of oil and gas in a modern context. Over many years, KONGSBERG has been involved in the evolution of process control solutions, and has been an active participant in utilizing the synergy of dynamic process simulators and control systems.
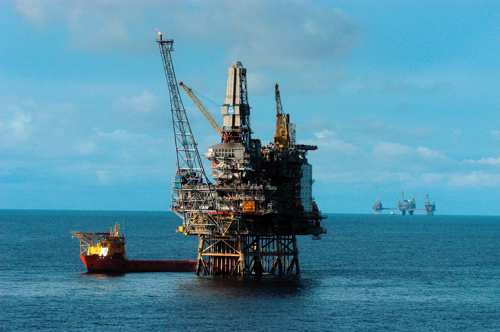
The full picture
KONGSBERG's system philosophy is based on the use of a distributed and open system design that employs a system-wide standardized communication network. The network facilitates free flow of information from sub systems, with system wide information on multifunctional workstations. A common base technology and user interface for all automation applications ensures a safe and reliable operational environment.
The KONGSBERG integrated control system is more than hardware and software modules. It is a solution that ensures stable and optimal production. Combined with our dynamic process simulator, for DCS checkout and control philosophy testing, this ensures excellent control of the process and reduces the need for flaring and CO2 emission.
The automation system is designed for large scale integration of all automation applications in your installation. The real benefit of the integration is in operation, modification and maintenance; the operators have a unified operator interface and alarm system, easing the training of your operators. Common hardware and software platform reduces the amount of spare parts needed and thus reduces the life cycles cost. A common information management system transfer information to the base organization for support and optimization of your reservoir and production processes. The level of integration may vary from full integration of control logic at the package level and integration of unit control panels, to common human machine interface.
Process & control applications
- Hydrocarbon stabilization systems
- Gas sweetening, gas treatment and gas lift
- Power generation and distribution
- Generator control
- Turbine control
- Compressor control
- Fiscal metering
- Oil and gas export systems
Gas processing systems
- Time stamping
- Advanced motor control
- Full power distribution control system (PDCS)
Power management system
Utility and auxiliary systems
- Produced water treatment
- Fresh, hot and sea water distribution
- Gas, water and chemical injection
- Jet fuel and diesel oil system
- Nitrogen/Inert gas system
- Glycol storage and distribution system
- Lube oil, hydraulic oil and compressed air
- Topside open drain system
- Heating and cooling medium
- Flare system/fuel gas system
- HVAC
Subsea control systems
- Redundant subsea communication lines
- Well and manifold temperatures and pressures
- Sand detection • Electrical power unit
- Hydraulic power unit • Shutdown sequencing
- Valve, choke control and movement
- Water, gas and chemical injection
- Well control
- Manifold
- Multiphase flow meter
- Corrosion meter
- Valve signature
- Housekeeping functions
Our common user interface is used throughout the system to make operation simpler. This provides benefits across the board from faster learning and higher safety through to increased operational efficiency – qualities that save time, effort and reduce mistakes all in all saving money. Professional user input has been vital in the development of the new user interface and its implementation into the K-Pro system.
Upgrades and modifications of control systems is part of the system life cycle. There are a number of reasons for upgrades and retrofit – here is a few:
- The plant is extended in lifetime, and new technology contributes to the extended lifetime.
- The plant is extended with new process equipment, and the control system needs expansion beyond the original spare capacity.
- New technology assists is increased oil recovery.
- Development in 3rd party equipment controlled by the control system.
KONGSBERG has been involved in a number of retrofit exercises. Our track record and experience proofs that the K-LINE control system can be upgraded with minimum downtime of the plant.
When upgrading the complete system onboard a platform, ensuring a shortest possible down time is a requirement. Such upgrades have been done more than once by KONGSBERG. One of the success factors in such upgrades is extensive testing, also involving the client.
Increased oil recovery (IOR) means upgrades of the control system and process equipment as the reservoir pressure is declining. Such rebuilds requires a revision of the dynamic model to verify rebuild of process equipment. As a consequence, the control and safety system also has to be upgraded.
IOR may require alternations in process equipment because of too low pressure, or means to increase the pressure by various means of injection, will be necessary. KONGSBERG takes interest in assisting the client using the dynamic process simulator to verify the process, the field equipment and modify the control and safety system accordingly. The upgraded simulator is a useful tool when training the operators prior to start-up of the upgraded plant.
Services & aftermarket support
Our support teams, located worldwide, are committed to helping you manage the vital balance between operational availability and cost. Wherever your vessel is located, our support is close at hand.
Lifecycle support for your vessel
-
24/7 Technical support
Our 24/7 technical support team is there to help at any time, day or night, wherever your vessel is.
-
Conversions, retrofit and refit
Upgrading and enhancing your vessel’s performance.
-
Training
Maximise crew efficiency and reduce downtime with expert training.