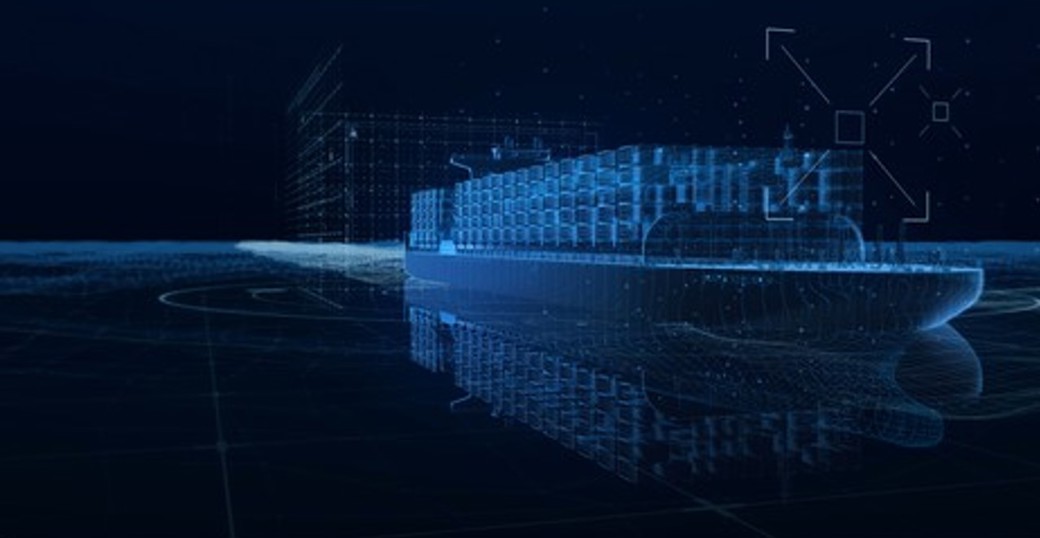
LNG and intelligent power generation: A quick way to cut emissions for container vessels
LNG fuel and use of PTOs could be key to ensuring that container vessels are as efficient, sustainable and future-ready as possible.
There are some areas where leading the market is a bad thing; producing the highest GHG (greenhouse gas) emissions is one of them. Energy production and use accounts for nearly three-quarters of global GHG emissions, or the equivalent of 36 billion tonnes of carbon dioxide (CO2eq) a year. Of that, around a quarter (8 billion tonnes CO2eq) is generated by transport, with shipping responsible for approximately 10% (800 million tonnes CO2eq).
The largest contributors to this are container vessels, but even the most ardent environmentalist would struggle to argue that change is easy. Containerisation is the lifeblood of our global economy – so how can we set about maintaining trade whilst at the same time minimising its effect on the planet? Driven by environmental awareness and the ongoing introduction of increasingly stringent regulations, many container shipping companies are already achieving significant emissions reductions through the simple strategy of slowing down, but this approach is necessarily limited. New vessels need to use fuel more cleanly and efficiently, and refits should follow the same path as closely as possible.
The IMO (International Maritime Organization) agrees. In phase 3 of the EEDI, or Energy Efficiency Design Index, all newbuilds are required to be 30% more energy-efficient by 2025 than those constructed in 2014. For larger container vessels this deadline has been moved forward, from 2025 to 2022. The same focus on larger vessels continues when we look at the reduction targets: smaller 15,000-40,000dwt (approx. 1,250 to 3,350 TEU) container vessel newbuilds will be allowed to meet the standard 30% EEDI reduction rate, but this then rises incrementally with vessel size up to a 50% EEDI reduction rate for the largest container vessels of 200,000dwt (approx. 20,000 TEU) and beyond. Combine this with the IMO strategy to cut CO2 emissions from 2008 levels by 40% before 2030 and 50% by 2050, and the urgency of this issue becomes clear.
Kongsberg Maritime (KM) has been developing a range of solutions for container ships to help address these targets and boost sustainability within the industry. With strategies for everything from 2,000 TEU feeder vessels and 15,000 TEU Panamax ships up to the largest 24,000 TEU vessels, KM has devised future-proof and cost-effective design proposals which offer shipowners practical and workable strategies to assist them in planning their future newbuild, upgrade and refit paths, and in addressing their emissions reduction targets.
For container vessels, one of KM’s strategies in the effort to lower emissions is the adoption of LNG as a fuel. The CO2 emissions from LNG are as much as 24% lower than for diesel/MGO, SO2 is reduced by around 99% and NOx by around 87%, which teamed with negligible ash and particulate production makes it one of the most environmentally friendly fuels currently available. Robert Eriksson, Senior Concept Engineer, Business Concepts, Kongsberg Maritime, explains: “Use of dual-fuel engines and LNG contributes to significant emissions savings over MGO, from 14-21% depending on the engine,” he says. “This takes into account pilot fuel use and methane slip, as well as LNG use. It also has a significant effect on OPEX; teamed with careful management of power generation capacity, we believe savings of up to 20% can be achieved.”
A key difference between container ships and other vessels is the sheer amount of power required. “Container vessels can consume huge amounts of electricity, especially when carrying refrigerated containers,” explains Eriksson. “Therefore, you see quite big gensets on these vessels. LNG-fuelled vessels tend to have two-stroke dual-fuel engines for propulsion and four-stroke dual-fuel engines for auxiliary power. These auxiliary engines can be bigger than many other ships’ main engines, and you’ll usually have at least four of these gensets on board. If we can reduce their use and/or number, we can save both emissions and running costs.”
KM’s solution to this high power demand is to add a shaft generator to the main, two-stroke propulsion engine as a PTO (power take off): a far more efficient arrangement than running auxiliary generator sets. The aim is that, through use of PTOs, some of these engines need not be used at all – or even fitted, in the case of newbuild vessels. Research carried out by KM’s Business Concepts team proposes that, by adding a PTO, a 14,000 TEU vessel – which might typically use a 50MW, two-stroke propulsion engine and four 4,240kW four-stroke auxiliary generator sets – can be more efficiently powered using just three generator sets and the PTO output from the main engine. Generator sets cost more than PTOs, so this represents a significant CAPEX saving, as well as reducing OPEX by around 2% and CO2 equivalent emissions by up to 3%.
“Using a PTO reduces overall running hours for the generator sets,” explains Eriksson. “The propulsion engines are running anyway, so by using a PTO we just take advantage of unused capacity. This allows one or more generator sets to be shut down. In addition, the larger cylinder sizes of the two-stroke propulsion engines are inherently more efficient, so it’s a win-win situation.”
For vessels running on LNG, this setup will also reduce methane slip, the process by which unburned fuel escapes into the atmosphere. “A two-stroke dual-fuel engine will have significantly lower methane slip than a four-stroke, so avoiding running the four-stroke reduces methane slip,” Eriksson continues. “Combined with the fuel savings, that’s a compelling environmental argument for a PTO system.”
Efficient power
A wider study carried out by Kongsberg Maritime, comparing the per-hour running costs and energy curves of two-stroke and four-stroke engines, highlights another benefit of shifting load to the propulsion engines. “Two-stroke engines run very slowly,” explains Eriksson. “80-90rpm at steaming speed, while four-stroke engines typically run at 720rpm. Because they move a lot more, the operating costs in terms of wear are actually very high. Four-stroke engines also have many more cylinders, which has a direct effect on wear and consequent maintenance. If you’ve got four of them, you’re logging many hours of service time.
“Two-stroke engines are also more efficient than four-stroke. Four-stroke engines are at their most efficient running at around 85% load, using less energy per kilowatt hour produced than at lower loads. But even when a four-stroke engine is running at peak efficiency, the two-stroke engine will be about 10% more efficient. Add the fact that the two-stroke efficiency curve is flatter everywhere, and that’s the whole reason why you’d want to take energy from two-stroke engines instead of four-stroke: it’s simply more efficient, less costly and has less of an environmental impact.”
Optionally, adding energy storage can introduce a level of redundancy which enables further reductions in the use of auxiliary generator capacity, as well as load smoothing and peak shaving capacity. The containerised, lithium-ion battery modules which constitute the core of KM’s SAVe Energy storage system for hybrid power operate on the principle of Dynamic Inertia Control. This is designed to optimise generators’ fuel efficiency by apportioning power usage between all components.
By charging batteries when generator capacity permits and providing supplementary power at times of peak loading, a reduction in overall emissions, noise, vibration and operational/maintenance costs can be achieved. In a similar study carried out by KM for LNGC, addition of an Energy Storage System delivered modest reductions in annual emissions and OPEX of 0.7% and 0.9% respectively, largely due to a projected reduction in auxiliary generator running hours of 78%, compared with 65% for a PTO without energy storage.
New concepts
KM are demonstrating that efficient use of existing technologies can already make huge differences to the sustainability of container ship operations, both for newbuild and existing vessels. At the same time however, they have an eye for the future – these concepts will be as relevant when next-generation fuels become commonplace as they are today.
Of course, any change has to made in the harsh light of business reality, but KM’s studies have taken this into account. Paul Fredrik Gjerpe, Vice President, Business Concepts, Kongsberg Maritime, explains: “We’ve shown that there are some definite OPEX benefits to using LNG and our PTO strategies, but what about CAPEX? Installing a PTO can pay for itself, as they are cheaper than generator sets, but there’s no doubt that LNG systems are more expensive – up to US $20m more than for an MGO-fuelled vessel. But we did some calculations, and the additional machinery costs can be offset by the efficiency savings over a period of between 10 and 15 years, taking financing costs into account. That makes economic sense, as well as helping to make the vessel as future-proof as possible.”
“There’s no doubt that a fuel transition is on the horizon,” adds Oskar Levander, SVP Business Concepts, Kongsberg Maritime. “The problem is, we don’t know what it will be. By designing our solutions around LNG we are making them as future-proof as possible: HVO (Hydrotreated Vegetable Oil), biogas and synthetic methane can all be used by dual fuel LNG engines without any major modifications, and an LNG system designed the right way can be converted for use with ammonia, albeit with uprated and increased tank capacity to cope with the lower energy density of the fuel. Of course, a dual fuel engine can also burn MGO, so that gives six possible fuels to choose from.”
“Choosing the right fuel is going to be important,” agrees Gjerpe. “But we’re also looking at the wider picture – how to make sure that get the best from your fuel. There are still efficiencies to be made, and the use of PTOs is a key enabler for this. Our research is quite clear – propulsion engines and generators sets are often underutilised, which means that they’re not running efficiently. PTOs allow use of spare capacity, meaning fewer generator sets need to be running, saving fuel, emissions, wear and service costs. It’s a no-brainer for us – we believe that a holistic, integrated approach to power use is going to be a key component of efficient container shipping in the future.”