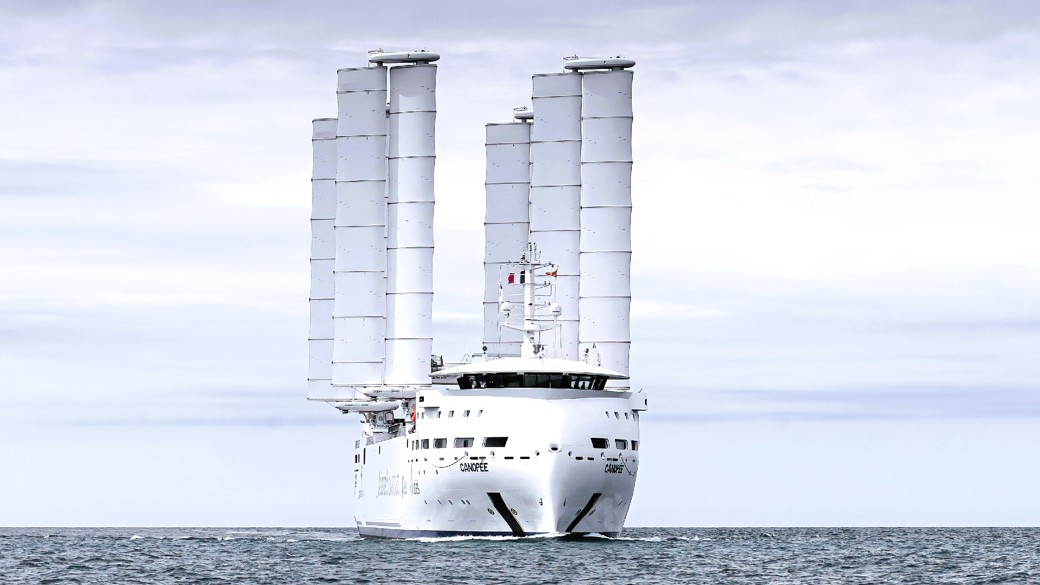
Comparing wind assist technologies for ship owners
Can wind assist technology help solve the problem of emissions reduction in the maritime industry? The answer is yes, but successful implementation requires the right type of solution and integration
Wind assist technology and propulsion systems are getting plenty of attention from ship owners and the media. Done right, wind assisted propulsion systems can offer immediate reductions in fuel consumption and emissions, taking into consideration operational profile.
Calculations by our researchers show that a theoretical Handymax container cargo ship running a route in the North Atlantic from Rotterdam to New York would see a fuel burn reduction of 19.3% annually with the right wind assist propulsion system.
We estimate that wind assist technology, deployed during the build phase or during a refit on an existing vessel, can save anywhere between 5 and 25% on fuel.
The real challenge for vessel owners and operators is knowing which type of wind assist technology will deliver the most benefit.
We work with vendors of different wind-assist solutions as an advisor to owners and integrator of technology. That means we can provide the analysis vessel owners need to make the right decision about which wind assist solution is best for their needs, based on ship data such as routing information, hydrodynamic and performance analysis.
We can even help integrate different types of wind assist technology on the same vessel.
In addition, we provide a range of engineering services to optimise wind assist technology on any vessel, including: engine and equipment optimisation, automation, propeller optimisation, energy storage solutions, installation, and commissioning, plus the power and information management integration.
There are four main types that we work with, each with its own advantages:
Flettner Rotors
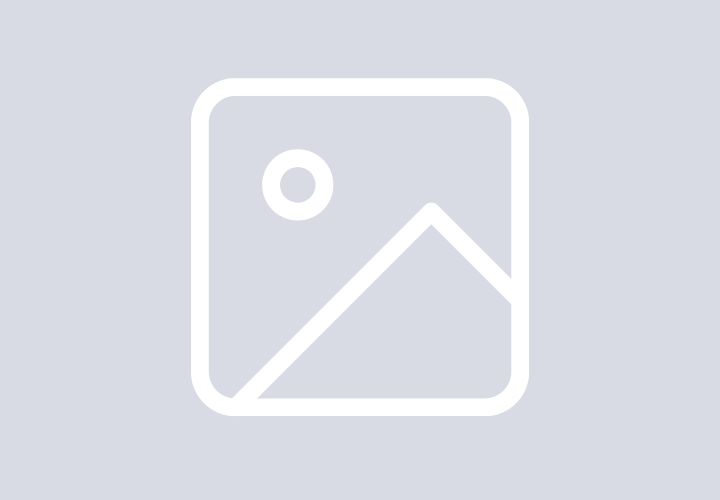
In 2020, ferry operator Scandlines installed a 30x5 Norsepower Rotor Sail™ on MV Copenhagen, finding that its operations between Rostock and Gedser were favorable for wind propulsion. Photo courtesy Norsepower.
A Flettner Rotor is a tower that spins around on its axis. As air passes around the tower, the aerodynamic shape of the tower creates a force perpendicular to the wind direction. This force is caused by the Magnus effect, which results in a pressure difference between the sides of the rotor, like a wing.
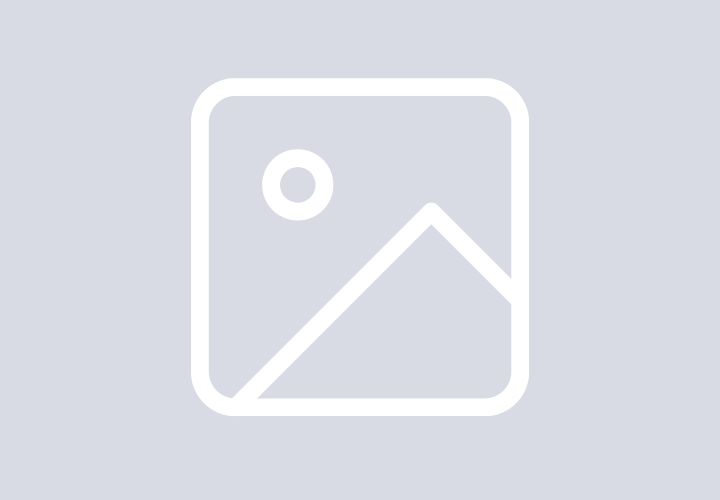
The Magnus Effect on a Flettner Rotor. Courtesy Norsepower
- They offer high performance on a small footprint, so they don’t take much deck space
- It is a relatively simple design
- It can easily be retrofitted to older vessels
- It is a relatively proven concept among wind assist technologies (apart from soft sails)
- Flettner rotors offer excellent performance on reaching points of sail (true wind angle of 90° to 160° from the bow)
- Flettner Rotors can create drag at higher speeds
- The rotors can potentially obstruct cargo handling operation in certain vessels, unless they are tilted
- They perform less well upwind due to their lift to drag ratio
- They require electrical power
Wing sails
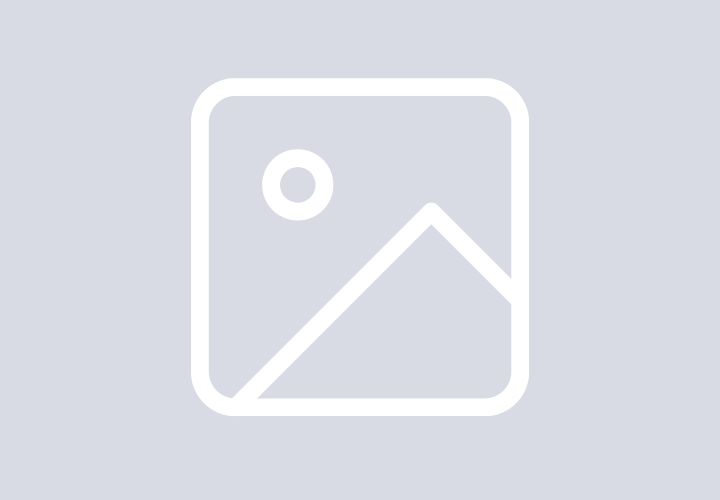
AlfaWall Oceanbird, a joint venture between Alfa Laval and Wallenius, offers the Oceanbird Wing 560, made of steel, recycled PET and fibreglas, standing 40m high, and weighing 150t. A main sail and a flap optimise aerodynamics, and the company says one wing sail on existing RoRo vessel can reduce main engine fuel consumption between 7 and 10% in favourable conditions
Wing sails, sometimes referred to as “hard sails”, have developed largely due to recent America’s Cup Yacht Races. They are essentially upright wings on the deck of a ship generating lift that is turned into propulsive force. A modern wing sail can have lift coefficient (a measure of how much force is generated) higher than the wings of a Boeing 787 Dreamliner.
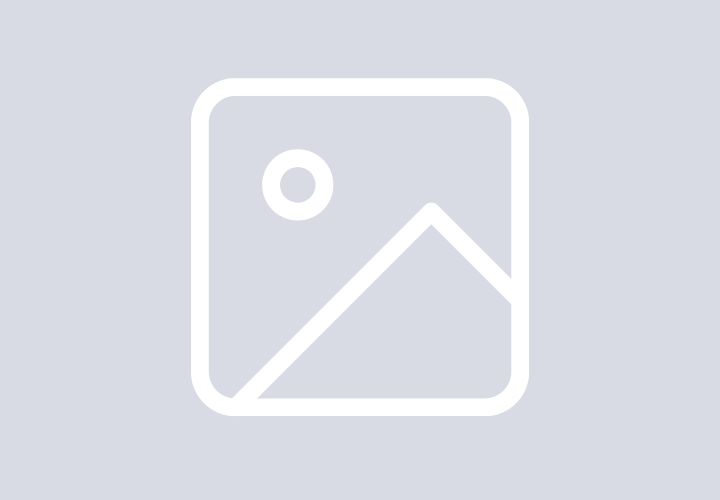
Four OceanWings®, by AYRO, fitted to the Canopée, a 121m cargo ship that transports the Ariane 6 rocket from Europe to French Guyana, sailing since 2023. Photo courtesy AYRO/OceanWings
- Minimum power requirement to run the system
- Proven technology
- Foldable, allowing for ease of stowage
- Wing sails operate better in upwind conditions due to their high lift per drag ratio
- It is more difficult to reef the sail (reduce sail area) and therefore reduce power in strong winds, unless the wing can fold down
- Wing sails are sensitive to the angle of attack and require regular trimming
- Wing sails require a relatively large surface area
Suction wings
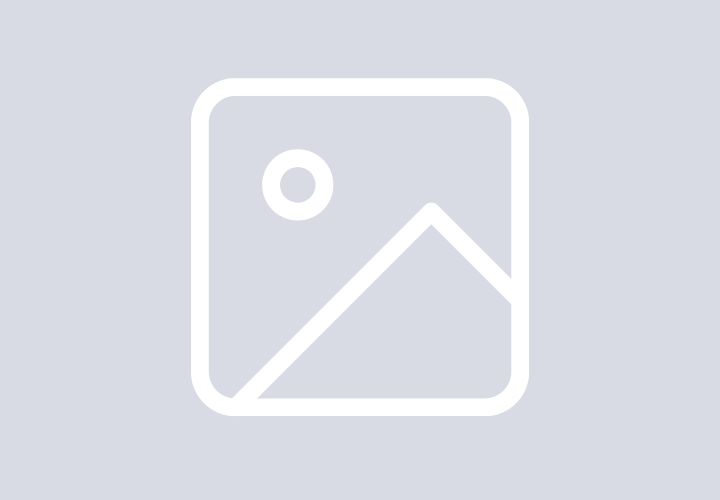
eConowind's VentoFoil suction sail technology aboard the Frisian Sea. Twin 10m VentoFoils were installed in 2019 on a movable deck arrangement. The VentoFoil can be folded down and is strong enough to withstand hurricane-force winds. Photo courtesy eConowind
Suction wings, like hard sails, resemble aircraft wings. But these structures have vents near the trailing edge and internal fans that help create boundary layer suction which delivers a higher propelling force due to the improved aerodynamic performance.
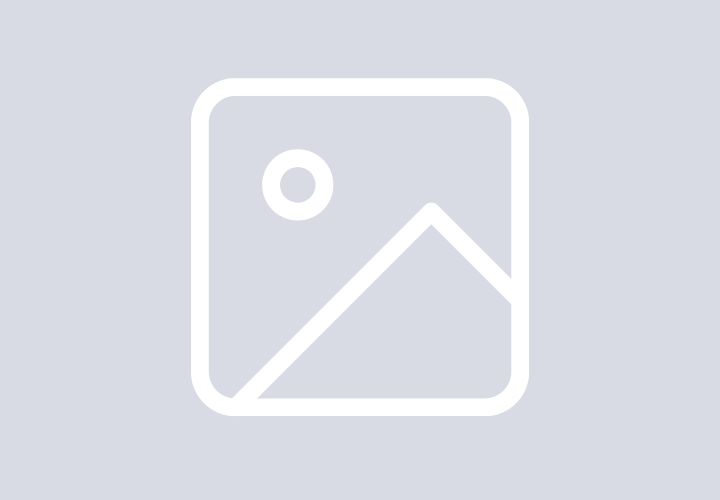
Bound4Blue's eSails suction sail technology aboard the 90m EEMS Traveller cargo vessel, each unit 17m in height, project completed in June 2023. Photo courtesy Bound4Blue
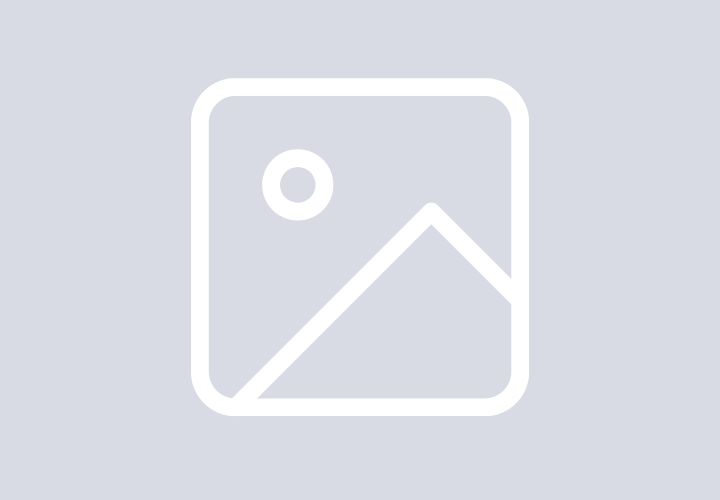
The effect of suction sails. Courtesy Bound4Blue.
- Suction wings offer good performance on a small footprint
- Installation is usually easy – as a refit project, it can be done in hours for some vessel types
- The suction wing system can be folded down for passage under bridges.
- The “wing-like” performance offer good upwind performance
- Operation generates relatively high noise
- Downwind performance can be less relative to other wind propulsion types
- Suction wings require electrical power
Soft sails
Soft sails are the closest option among wind assist technologies to traditional sail systems. They consist of masts and fabric sails that can be shaped and furled. Superyachts have continued to use soft sails, and new developments have emerged that may also be applicable to the shipping industry. A concept that was developed in the 1960s by German naval architect Wilhelm Prölß (1901–1974) that re-imagined old sailing cargo ships but with new rigging has been deployed on two superyachts.
- Very lightweight
- Flexible and can be stowed as needed
- Furlers allow for control and operation from the bridge
- Require large sail area for good performance
- Soft sails have relatively higher maintenance needs due to the limited life of sail cloths
- The frequent replacement of soft sails can become expensive over time
- Upfront investment costs for rigging can be expensive
Wind assist solutions are still being developed, such as Kite Sails, which use a large wing kite that flies in figure 8 patterns high above a vessel to create propulsion. In some cases, there is a blurring of lines between wind assist types. A French naval architecture firm (Ayro) has developed a wing sail concept make out of soft sail cloth.
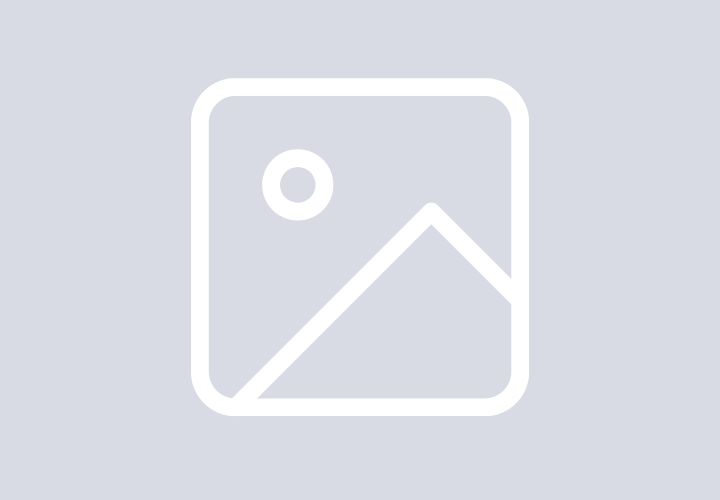
Ayro's use of soft sail technology in Wingsail format. Courtesy AYRO
We offer vessel owners the chance to get started on wind assist propulsion project – either as new build or refit – with clear answers that suit a vessel’s requirements and creates real fuel and emissions savings.