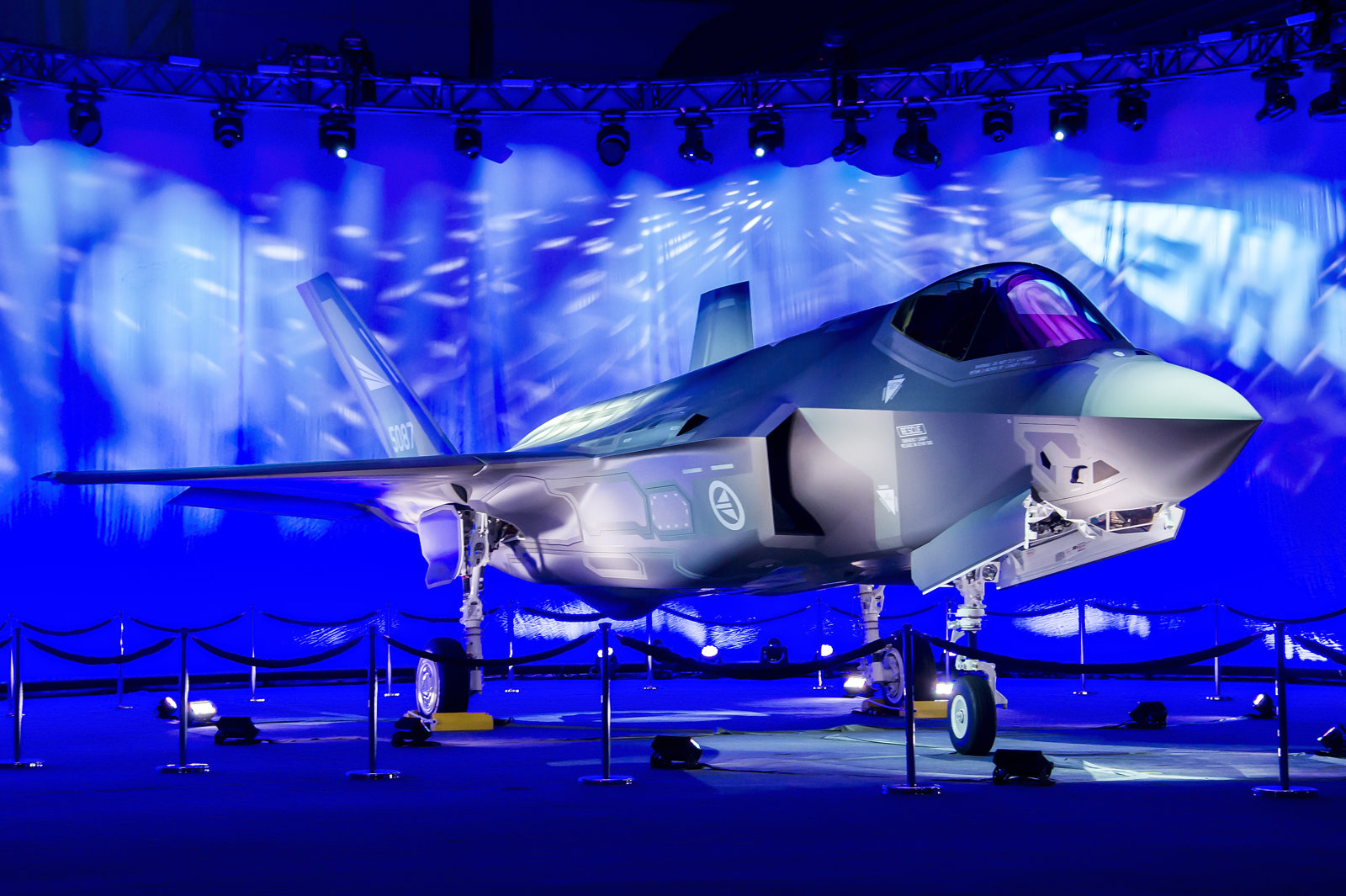
The F-35 has been a demanding undertaking for KONGSBERG. This is the story of how challenges are turned into success.
-
Text:OVE RONNY HARALDSEN
-
Ove Ronny HaraldsenGroup Communication Manager
Fort Worth 22 September 2015: For a brief moment the production hall is in darkness. There’s not a sound to be heard. Then the curtain falls. Norway’s first F-35 Lightning II comes into view. The floodlights sweep over the wings. The fuselage is bathed in blue and purple light. Heavy techno music comes from the speakers. The auditorium rises in applause. The images are streamed across the globe over the Internet. Leaders from the Norwegian and American Armed Forces as well as industry and the press are in the audience.
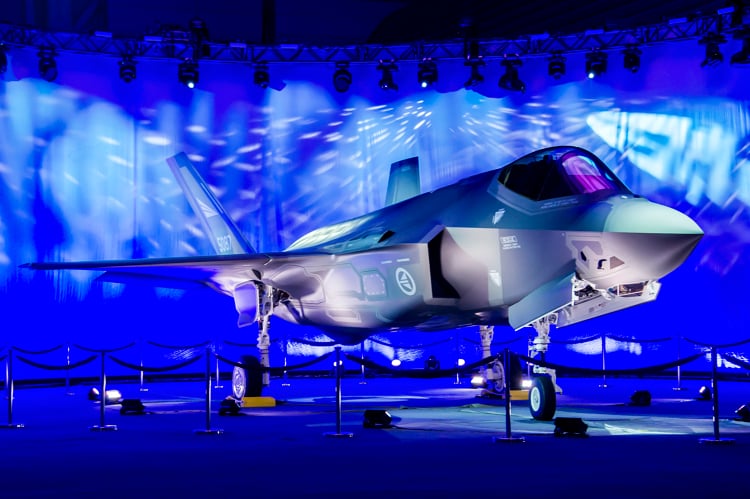
The ceremony marks the first of 52 combat aircraft being delivered by the manufacturer Lockheed Martin to the Norwegian Armed Forces. Armed Forces Chief of Defence Haakon Bruun-Hanssen stands at the lectern.
“I would like to conclude by congratulating all those involved. You have managed to deliver the aircraft on time. I look forward to continued collaboration, interaction as well as further development of the fantastic F-35 system. Thank you very much”.
CHALLENGING TIMES
Two weeks earlier. We follow Atle Wøllo up the stairs to the office on the fourth floor of Arsenalet outside the town of Kongsberg. From the window we look down on the production facilities where parts for the F-35 combat aircraft are designed, checked and sent to the factory in Fort Worth, Texas. Photos and plaques on the walls testify that Atle is among those who have been part of the project since the beginning. From the initial dealings with the F-35 programme back in 2004—via the opening of Arsenalet in 2008—to the signing of the centre fuselage of the first Norwegian F-35 in 2014.
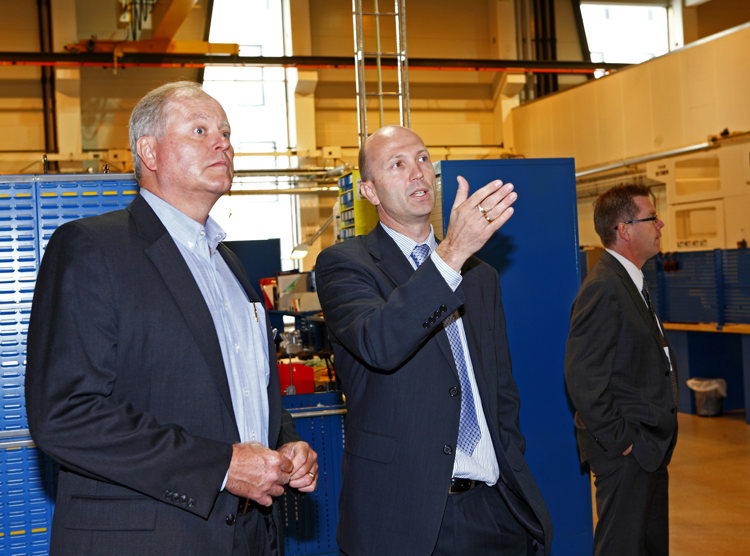
Atle Wøllo has a comprehensive story to tell. About tough contract negotiations. About pressure regarding production costs. About the uncertainty concerning the annual number of aircraft to be produced. “We have to admit—at times it has been extremely tough. When you have done everything you thought was possible to reduce costs and costs still need to go down, then you have to think creatively”, says Atle Wøllo.
NEVER GIVING UP
KONGSBERG’s first deliveries for the F-35 programme consists of aircraft parts in composite materials and titanium as well as parts of the fuselage and rudder. More specifically, these parts are: “Rudder & Vertical Leading Edge”, “Composite Details and Assemblies for Centre Fuselage” and “Air to Air Pylon”.
Back in Fort Worth, Terje Bråthen is sitting amongst the audience in the auditorium. Bråthen is Executive Vice President at the Arsenalet factory. He regards the mighty aircraft standing impressively on the stage. Thoughts turn to all those who have made it possible for KONGSBERG to get where it is today. Men and women in the Aerostructures department who never gave up the struggle to keep production costs down.
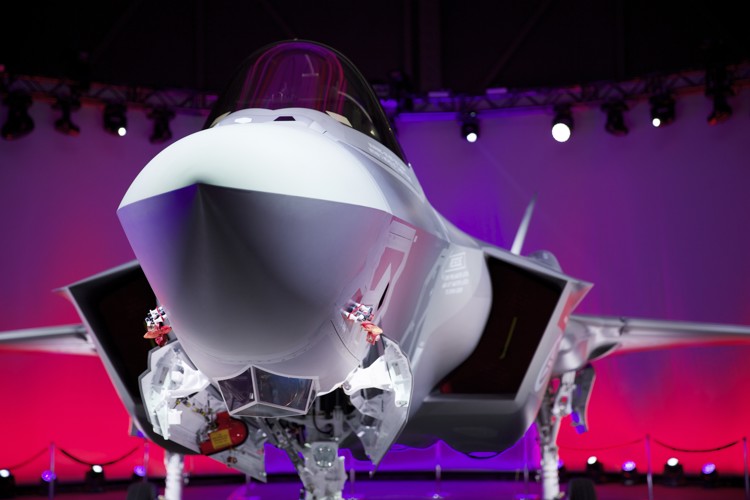
“An amazing effort has gone into keeping costs down— primarily by using “high-end” technology. But also by looking at the components we were commissioned to make and proposing completely new ways of manufacturing them”, says Terje Bråthen, Executive Vice President Aerostructures.
DEMANDING QUALITY REQUIREMENTS
It was back in November 2008 that the government announced that Norway had selected the F-35. Atle remembers a special drive out to Arsenalet on the eve of the factory opening. “On the way there we heard on the radio that Norway had chosen the F-35. There we were with Americans in the back seat translating in real-time what the Government had decided. It was pretty special”.
Later came the period when KONGSBERG had to qualify as a supplier. Not a single aircraft component could be delivered before Lockheed Martin had reviewed and approved every single detail of the production plans. Test parts were examined by x-ray and microscope. There was an extreme focus on quality throughout every aspect of the process—an effort that would pay off later, giving KONGSBERG major competitive advantages.
“KONGSBERG has not dispatched any incorrect deliveries for the F-35 programme since 2012. This gave us a huge advantage when we subsequently went out and competed for further contracts for the combat aircraft”, says Atle Wøllo.
INNOVATION PAYS OFF
When Arsenalet opened in 2008, KONGSBERG had designed the factory to produce parts for an estimated 368 aircraft over a five-year period. However, only 150 aircraft were actually produced, resulting in Arsenalet going into the red during these years. “We had to work very hard on reducing costs. We had no choice”, says Atle Wøllo.
Nevertheless, low production freed up resources that could be oriented towards achieving innovation. Increasingly tough demands from the customer triggered a number of initiatives, including a project focused on innovation that has since become a textbook example for subcontractors for the F-35 programme. Previously, parts that were included in the rudder on the F-35 were made from blocks of titanium. This meant that 98% of the raw material was machined away.
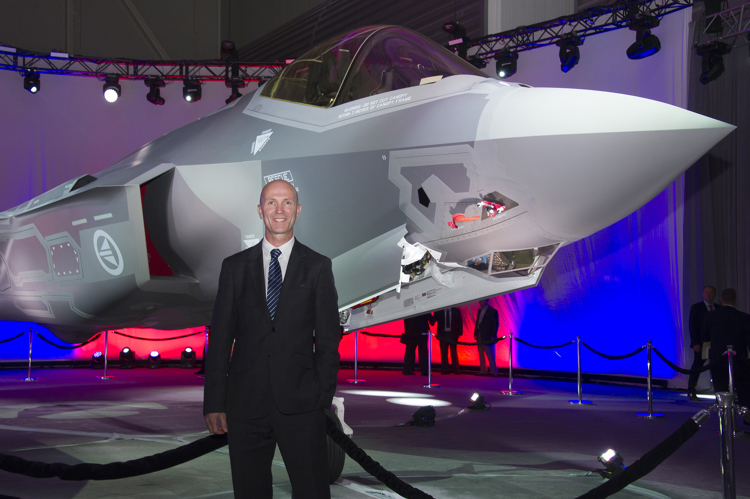
“By challenging the design proposed by the customer, we managed to introduce shape forging as the starting point for the machining process. As a result, significantly less titanium is machined away”, explains Wøllo who then adds: “The fact that we left no stone unturned in our search for improvements means that we might be in a better position today than we would have been if the production rate had been as predicted”.
GROWTH AS A RESULT OF THE TASK
The work carried out in order to reduce costs has made KONGSBERG highly favourable with Lockheed Martin. The willingness to think creatively is cited as a strength that characterises the organisation. “KONGSBERG has delivered under pressure”, confirms Lorraine M. Martin, Executive Vice President &General Manager of the F-35 Lightning II Programme.
“Reducing costs is extremely important. This can be achieved through large-scale production but also by good ideas. KONGSBERG has presented us with ideas on how components can be produced in a fundamentally different way— at lower cost and without lowering the quality”.
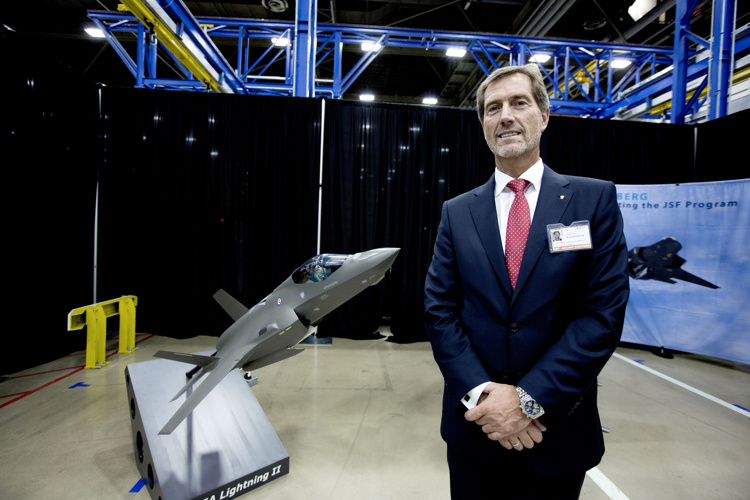
In May 2015, KONGSBERG proudly presented the agreement for a new aircraft component for the F-35. A success achieved yet again with time-consuming negotiations on multiple levels. The agreement involved the production of “Main Landing Gear Closeout Panel”—two hatches in composite materials to completely cover the wheels of the F-35. The contract is yet more proof that KONGSBERG has passed the test as a supplier to one of today’s most advanced technology projects. The high-quality and on-time deliveries have given KONGSBERG a competitive advantage that could open up new opportunities in years to come.
“We want to be a leading technology company. We can only achieve this if we work with the best companies and the most advanced technology. Some of the challenges we have faced in this programme have presented us with such opportunities. It is therefore important for us to continue to be on the front line and take on these types of challenges”, says CEO and President Walter Qvam.