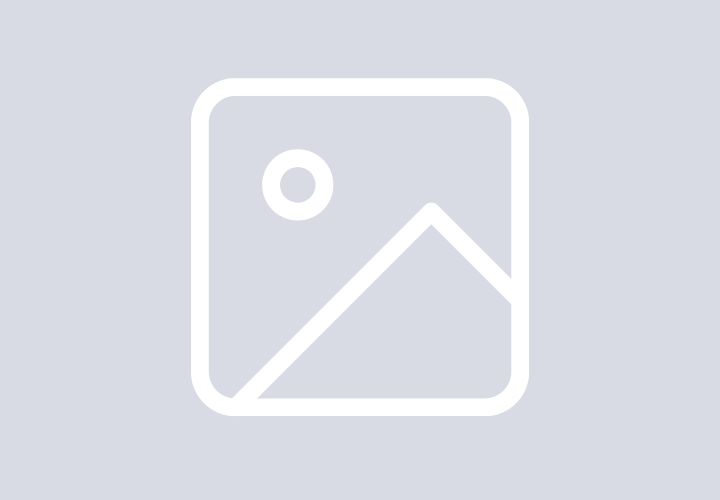
Composites
Composites
Kongsberg Aerostructures & MRO is a trusted supplier of complex and high tolerance composite parts and assemblies for the most demanding environments.
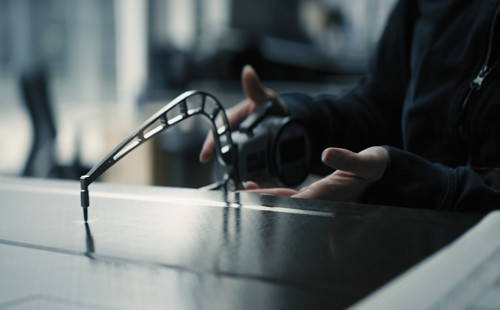
Kongsberg Aerostructures & MRO have utilized advanced composites in their successful missile programs for more than 2 decades, and have extensive experience in composite manufacture for 5th generation fighter aircrafts programs.
Step by step
The following step-by-step process describes manufacture of a simple composite structure demonstrating KONGSBERG’S manufacturing process at large. There are countless varieties of manufacturing some of which require three autoclave cures.
-
1. Material handling, cutting and kitting
Rolls of prepreg (resin impreg¬nated CFPR ) is stored in our automated freezer hadling-system at appr. -20°C to delay curing and ensure up to two years shelf-life. The prepreg is cut into different sized pieces based on design requirements. A cutting machine with a vibrating knife enhances cutting quality and ca¬pability. Pre-cut kits are stored for large production series.
2. Laminating/lay-up in clean room
The prepreg is placed in moulds, layer by layer, to build structure and strength. The direction in every layer is predefined, influencing strength and stiffness. Laser projectors project the end-of-plies to facilitate its location and sequence in complex structures. Clean Room of 2800 m² offers high capacity for large simultaneous production mixes.
3. Bagging
Typically a plastic film is placed over the composite component, edges sealed, and air is extracted to prevent entrapping volatiles/air before the mold is placed in the autoclave.
4. Autoclave/demould
The autoclave cures the composite material at a pressure typically up to 7 bars and 180°C. Autoclaving is used to ensure high quality and level of repeatability of the production.
In Demould, the composite component is taken off the mold and prepared for next operation.5. Bonding
Parts can be integrated into assemblies. Ingoing details can be composite laminates, various metallic details (steel, aluminium, titanium) or metallic/ non-metallic honeycomb core materials. In most cases the assembly operation is done using various types of adhesives. The preparations prior to adhesive application is of paramount importance and consists typically of chemical cleaning and light sanding/ abrasion to remove any traces of dust, grease or any other contamination which may affect the bonding quality.
The bonded assemblies are usually cured in ovens at elevated temperatures to reduce cure cycle times.6. High precision milling (PMM)
Part surfaces are machined, the outer edges trimmed, and the holes drilled. Our Zimmermann PMM provides the high precision milling necessary for large volumes of complex structures. Offering high volumetric accuracy better than 55 microns and large dimensions on parts in an integrated automated manufacturing cell.
7. Co-ordinate measuring machine (CMM)
Subsequent to the milling of the part, it travels down into an automated co-ordinate measuring machine. The part’s dimensions are verified to the requirements. All this happens with the part still attached to its tool, vacuum or mechanically clamped.
8. In-house ultrasound and X-ray inspection
Once a part has been bought-off in the CMM area, it is inspected using ultrasonics to check the integrity of the material; free from pores, other defects or foreign objects. Ultrasonic scanning of highly complex curved surfaces is performed using a Midas 5+5 multi-axis scanner. Further, we are capable of conducting X-ray inspection of thin composite panels up to 250 mm steel or titanium.
9. Prime and paint
In order to environmentally seal the composite part/assembly, various types of paints are sprayed onto the part. This can be done manually or using a robot. KONGSBERG uses a CNC Robot ABB with a painting area of 2100 x 4400 mm. To enhance bonding properties primers are also sprayed onto the details.
10. Mechanical assembly
Usually before a part is delivered to the customer it goes into mechanical assembly. After surface treatment/ painting, all mechanical details are drilled/countersunk/deburred before they are bolted/bonded in its correct locations to the requirements. A part is completed after surface treatment. Metals are then mounted such as fasteners.
11. Final inspection
At final inspection the part’s build-history is verified. An inspector checks that all operations have been signed off, and all applicable document records have been collected and are in line with both customer and internal requirements.