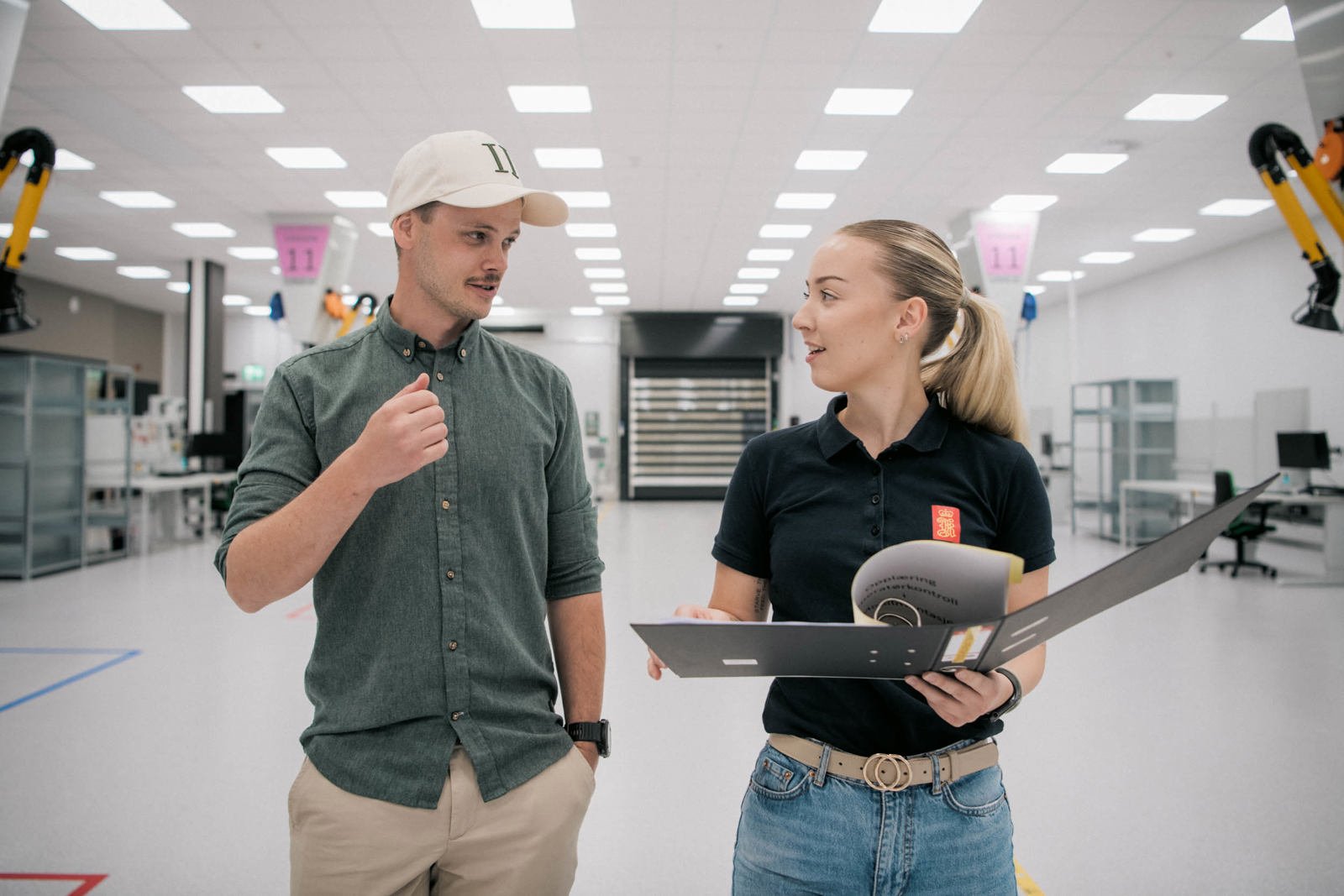
A key to increased productivity and attractiveness
At Kongsberg Defence & Aerospace (KONGSBERG), the implementation of a key provision in the company's Industrial Agreement and improved the attractiveness of roles within production and operations. By enabling greater flexibility and expanded responsibilities for skilled workers, this provision fosters innovation, collaboration, and enhances overall competitiveness—vital elements during a time of significant growth and transformation.
-
Text:Anita Nyheim / KONGSBERG
Photo:Magnus Bjørnnes / KONGSBERG
The local agreement to implement the new provision called “Bilag 5” was signed in January 2023 and has since been adopted across several company departments. Currently, around 40 workers benefit from the arrangement, which increases flexibility by enabling a broader distribution of roles among skilled workers. The ability to take on various tasks across different production roles boosts efficiency and optimizes resource utilization. As we continue to expand with several new production facilities, the aim is to extend this program to even more skilled workers.
Bredo Larsen, HR Director at Kongsberg Defence & Aerospace, is clear about why this vertical integration is important:
"This arrangement enables skilled workers to take on more responsibility and serve as an important link between operators and supervisors."
"The arrangement allows them to stay closely connected to their core profession while maintaining a close involvement with the operations, applying their expertise across a broader range of tasks. This creates a more flexible and capable workforce, ensuring we maximize the experience and knowledge of our skilled workers to its full potential.”
The provision enables skilled workers to take on a wider range of roles. This makes it easier to implement both technological- and process improvements, as those closest to production are often the most equipped to spot improvement opportunities and have a firsthand understanding of the challenges.
A good example of this is the improvement work within surface treatment, where skilled worker Ingrid Jensen has played a pivotal role. Thanks to these efforts, the production time for the Naval Strike Missiles and the Joint Strike Missiles have been streamlined, saving the equivalent of four full-time positions per product—an essential improvement in a time of growth and expansion.
Jensen joined the program a year ago and today she works as a methods technician, where she is involved in training and contributes to the implementation of new work procedures. In her new role, she functions as a bridge between production and process, fostering greater collaboration between different technical teams. And she thrives with her new tasks.
"This opportunity gives us, as skilled workers, greater ownership in the improvement processes and encourages more effective collaboration across disciplines. This makes the implementation of improvements significantly easier and more efficient than before," says Jensen.
Rune Sundt Larsen, leader of the “Fellesforbundet” Company Union, emphasizes the importance of the arrangement in expanding career opportunities for skilled workers:
"The provision ensures that our members can take on a wider range of tasks, strengthening career paths and increasing the attractiveness of skilled worker positions. This allows for better utilization of the Technical Vocational School and its programs, and it promotes professional development initiatives that strengthen both the company and our employees."
The workforce of the future
Norwegian industry is facing a growing challenge in recruiting skilled workers for the years ahead. This provision plays a key role in attracting the next generation of talent by offering a career path that allows workers to continue their professional development without stepping away from production. At the same time, it maximizes the return on investments in new and advanced technologies, many of which are currently underutilized.
Markus Redalen Johansen, a process technician in Manufacturing Engineering, exemplifies how the arrangement can elevate internal talent. Starting as an operator on the NSM missile production line, he has now assumed responsibility for overseeing the processes related to the products he initially worked on. Through cross-disciplinary collaboration with a team of operators and engineers, he focuses on optimizing processes and resolving deviations.
"As an operator, my familiarity with the products makes it easier for me to address deviations and recommend process and design improvements. I also have the ability to step in, troubleshoot, and test the improvements myself, which saves time and gives me a comprehensive understanding of both the process and the final result," says Markus, adding that he is very pleased with the development opportunities provided through the program.
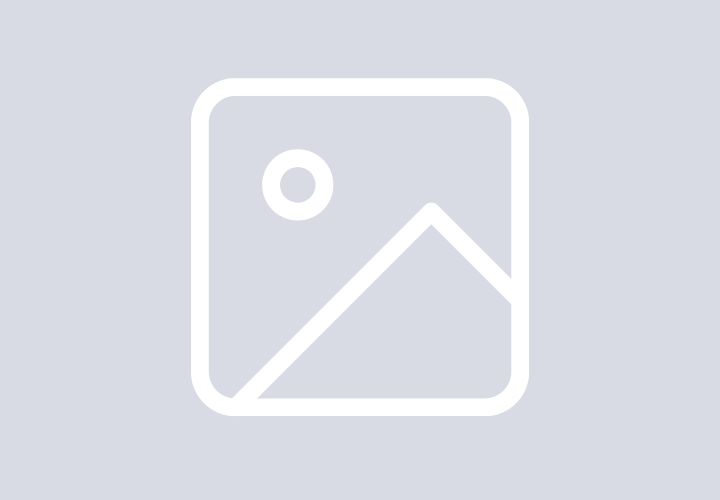
“We recognized a gap in our operations, so being able to promote individuals who are already familiar with the job, the environment, and ‘speak the same language’ has been a major advantage. The improvement initiatives led by Ingrid in close collaboration with the department, have reduced the learning curve for several surface treatment processes in our missile production by up to 70%,” says Production Manager for Assembly, Amund Biti-Johansen.
A competitive advantage
The agreement provides Norwegian companies with the opportunity to modernize their operations while giving skilled workers a more defined career path within production. This drives both productivity and the attractiveness of Norwegian industry, key to securing future growth.
"This represents a historic development in our collective agreement. It gives skilled workers greater flexibility and the ability to influence processes—crucial factors in strengthening the competitiveness of Norwegian industry moving forward," concludes Bredo Larsen.
For KONGSBERG and other companies in Norwegian industry, this arrangement could be a pivotal catalyst in meeting the future demands for efficiency, technological innovation, and professional development.