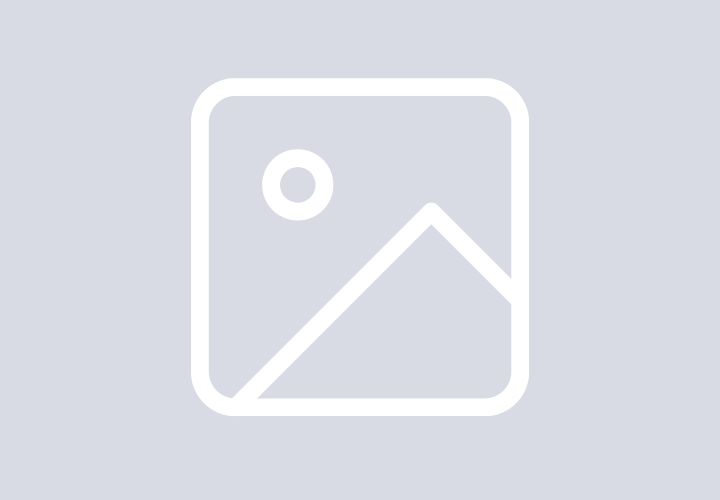
Triple Redundant Dynamic Positioning System
Triple Redundant Dynamic Positioning System
The K-Pos DP-31 and DP-32 are triple-redundant DP control systems comprising a triple-redundant dynamic positioning system controller unit and three identical operator stations. The controller unit and the operator stations communicate via a dual high-speed data network. Both systems satisfy the requirements of IMO Equipment Class 2 and corresponding class notations.
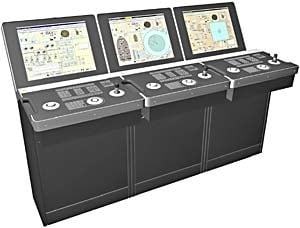
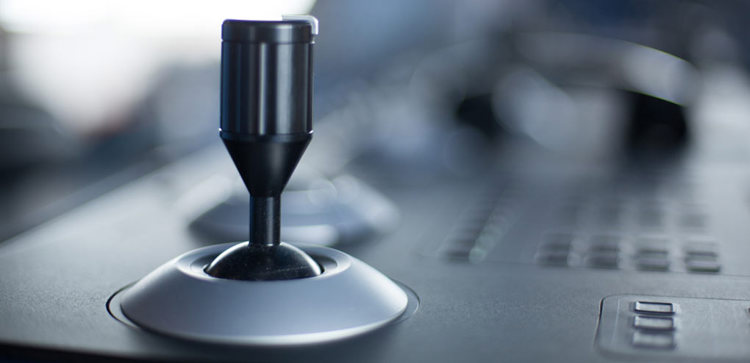
K-Pos DP-31 dynamic positioning system
The DP31 provides a direct interface to the propellers, thrusters and rudders, and includes the necessary interfaces to power plants, position-reference systems and sensors.
K-Pos DP-32 dynamic positioning system
The DP-32 is designed for integration with K-Chief (marine automation system) and K-Thrust (thruster control system) via a dual Ethernet LAN. Dual redundancy is also built into the interface units for connection of sensors and position reference systems.
Integrating all the functions for monitoring and control of a vessel provides a real benefit both technically and economically. Functions are integrated to reduce the overall need for hardware and software functions and to reduce interfacing requirements. This leads to less demand for special software, cabling and testing. Furthermore, integrated systems offer a far greater degree of redundancy, and therefore increased system availability and operational performance.
Purpose of voting
- Detect local interface errors in each controller
- Detect sensor errors such as compass drift and sensor breakdown
- Ensure that all three computers use the same data as a basis for calculations of command signals and that the command signals are equal from the computers
Triple redundancy advantages
- Voting of sensor input signals. The voting is performed between tightly synchronised computers to detect sensor errors such as compass drift and sensor breakdown and ensure that all three computers use the same data as a basis for calculation of command signals
- Software Implemented Fault Tolerance. The Triple Modular Redundancy (TMR) detects an error in the processing elements and corrects the error by employing voting algorithms. The system represents a Software Implemented Fault Tolerance (SIFT) concept
- Voting on command (output) signals. DP-31: The thruster commands from the three control computers are compared by the “master” computer and the median command is selected to be the final output. DP-32: The voting of the thruster commands is performed in the thruster control field station
- No single-point failure. The system is designed to avoid total system failure if single failure occurs
- Failure detection. The system will detect a failure, allowing corrective action to be taken
- Fault isolation. If one system component fails, the other components will not be affected
- No standby unit, all computers are "hot". If one DP control computer fails in a triple-redundancy system, the two other computers continue working and perform dual-redundancy procedures in the same way as a dual system. Should a second computer failure take place, there is an automatic switch-over to the remaining computer
- Hot repair. It is possible to replace a computer while the other computers continue the operation
DP class notation
The K-Pos DP-31/32 with DP-11/12 dynamic positioning system meet the Equipment Class notation for Class 3 dp systems. The K-Pos DP-11/12 is used as backup.
Dynamic positioning operator interface
The operator interface is designed to allow efficient and safe operation of the dynamic positioning system by assisting the operator in making optimum operational decisions.
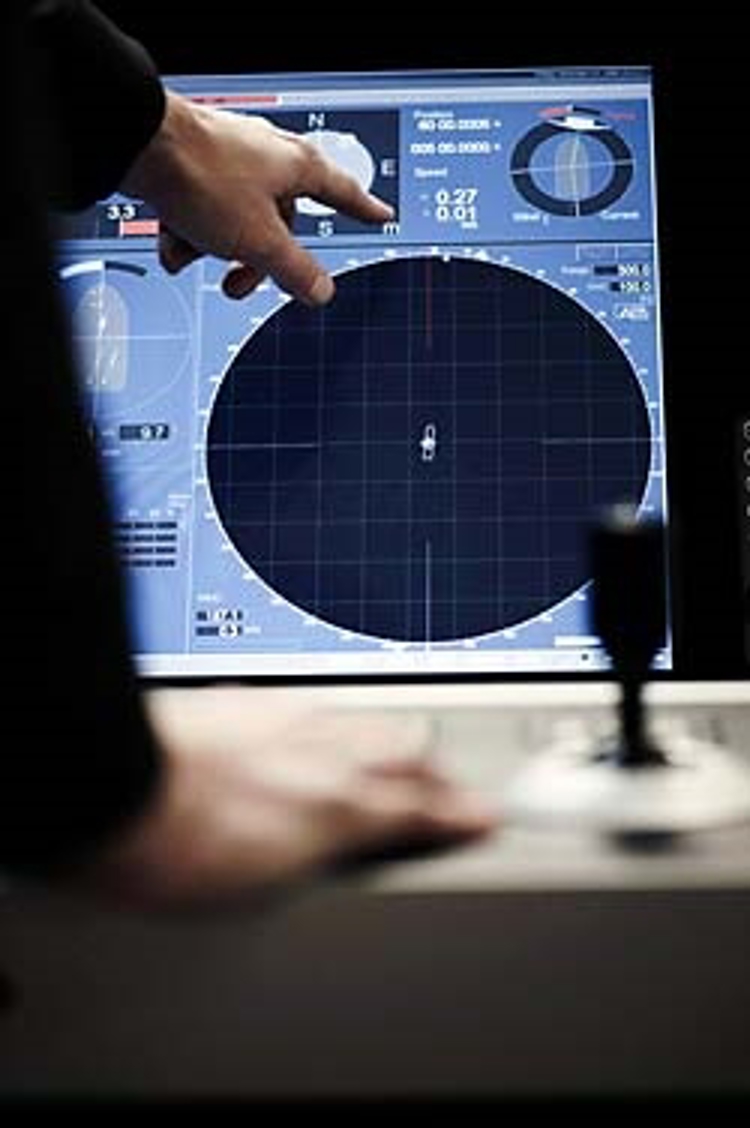
Related information
Lifecycle support for your vessel
-
24/7 Technical support
Our 24/7 technical support team is there to help at any time, day or night, wherever your vessel is.
-
Conversions, retrofit and refit
Upgrading and enhancing your vessel’s performance.
-
Training
Maximise crew efficiency and reduce downtime with expert training.