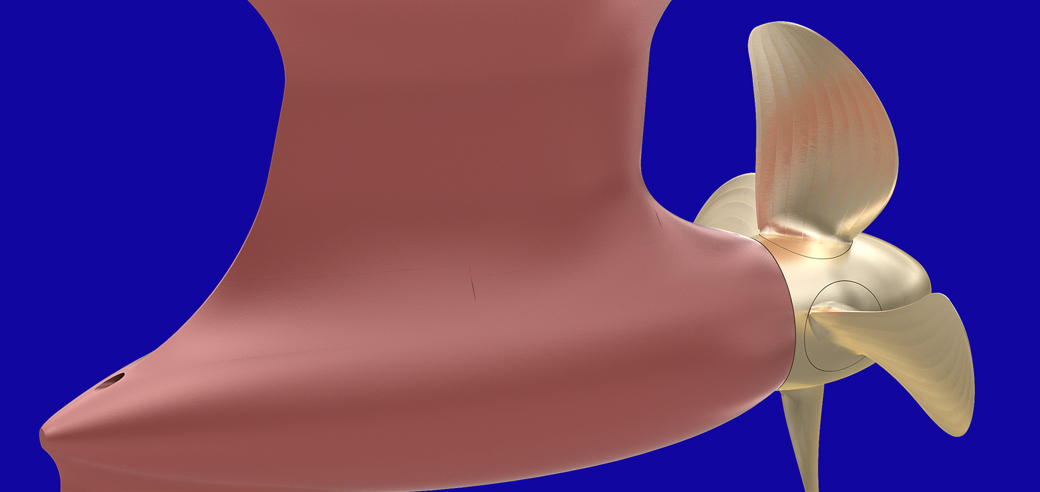
Cruise control
Hurtigruten’s new expedition cruise ships will feature what is possibly the world’s most efficient propeller system.
Possibly the world's most efficient propeller system
New Azipull PM electric motor largely uses the same underwater unit as before, but is equipped with a vertically-axled PM motor that’s integrated into a new upper unit.
The Kleven Verft shipyard in Norway is building two environmentally friendly expedition cruise ships for Hurtigruten, the company that operates Norway's iconic coastal ferry service from Bergen to Kirkenes.
In addition to a hybrid power system, their main propellers represent a green innovation, one that will provide both environmental and financial benefits.
The new vessels, MS Roald Amundsen and MS Fridtjof Nansen, will be powered by our hybrid system, which combines batteries with highly efficient diesel engines. The environmental gains increase even more when you take into account the propulsion system. With a 4 per cent higher efficiency rate – 10 per cent at lower speeds – Hurtigruten stands to achieve major savings.
Building on experience
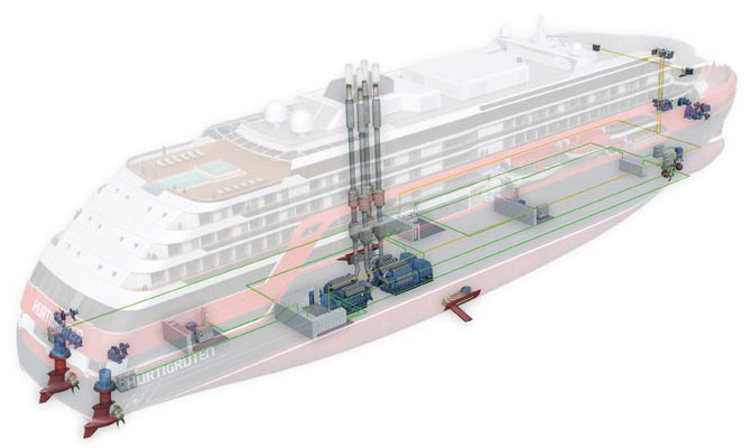
Each of the ships will be fitted with two Azipull main propellers from us that have been further developed to incorporate permanent magnet (PM) motors. Azipull thrusters are pulling propellers, housed in a streamlined underwater unit, and have been providing effective propulsion and manoeuvring for various types of vessels since 2003.
To date, we have produced 550 of these units in Norway. They operate either by direct mechanical transfer or are powered by a separate electric motor in an electric, gas, hybrid or battery-driven system. The introduction of PM technology has made them even more efficient.
The new Azipull-PM has been on the market since 2017. It is configured for L-drive operation, which largely uses the same underwater unit as before, but is equipped with a vertically-axled PM motor integrated into a new upper unit.
"The new PM electric motor has an extremely high-efficiency rate over a wide range of rotational speeds," says André Landes, Product Manager for Azipull PM at Kongsberg Maritime. "Excellent hydrodynamic efficiency, along with lower mechanical losses with the new PM-L driveline, make a really profitable combination."
Super Premium Efficiency
The amount of space required in the thruster room is also reduced because the new thruster is compact. The PM motor lies within the diameter of the housing, which avoids the complicated wiring and anchoring of the separate motor needed with a conventional Z- or C-drive electric configuration.
André adds: "Typical areas of application will be offshore supply and service vessels, support ships, offshore stand-by ships, coastal tankers, car and passenger ferries, as well as cargo vessels and cruise ships."
The new Azipull 120 PM motor was recorded as operating at a 98.6 per cent efficiency rate during recent joint tests by Hurtigruten, Kleven and DNV GL. This means that the Azipull 120 PM motor is classified as meeting the highest international standard for energy efficiency for electric motors, IE4 – Super Premium Efficiency. In the new L-configuration, the top gear and the classic induction motor has been replaced by a top-mounted PM motor. In tests, the latest edition of the AZP120-L has demonstrated an improved efficiency rate of around 4 per cent at nominal and more than 10 per cent at low loads. Also, removal of the top gear has made the motor much quieter.
"This is a fantastic result, our team has supplied Hurtigruten with two of the world's best electric motors. We have never seen commercial motors of this output and speed class with such a high efficiency rate."
Although the vessels' actual performance profile will not be known until they have been in operation for a while, the basic data from another Hurtigruten ship, Fram, shows that the propellers generally operate at partial load, where the new solution is particularly favourable.
Initial calculations for typical operations in Arctic areas show that it could be possible to save around £70,000 (NOK 750,000) per year in fuel costs.