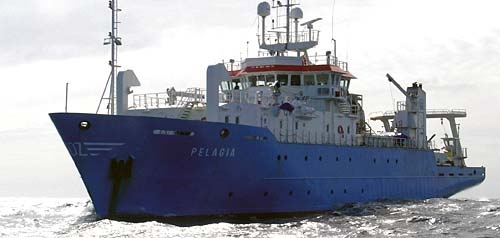
As knowledge about the seas increases, scientists need to be able to place their sampling and other equipment with ever increasing spatial accuracy on the seabed. The sea bed shows high variability and it is essential for proper data interpretation to know exactly where the samples are taken, underwater video surveys are carried out and frames with various measurement and sampling equipment (so called landers) are placed. To support this, it was decided that during the midlife overhaul of the vessel in 2010 an underwater navigation system should be installed.
Various suppliers of this type of equipment have been asked to present the pros and cons of their systems. The main criteria that played a role in the final decision were: maximum working depth (most of the NIOZ equipment is designed for 6000 m water depth, so the transponder should be depth rated to 6000 m as well), a large range to be able to find free floating landers at depth, deployment on a pole from inside the ship, size of the transducer head (it should fit in between the frames when hoisted in), ease of integration with the existing ships navigation and attitude sensors, ease of handling of the transponders and the price.
After thorough consideration it was decided to install a Kongsberg HiPAP®101 with cNODE® Mini transponders. The system has been working well since the final sea acceptance test was successfully carried out.
Once installed and people are familiarised with it, the system proves easy to operate. However, because the R.V. Pelagia is a multipurpose vessel, the HiPAP® is not used during every cruise. This means that not everybody sailing on the ship is an experienced user, sometimes resulting in some typical user errors. To avoid this, a manual containing numerous photographs and screen shots explaining the standard operational procedures was made. With this manual at hand, standard operation is straightforward, also for the non-experienced user.
Last December the HiPAP® was used during piston coring activities. A piston corer is a device designed to retrieve several metre long sediment cores from the seabed. It consists of a long (in this case 12 m) steel pipe with a heavy weight (1.5 metric tons) on top, and a release mechanism that allows for a free fall when lowered near to the seabed. In this case the core was used for paleoceanographic studies.
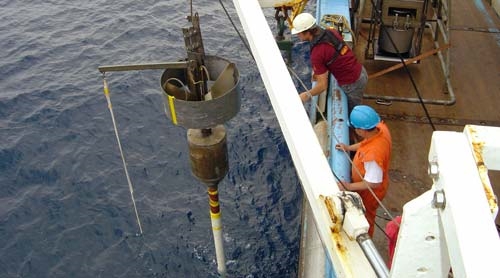
The coring activities took place on the Nares Abyssal Plain (Atlantic Ocean), about 300 nautical miles northeast of Puerto Rico. The target in the 5.8 km deep ocean was the top of an approx. 250 m high narrowly crested ridge. The target was an area at the crest with a diameter of 50 metres. During the preparation of the coring activities the cNODE® transponder was attached to the coring cable by means of a custom made bracket. In order to avoid any possible damage to the transponder during release of the corer (at the point of release tension in the Super Aramid cable causes jolting of the release mechanism) the transponder was attached 60 metres above the corer. This distance had to be taken into account when calculating the distance of the corer to the sea floor. At the moment the corer had penetrated the seabed, the HiPAP® gave a depth of the transponder of 5489 m below sea level. When the 60 m height difference mentioned above is taken into account, this would mean that the top of the corer, which is at the seabed after the corer has fully penetrated the sea floor, should be at a water depth of 5549 m. This coincided very well with the water depth as measured by the on board EM302 multibeam echo sounder, which was 5548 m. Later measurement on deck revealed a total core length of over 10 m. This and the fact that the weight on top of the corer was covered in mud indicates a complete penetration of the corer. This supports the conclusion that the HiPAP® system gave a reliable indication of the transponder depth of 60 m above the sea floor.
Although the HiPAP® indicated that the corer was subject to lateral drift due to variable currents encountered during the descent through the more than 5.5 km deep water column, it turned out to be fairly easy to manoeuver the ship in such a manner that the corer could be placed well within the 50 m radius target area. The corer penetrated the seabed 36 m from the centre of the target. Keeping in mind the horizontal accuracy of the HiPAP®101 of less than 0.2% of the range, this means that the core was taken within the projected target area, so on the narrow crest of the ridge. This was important in order to avoid any possible disturbed sediment due to gravitational processes that are likely to occur on the slope of the ridge.
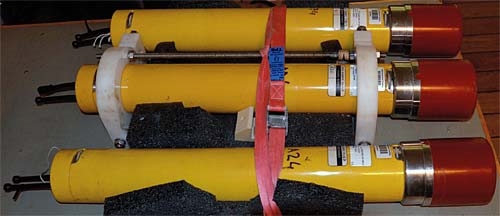
In summary: The HiPAP® system is straight forward to operate during standard underwater navigation operations. Having a ‘pictures cook book’ at hand makes operation easy, also for non-experienced users. The cNODE® mini transponders are mechanically robust. In addition to piston coring, they have been installed on various other types of equipment (video frames, other coring equipment, CTD), also during rough sea conditions. Collisions of these devices against the hull did not affect the functioning of the transponders.