Kongsberg Maritime developed AUV, instruments and software combine for high performance survey.
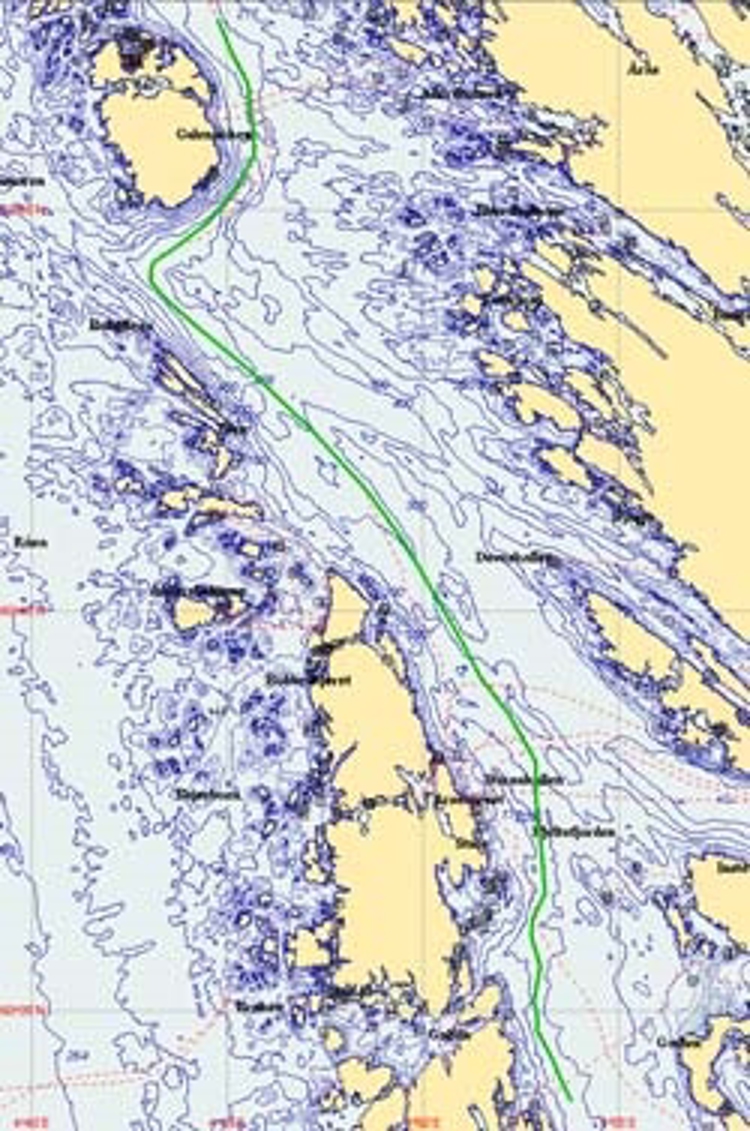
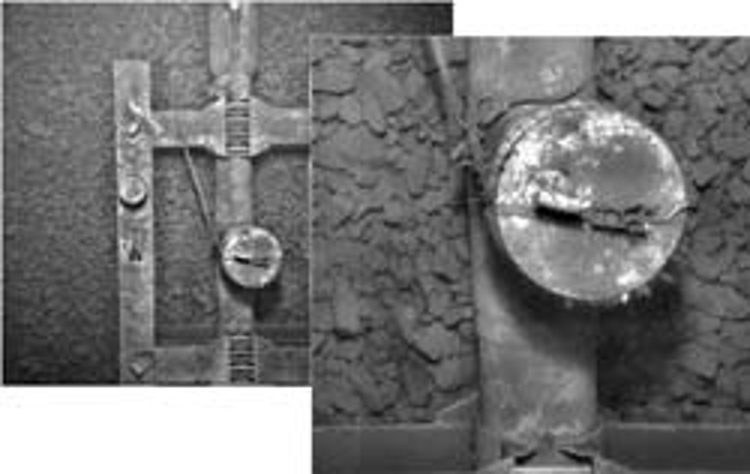
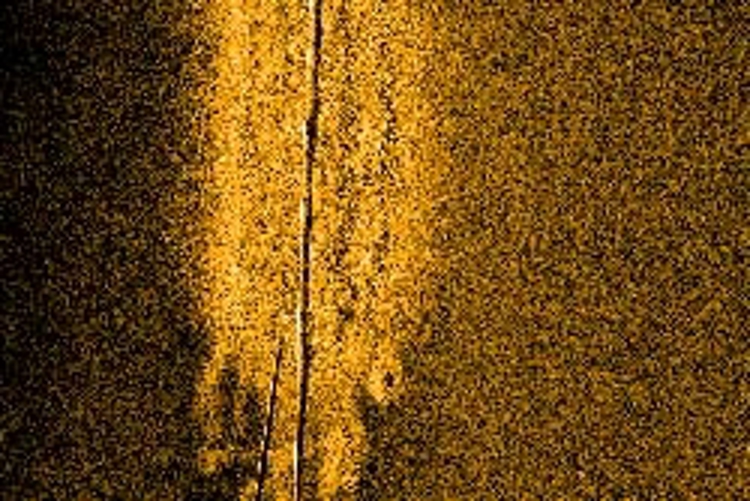
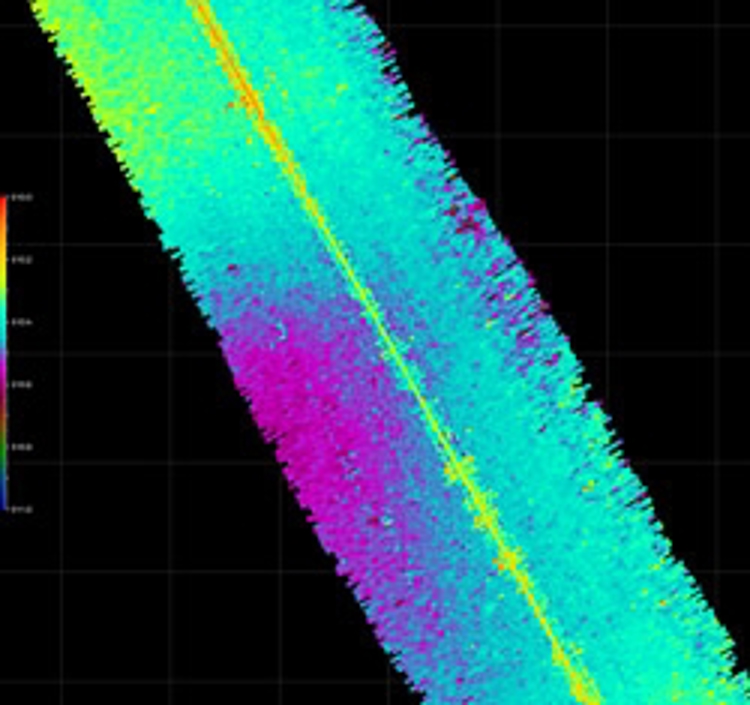
KONGSBERG has completed the world's longest multi-sensor AUV pipeline survey using one of its cutting-edge HUGIN Autonomous Underwater Vehicles (AUV). The pipeline inspection took place February 9th – 11th 2011, in the Hjelte fjord near Bergen, Norway and the HUGIN was operated from the Royal Norwegian Navy vessel HNoMS Maloy.
The subject of the inspection was two subsea pipelines going to the Mongstad oil refinery. The HUGIN AUV was equipped with a an advanced suite of KONGSBERG imaging equipment including the HISAS 1030 synthetic aperture sonar, EM3002 multibeam echo sounder and an optical camera with LED lighting. The instruments were used to inspect around 30 km of subsea pipeline in an 8-hour, two-pass mission.
In the first pass, side-scan data from the HISAS 1030 sonar was used to detect and track the pipelines in real-time, using PipeTracker software for pipeline detection and tracking extracted pipe-like features in the sonar images, with a high degree of robustness towards false detections.
The PipeTracker software, which was developed in a collaborative effort with the Norwegian Defence Research Establishment (FFI) in a project funded by the Norwegian Research Council, runs as a plug-in module in the standard HUGIN payload system. The HUGIN control system in turn uses the identified pipeline tracks to position the vehicle at an optimal range for HISAS imaging. The whole process is fully automated inside the AUV and requires no operator intervention.
In the second pass, HUGIN followed the pipeline tracks identified in the first pass at low altitude and inspected the pipelines using the EM 3002 multibeam (now available as the more modern EM 2040) and the optical camera. After the mission, the recorded HISAS 1030 data was post-processed into high-resolution (4x4 cm) sonar images and bathymetry maps of the pipeline. Together with the optical images and the multi-beam data recorded in the second pass, this gave a detailed view of the pipeline surroundings and the pipeline itself. The complete procedure was repeated the next day over the second pipeline in a new 8-hour, two-pass mission.
Both pipelines were surveyed at a constant speed of 4 knots and at 4-25m altitude, depending on the sensor in use. Water depth was 180-560m. The greater speed of the HUGIN compared to that of a ROV meant that 60km of pipeline could be inspected in a little over 16 hours during the two passes. Furthermore, the stability of the HUGIN platform and the ability to simultaneously operate both at high speed and at low altitude resulted in an efficient survey with crystal clear images from the onboard optical camera.
Kongsberg Maritime and subsidiary Hydroid offer 'Full Picture' HUGIN and REMUS AUV solutions, where the vehicles themselves and required instruments can be supplied by Kongsberg Maritime, ensuring users have a single company to co-operate with for any kind of survey. The company is aligning the two product lines, providing users operational synergies and a strengthened technology base, suitable for all underwater survey applications. The PipeTracker software module has been developed in a collaborative effort with the Norwegian Defence Research Establishment (FFI) in project funded by the Norwegian Research Council (the FORNY-program).