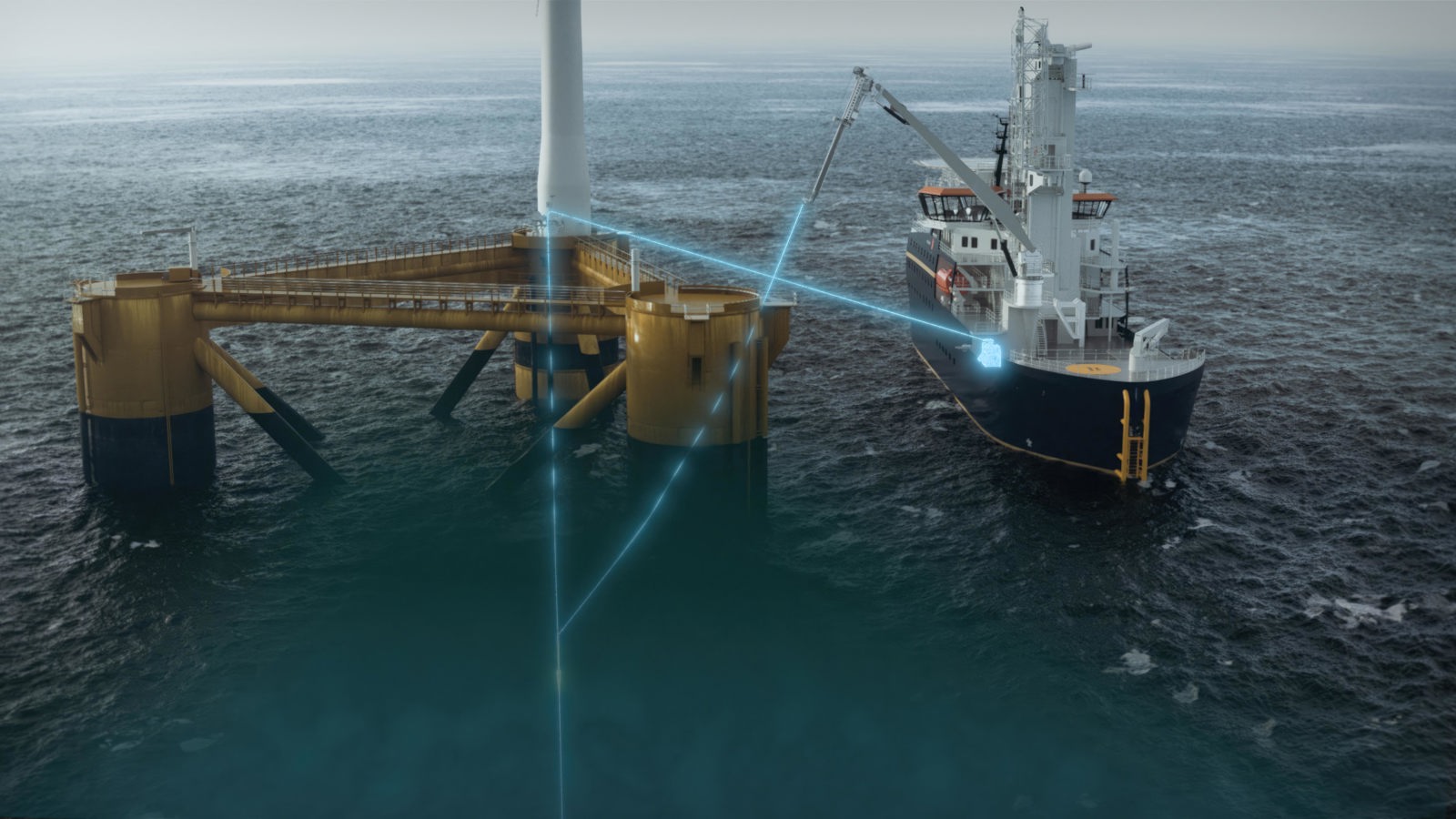
Power of integration
A new, patented Kongsberg Maritime method for dynamic cable pull-in operations enhances safety and efficiency by reducing the need for heavy equipment and personnel on the floaters.
-
Text:Global Sales and Marketing
Photo:©Kongsberg Maritime
-
Craig TaylorSenior Manager PR & Communications
Kongsberg Maritime has developed an innovative method for cable pull-in operations that promises to improve the way the inter-array cables are pulled in on floating wind turbines.
This new approach from the Advanced Marine Operations (AMO) department in Kongsberg Maritime not only enhances safety and efficiency but also extends the operational window to all year-round. At present, in what is a relatively new industry, cable pull-in operations require mobilising equipment such as winches, power packs, fuel tanks and sheaves on the floater (the floating wind turbine). Personnel must be on board the floater after it has been hooked up to perform the cable pull-in. However, the new, patented Kongsberg Maritime method reduces the need for personnel and eliminates the need for heavy equipment on the floater. Instead, all necessary equipment is placed on the vessel, significantly reducing the complexity and risk associated with the operation.
-
All stages executed from the installation vessel set in Dynamic Positioning and under Remote Monitoring
-
Cable pick-up
First, the vessel moves towards the floater with
the end of the pre-installed cable. The method
may also be used in a direct installation. -
Vessel moves cable towards floater
Positioning ready for connection. -
Winch line connection
The Remotely Operated Vehicle (ROV) picks
up the winch line connected to the pre-thread
line and attaches it to the cable’s pull head.
Gunnar Thorsen, Kongsberg Maritime’s Senior Vice President of Business Concepts, explains: “What we have developed is a method where all active machinery is on the vessel, providing it has DP2 capability. This is a totally different way of doing things.”The operation involves a hand-carried, mobile instrument package being installed on board the floater that communicates with the vessel. A pre-thread line runs through the guide tube on the floater and a winch on the vessel equipped with a processing unit manages the data from the floater about its real-time motions and position. The system compensates for relative movements between the floater, the cable and the vessel.
Gunnar Thorsen, Kongsberg Maritime’s Senior Vice President of Business ConceptsAll active machinery is on the vessel, providing it has DP2 capability. This is a totally different way of doing things.
The operation involves a hand-carried, mobile instrument package being installed on board the floater that communicates with the vessel. A pre-thread line runs
through the guide tube on the floater and a winch on the vessel equipped with a processing unit manages the data from the floater about its real-time motions and position. The system compensates for relative movements between the floater, the cable and the vessel.
Gunnar elaborates: “We have developed a highly accurate system that automatically instructs the winch on the vessel to take out relative movement between the floater and the cable, and between the vessel and the floater. With that method, we can do the pull-in operation in bad weather, extending the operational window.”
The dynamic cable pull-in system is used to connect inter-array cables.
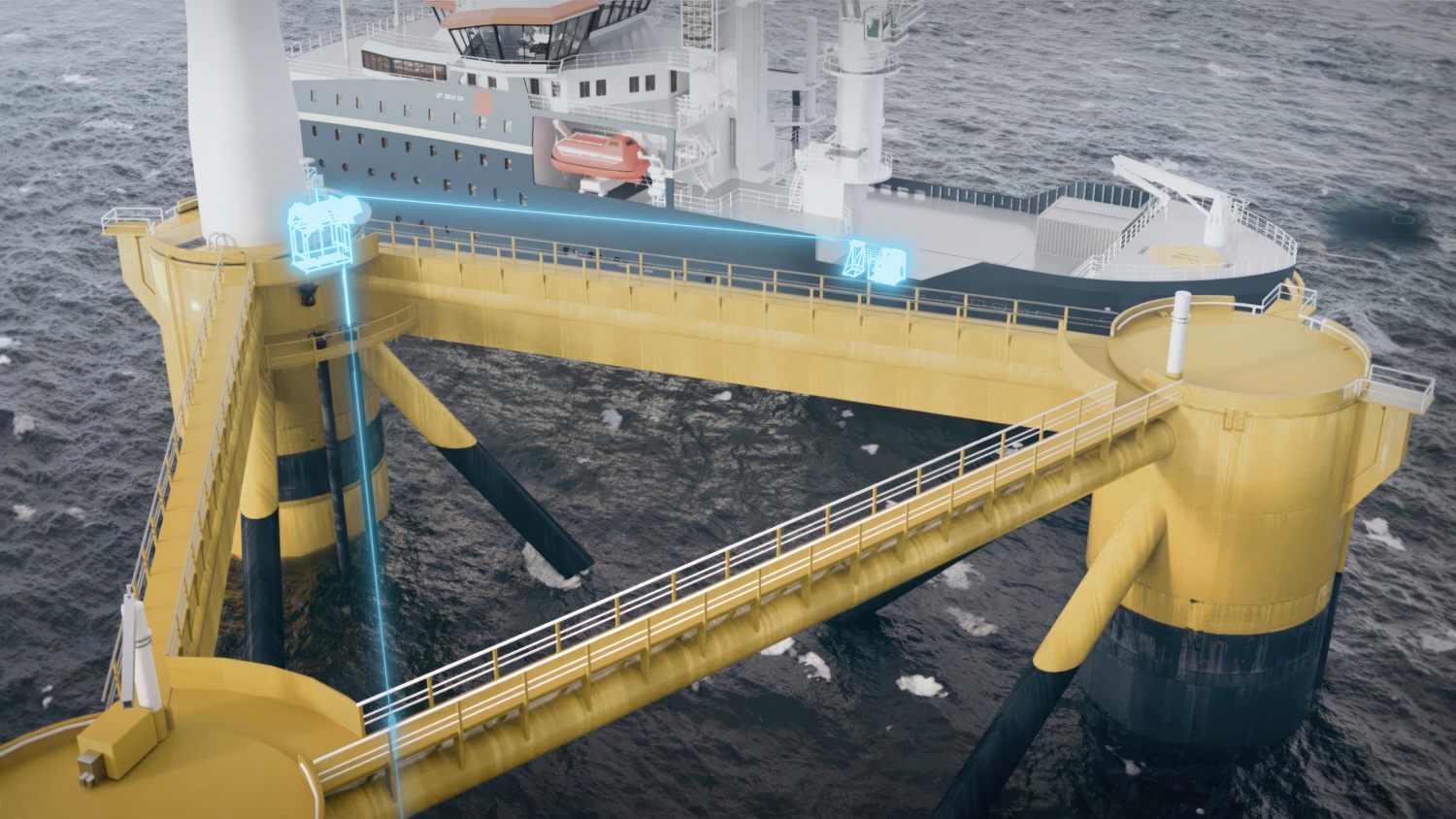
At a glance: key benefits
- Eliminates the need for heavy equipment installed on the floater
- Enhances safety by reducing personnel requirements on the floater
- Both extend the operational window
- Simplifies the cable pull-in process
- Supports the industrialisation of floating offshore wind operations
The step-by-step method shown below offers several advantages, including enhanced safety by reducing the need for personnel on the floater during the pull-in operation, and speeds up the overall rate of installation of the wind farm array.
Ottar Antonsen, Kongsberg Maritime’s VicePresident Business Concept and Advisory, highlights the broader implications: “We offer the full package of equipment and technology, from the point the floating turbines leave their construction site, up to the point at which the turbines are connected to the power grid and local substation, and everything in between.
“As the floating offshore wind market expands globally, with regions such as Taiwan, Japan, Korea, Europe and the Americas adopting this technology, the need for an industrialised process becomes evident. “We see that the way we do it today, using several types of vessels, might be okay in the North Sea where we have a well functioning oil and gas spot market. However, with floating wind being adopted globally, areas without oil and gas activity will require a different approach, with vessels designed and built for this specific role.
“Our innovative cable pull-in method is the final part of a new holistic solution to the industrialisation of floating wind installation. Together with our new approach to tow-out, anchor tensioning, mooring and hook-up, we are offering a full solution that represents a big leap forward. This range of methods will enhance safety, efficiency and operational flexibility, and support the rapid growth of this vital renewable energy source.”
-
Load transfer
The load is transferred from the crane to the
winch, and the instrument package on the floater
is activated to communicate with the vessel. -
Pull-in operation
The winch compensates for heave and other
movements between the floater and the vessel,
allowing the cable to be pulled in and hung off
the hang-off system on the floater. -
Disconnection of the pull-in line
Releases the load on the winch and
disconnect line, which can be recovered
and reused later.