
The need for regulatory compliance is a challenging one for ship owners. While switching to low-carbon fuels is an option for some, what if conventional fuel is preferred as the way forward? Is compliance still achievable?
Kongsberg Maritime has looked at the way in which a conventional fuelled ship can be combined with a range of complementary technologies, and the answer to the big question about compliance is ‘yes’. Two scenarios were examined, with fuel cost savings of 44 and 56 per cent depending on operation.
-
Text:Global Sales and Marketing
Photo:©Kongsberg Maritime
-
Craig TaylorSenior Manager PR & Communications
Kongsberg Maritime combined conventional ships with new technologies, achieving compliance and fuel savings of 44% and 56%, depending on operation.
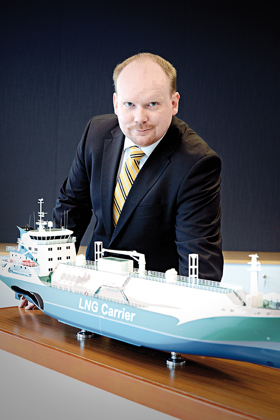
Oskar Levander, Vice President Strategy & Business DevelopmentOskar Levander, explains how a ship using conventional fuels can meet future compliance targets, with the addition of energy saving technology.
There are many ways in which ship owners can tackle the prospect of tighter regulation. The easy part is agreeing that all of these new technologies have something to offer.
“However, the difficulty lies in how to apply this to a vessel knowing that your investment choice will need to remain relevant for decades of operation,” says Oskar Levander.
“The fundamental target here was to design a vessel that could comply with the predicted CII (carbon intensity indicator) regulations throughout its lifetime.
“For this study, we decided to look at a vessel with global operations. We settled on a bulker as the basis of a new concept. To represent a common vessel size, we selected a Kamsarmax bulker of 82,000 DWT. It also represents a vessel type for which a switch to an alternative fuel could become restrictive, in terms of global availability of low-carbon bunker fuels.”
Kamsarmax is a medium-sized vessel that could traditionally fit through the old Panama Canal and access the port of Kamsar in West Africa. Today, it is more a maritime term for a bulker of this capacity.
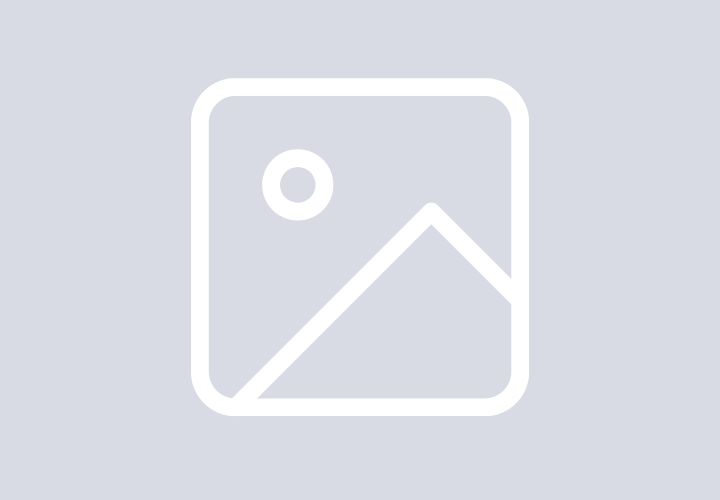
Add-on tech for big results
With the vessel size agreed, the Kongsberg Maritime team, working alongside ship designers Deltamarin, looked at available technologies and savings they would bring to typical Kamsarmax operations. Oskar says: “We have one of the largest technology portfolios, so we looked at what we could bring to the table. We also researched the other manufacturers that offer energy-saving systems, such as wind sails and air lubrication.”
The result is a new vessel design that is known as the ‘Super-Efficient Bulker’. The study compared this vessel in two operational profiles, both based on 12 months of operation. One scenario looks at a vessel in global operation, without a fixed route where wind calculations look at an average.
The second was a more focused study of a regular transatlantic operation between Rotterdam and Sept-Îles, Quebec. In this scenario, with more favourable wind conditions, the vessel performed even better with estimated savings of more than 50 per cent.
In order to achieve significant savings in fuel, there are several features on the ship that each contribute to the significant fuel savings. One of these is the operation of the vessel itself. Oskar says: “Slow steaming is becoming a more popular choice for many ship owners. There is a clear realisation that by slowing down you can cut fuel and emissions, and reduce maintenance costs, too. However, many ships have already reduced speed and you do not want to slow down too much as the earning potential is reduced. In this case, we assumed a 1 knot speed reduction.
“Next, we looked at one of the major contributors – wind technology. There are a lot of options, but we chose to have a different approach to what we’ve seen in this space to date. All manufacturers, be that those making wing sails or rotors, only offer their own solution and each solution works well in specific conditions. For example, a prevailing headwind gives better results with a wing sail, while rotor sails give maximum benefit in side winds. However, we must remember that there’s nothing constant with wind.
“What we chose to do was equip this vessel with two types of wind-assist technology, in order to get the best of both. So, instead of installing five of one type we have opted for three Flettner rotors and two suction wing sails. The combined wind propulsor setup results in larger savings compared to either wind technology being used on its own. The three rotors in the middle are also tiltable to aid cargo handling.
“The other significant driver of fuel saving is the use of air lubrication, a system where air bubbles are pumped out at the bow and spread out along the length of the ship reducing resistance between water and the hull. This technology is becoming more popular on larger ships with flat bottom hulls; however, no vessel has yet been able to capture the full potential of this technology. In conventional bubble systems, the bubbles ‘escape’ quickly towards the aft and to the sides, as the vessels move over them, meaning that a lot of air needs to be continuously pumped below the hull. Concepts with an air cavity below the hull that trap the air have been tested at model scale, but there are technical complications to get it to work correctly.”
New hull is a design innovation
To address these shortcomings, Kongsberg Maritime has devised an innovative hull form that will trap bubbles, to maximise the effects of resistance reduction. The key features of the design are a sloping hull, where the bow is slightly higher in the water than the stern, at an angle of around 1 degree. The inclined hull slows down the movement of air bubbles making them stay longer below the hull. Combined with the slope, the bilge keels, running along each side of the hull, are turned down in the vertical creating ’walls’ to keep bubbles beneath the ship reducing the air consumption.
In addition, the hull is made wider to enlarge the bottom of the vessel where the air lubrication is effective and reduces the hull side area where the air does not have an effect.
Oskar adds: “The optimum dimensions for a hull with air lubrication are not the same as for a vessel without.”
The wider hull does come with a small impact of bare hull resistance, but the saving with air lubrication is bigger. In addition, the wide hull also makes it possible to have the same DWT despite the inclined hull, with a lower draft forward.
Oskar explains: “With the new aspects of the hull form, you can really get the best from air lubrication and make game-changing savings, through reduction of frictional resistance. The estimated net saving from the new air lubrication is about double compared to a conventional hull arrangement with air lubrication. Couple that with the savings gained from wind power, slow steaming and smart management of energy on board, and you have a real alternative to the low-carbon fuel option.”
The Super-Efficient Bulker includes proven Kongsberg Maritime technology. The Hybrid Shaft Generator is a large shaft-mounted PTO (power take out) with frequency control for improved efficiency and lower emissions. A PTO solution is ideal for this ship, as the electric hotel consumption is much larger due to the electric motors needed for the wind propulsion devices and compressors supplying the air lubrication. An increase in hotel power occurs when the propulsion power is reduced, so taking the power off the main engine is the optimum solution.
Flexibility and fuel efficiency
The ship is further equipped with a controllable pitch propeller as they give flexibility when operating with wind and a larger PTO capacity. Energy is optimised through an Intelligent Energy Management System (iEMS) in combination with energy optimisation, and route optimisation software systems to get the best optimisation from wind and propulsion. Keeping the hull clean also contributes to reducing resistance, so a Hull Skater is also proposed.
“This project has been a real eye-opener for us,” adds Oskar. “While each element makes a difference, it’s the combination of these technologies where the real difference is made. The fuel saving calculations were determined through comparison with latest bulker designs, rather than an old vessel as the benchmark.
“The opportunity to reduce fuel costs by half compared to state-of-the-art conventional vessels, without the need to blend low-carbon fuels, is something I believe will be attractive to ship owners, particularly with the vessel size we examined. The Super-Efficient Bulker also offers a short payback of about five years, so the upfront investment is returned thanks to significantly reduced running costs.
“Wind and air lubrication are great technologies. At KONGSBERG, with our experience as an integrator, it means we can pull together the best technologies out there, along with our own, and offer something that could offer an alternative destination on the journey to cleaner, more efficient shipping.”