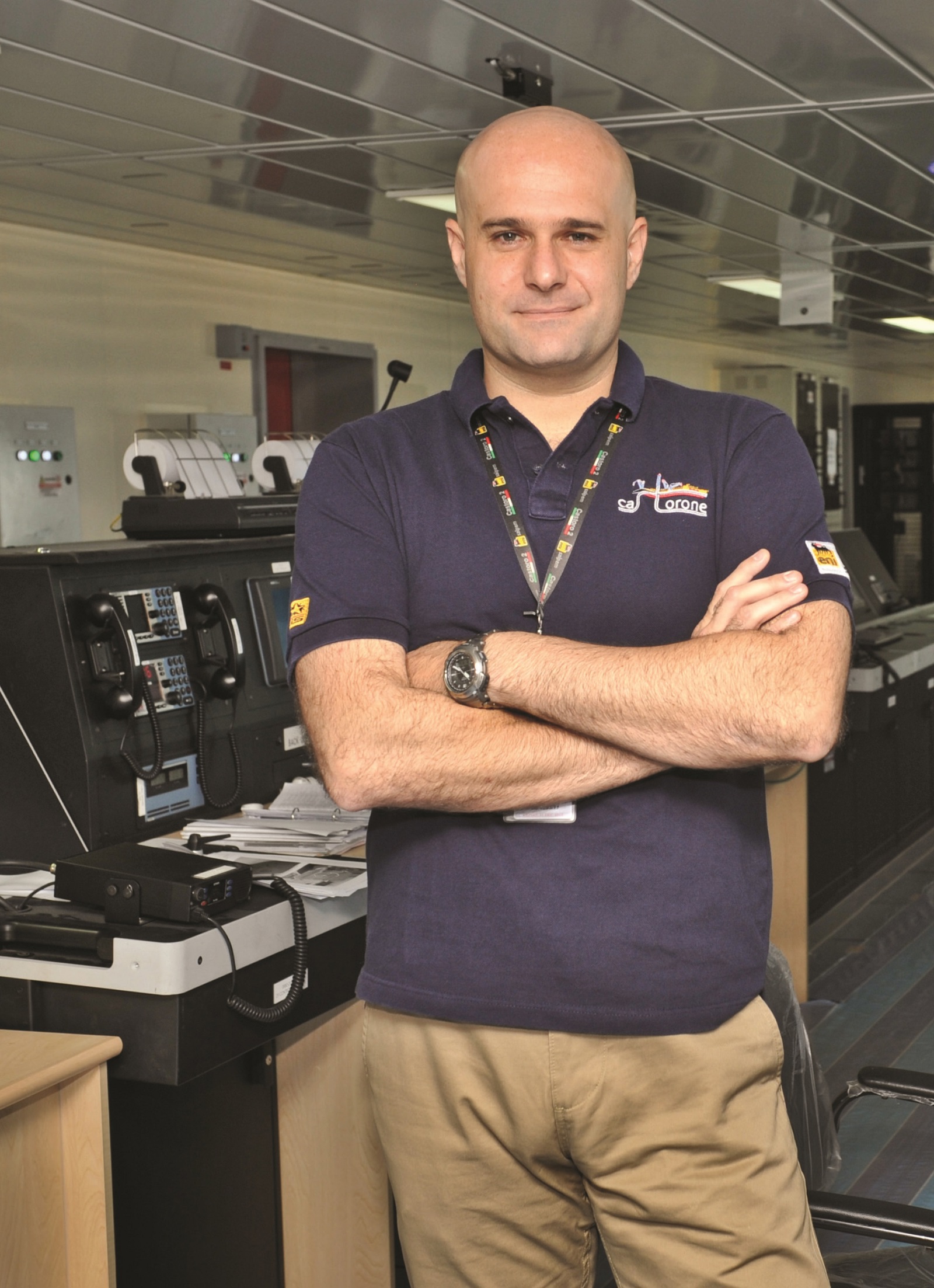
Saipem Goes Deeper with Castorone
Saipem’s new flagship vessel, the Castorone, is not only the largest vessel of its kind in the world. It can also lay pipes deeper, faster and in harsher conditions than any other pipelayer to date.
-
Text:Kongsberg Maritime Communication
-
Gunvor Hatling MidtbøVice President, Communications
The Full Picture Magazine was invited to visit Saipem’s latest new- building vessel, Castorone only a few days before its scheduled departure from Singapore. The vessel then underwent extensive sea trials, which lasted for several months due to the ship’s complexity. With its 330 metres in length, excluding the stingers, Castorone is an impressive sight and comparison to any other pipelayer is almost impossible.
“This has been a long process, but we are nearly there,” says Commissioning Manager, Fabrizio Fantacci, underlining that due to its complexity on several levels, the Castorone has taken no less than five years to complete.
“The concept design started back in 2006 in Milan. While the hull was initially built in China, it was brought to Singapore for final outfitting and commissioning in early 2012. During the busiest time of construction in Singapore, approximately 3500 workers were aboard on a daily basis, constituting 12 million hours of work during the project period in Singapore alone,” he explains.
PREPARING FOR FUTURE OPERATIONS
Castorone will replace Saipem’s Castoro Sei as the company’s new flagship pipelayer. As a world leader in the oil and gas contracting services sector, both onshore and offshore, Saipem has been operating within the industry for more than 60 years. After a period of low investment, Saipem made the decision to build a series of vessels and initiated an investment program in 2006. The program was aimed at reinforcing and expanding the company’s drilling and construction fleet in order to meet the future challenges of drilling in ultra-deep water. Castorone is the largest of these newbuildings both in terms of investment and vessel size. With this new asset in its fleet, Saipem wishes to be ahead of the curve both in terms of water depth capabilities, efficiency and environmental conditions.
“The market trend points towards deeper and deeper waters, and Saipem’s design strategy has followed this. With the S-lay stingers, the Castorone has the ability to lay pipes up to a water depth of 3000 metres. In addition, it is a DP ice class vessel, meaning that we can operate in Arctic waters, which is where we anticipate a big part of the future market to be,” explains Fantacci.
The vessel is currently fitted with stingers for S-lay operations. In two years time, however, a J-lay tower will be installed, enabling it to reach even greater depths. Another important feature is that the vessel will use new welding and field joint coating technologies, providing for future operations in the pipelaying industry. Instead of the usual two pipes, the Castorone can connect three pipes of 12 meters, resulting in more efficient and faster operations.
“Since the Castorone can lay triple joints, which means three pipe-lengths at a time, it can operate up to three times faster than a regular pipelayer and 50% faster than a double joint pipelayer. This new laying configuration is also a means of preparing for future operations in double joint configuration with pipes expected to be 50% longer than what they are today,” explains Fantacci.
Castorone also has a storage capacity of 20,000 tonnes of pipe, corresponding to approximately four days of operation. This means that it does not need to load pipes as often as a regular pipelayer. In case of extreme weather where it might be difficult for a supply vessel to approach the Castorone to transfer pipes, operations are not interrupted, something which ensures time and cost efficiency.
“The market trend points towards deeper and deeper waters, and Saipem’s design strategy has followed this” - Fabrizio Fantacci, Commissioning Manager, Saipem
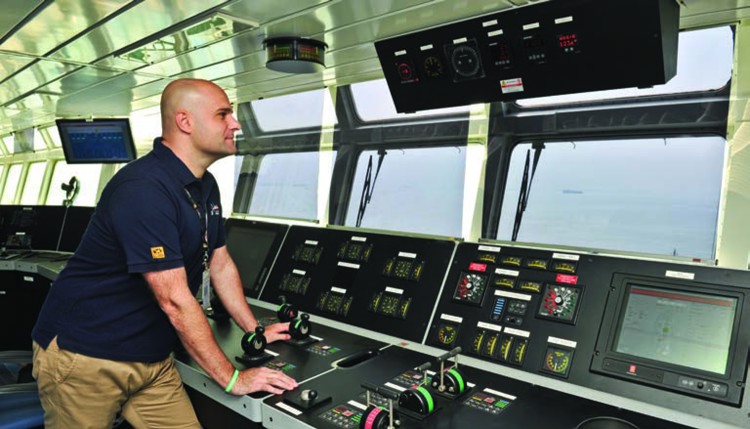
MAJOR CONTRACTS SECURED
Several contracts had already been secured well ahead of completion. The vessel arrived in the Gulf of Mexico in April 2013 for its first operation. Saipem has been awarded a contract for the transportation and installation of a 20 inch-diameter, 350km gas export pipe- line in waters ranging from 100 to 2100 metres deep. The contract is for Keathley Canyon gas export pipeline. As soon as this opera- tion is completed, another contract awaits for the 20 inch-diametre, 60km long Big Foot lateral export pipeline for Enbridge in 2200m maximum water depth, also in the Gulf of Mexico. A third contract in this region is signed with Amberjack Pipeline for a 219km, 24 inch-diameter pipeline at 2140 metres depth. The pipeline will run from Chevron’s deepwater Jack-up rig to a Shell-owned and operated platform in Green Canyon.
“The fact that we have secured so many important contracts in important regions proves that there is definitely a market for this type of vessel,” says Fantacci.
In 2014, the vessel will move on to Australia to install an 889 km pipeline of 42 inch-diameter pipes down to 275 metres deep. The pipe is for the Ichthys LNG project, which is a joint venture between INPEX and Total and will connect the offshore central processing facility to the onshore processing facility in Darwin. Saipem is responsible for the entire engineering, procurement, construction and installation in the Ichthys Project, which is expected to produce 8.4 million tonnes of LNG and 1.6 million tonnes of LPG per year, as well as approximately 100,000 barrels of condensate per day at peak times.
THE BEST OF EVERYTHING
For this exceptional construction, Kongsberg Maritime has provided a Full Picture Delivery, comprising of DP-3 system (K-Pos 32 and K-Pos 12 BU), cJoy Independent Joystick System, K-Chief 700 Ves- sel Management System incl. Power Management System, Auxiliary Machinery & Control and Ballast Control System, K-Thrust Thrusters Control System, K-Bridge Integrated Navigation System and Integrated Safety Management System. The size and complexity of the vessel can be illustrated by the 11,500 electrical input/output (I/O) points fitted on board, something which is comparable to an oil rig. A normal pipelayer would only have about half the amount.
“We want to achieve excellence, and there are no standard solutions onboard this vessel. We have chosen the best of everything,” says Captain of the Castorone, John de Hartog. He emphasises the importance of keeping a stable position for the complex task that the vessel will perform.
“A pipelayer is absolutely dependant on keeping stable positions otherwise the pipes may break or be damaged. An excellent DP system is vital in order to achieve this. KONGSBERG and Saipem have had a very long and good working relationship, and we know that the KONGSBERG systems are reliable. They are a market leader in DP systems, and after some good discussions, we arrived at a custom made DP system that is suited for the 11 thrusters onboard, and for the complex operations that this vessel will perform. The level of professionalism that KONGSBERG provides made us feel safe,” he comments.
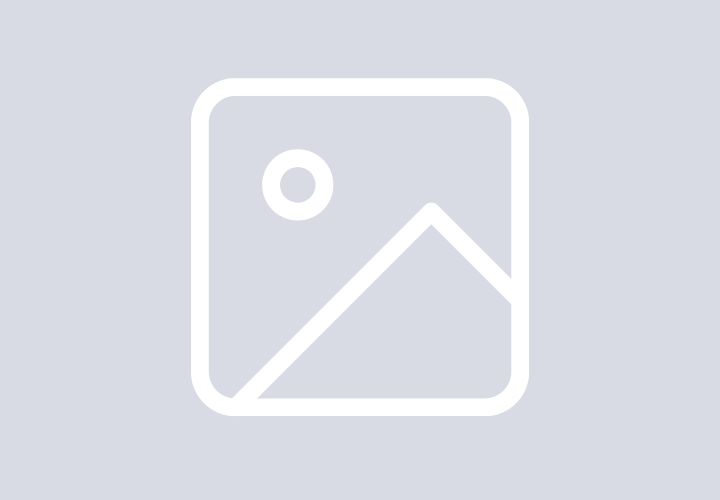
During normal operations there will be 450-600 people onboard.
A SAFETY LEADER
In addition to being a leader with regards to size and capacity, Saipem also had the goal of building the safest pipelayer in the world.
“Our main concern is that all the colleagues who live aboard this vessel go home safely after a shift. We want to ensure that nobody gets hurt, and we should be equally proud of our safety measures as we are the other features of this vessel,” says Captain de Hartog.
One of the measures taken to ensure the highest level of safety is to install Kongsberg Maritime’s Integrated Safety Management System (ISMS), currently only used aboard passenger vessels. With as many as 702 crew members on board at one time, the Castorone is in fact classified as a passenger vessel. Keeping track of so many crew members is complex but important, which is why Captain de Hartog, took the initiative to install ISMS from KONGSBERG. The system includes the four main applications safety desk, passenger tracking system for emergencies, emergency crew mustering and a fire patrol system. It enables distribution of critical information to all designated channels as fast and as efficiently as possible.
“During normal operations, there will be approximately 450-600 people onboard, maybe more. This means that we have to master a lot of people. We looked around in the market for products that could handle this, and found no solution other than Kongsberg Maritime’s system. It is impossible to master and keep track of so many people in any other way than by using a good tracking system. The Integrated Safety Management System is also compatible with the rest of the equipment from KONGSBERG. Having one supplier for several systems is a great advantage because it is easier to interface and because you only need one contact person with the supplier,” says the Captain.
GLOBAL PRESENCE
Captain de Hartog also emphasises KONGSBERG’s global presence as an advantage for Saipem, both throughout the project period and in terms of local support. From Kongsberg Maritime’s side, the project has mainly relied on local resources from the Singapore office in collaboration with staff from other locations.
“We are very happy to contribute to this milestone project,” says Stene Førsund, Managing Director, Kongsberg Maritime, Singapore. “Kongsberg Maritime has enjoyed a very long and good working relationship with Saipem, and we appreciate their trust in our products for the intricate tasks that this unique vessel will perform. This project is also a good example of Kongsberg Maritime’s global presence, involving close collaboration between our offices in Europe, China and Singapore as well as with the client and yard. We hope to continue our good cooperation with this important client for years to come.”