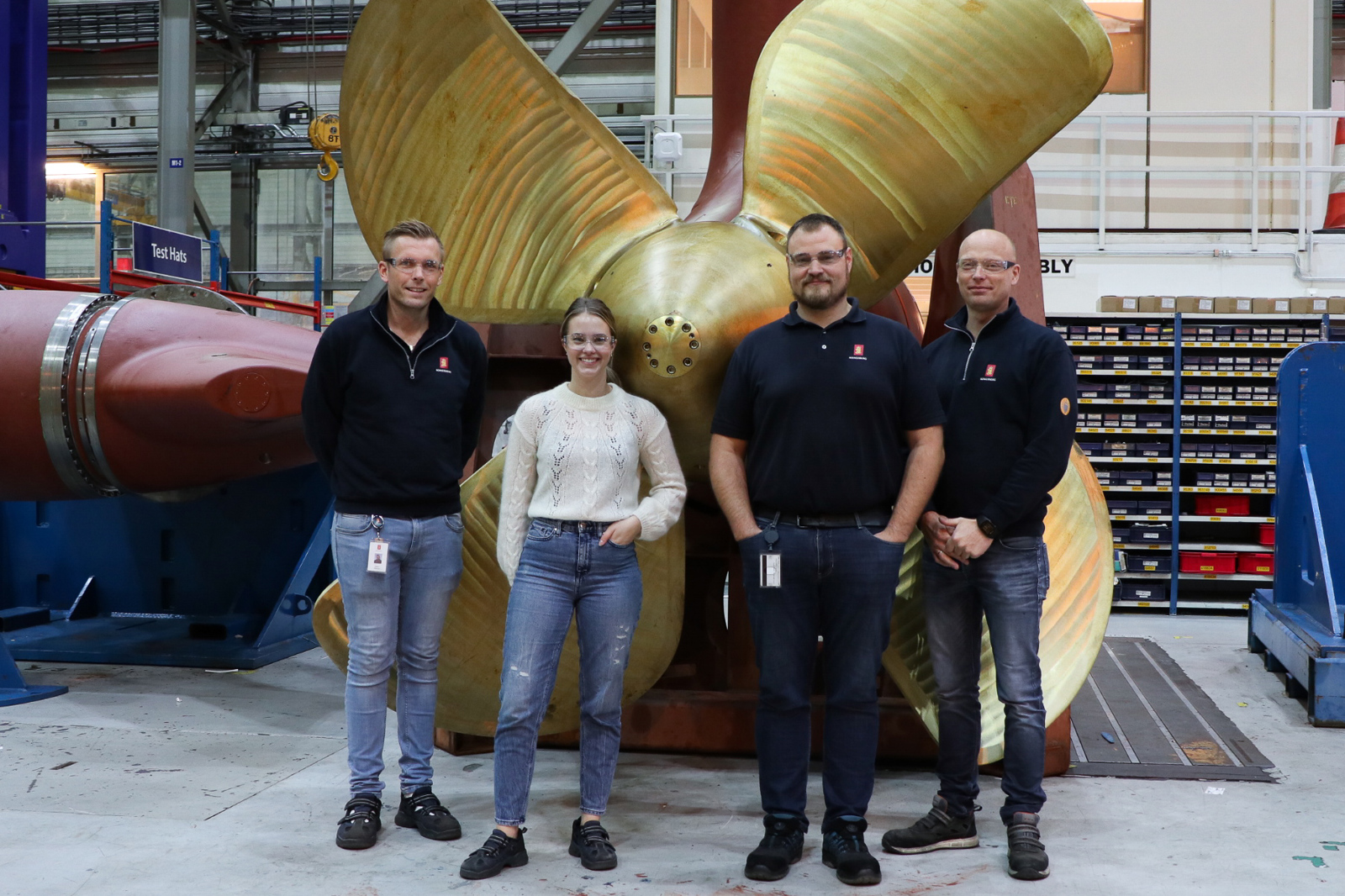
It’s a late September morning. The express boat to Hareid leaves Ålesund at exactly 06:45. There’s a nip in the air, but the sun has begun to peep through the gaps in the Sunnmøre Alps. William Pettersen, team leader at Kongsberg Maritime CM, is waiting for me on the quayside in Hareid. We get into his car and drive to the factory in Ulsteinvik.
When we arrive at the site, I’m issued with safety boots and glasses, along with an unmissable dark red and orange vest emblazoned with the word VISITOR. We walk into the office for a cup of coffee and to say hello to the other team leaders, Frode Steinnes and Hans Martin Bigset. A few weeks ago, I met these guys on an internal leadership course in Kongsberg. That’s how we got to know each other.
RISEN THROUGH THE RANKS
In the corridor I meet Aage Falch Gundersen, manufacturing manager here in Ulsteinvik. It was he who sent the guys on the course in Kongsberg. I sit down in Aage’s office for a chat. Aage tells me that he has worked for the company since 1996, and that he’s been rising through the ranks ever since.
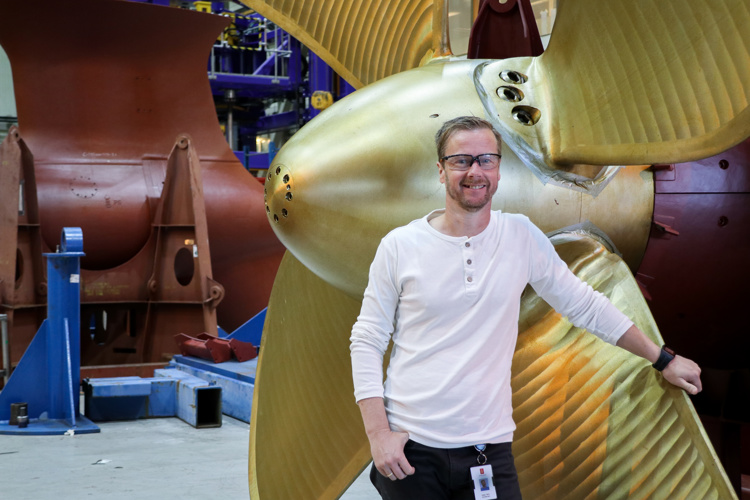
“Can you tell me a little bit about when you started in the company?”
“I started on the shop floor, like many other people. I was 23 years old and had no relevant experience or education. My father and brother both worked here, so it was where I definitely didn’t want to work. But one day the man who was manufacturing manager at the time phoned me up. They needed more people. I knew the manufacturing manager through my father, so when he called, it was hard to say no. I came for an interview and got the job.
“I started as a machinist. That involves standing and making components for assembly. The best way to learn a job like that is through practical experience. So, it was really important to watch other people. I was trained by my younger brother — and he still works here too.”
TOOK OPPORTUNITIES
“How did you go from being a machinist to manufacturing manager?”
“I worked on the shop floor until I got my apprenticeship as an external candidate in 2001. Then I specialised in CNC. After that, I started doing evening classes at a technical college. The company was very accommodating in terms of allowing us to combine work and studies, and they also covered all the costs involved. At that time, I had two young children and was working shifts while going to evening classes. There were three of us doing the same thing, and we worked a lot as a team. I finished my studies in 2005, and the following year I was offered the position of planner.
“When you work as a planner, you’re responsible for organising a process to ensure that everything runs seamlessly, from production to customer. That means acting as a link between production, purchasing and contracts, and getting everything to run as it should.
“I worked very closely with the production manager, and when he moved into a different position, I was given the job as new production manager for the machining department. It came completely out of the blue! But then there was a downturn, and I spent the first few years as production manager having to give lots of colleagues their notice; some of them took severance packages. It was a tough and hectic period. And those of us who were left were given more responsibilities, which in my case meant responsibility for apprentices and the control department.
“In summer 2018 I was offered the position of manufacturing manager, which meant that I also became responsible for assembly. It was a huge vote of confidence to be given such a responsibility, and a challenge I could not refuse.
“Now I have five team leaders reporting to me. The team leaders ideally know more than me about their fields, which means that we can challenge each other and develop as a team. I give them a certain degree of control, while I see the bigger picture and the plans.”
KONGSBERG GRUPPEN AS NEW OWNER
“What were things like before the acquisition?”
“We were in a period of great uncertainty. The job cuts had resulted in a high level of sick leave. We needed to improve communications in order to reduce the uncertainty. Then the years went by, and when we were told that we were going to be sold, the uncertainty returned. So, it was really important to keep the staff informed about the changes.
“The time passed, and even though we were downsizing, there was still a lot to do. The day we found out that it was KONGSBERG who had bought us, all you could see were smiling faces all over the building — and of course we had to put the flag up! Now that the acquisition has gone through, the real work is starting. We still have to deliver and earn money.”
“What has been the biggest change?”
“We now have an owner who is really interested in getting to know us and our products. It’s also extremely positive that Egil Haugsdal, the president of Kongsberg Maritime, has visited us a few times. It feels as if we are one company!”
THE PROPELLER FACTORY
We have been talking for an hour, and Aage has another meeting to go to. Out in the corridor I meet William, Frode and Hans Martin. They take me on a tour of the production hall. As team leaders they are each responsible for their area of production.
In Ulsteinvik, raw materials are designed and shaped into specific components for various types of propellers and thrusters. The components are sent from one line to another through the production process, until they finally end up in the assembly department. There the products are assembled and quality checked before they are ready for delivery.
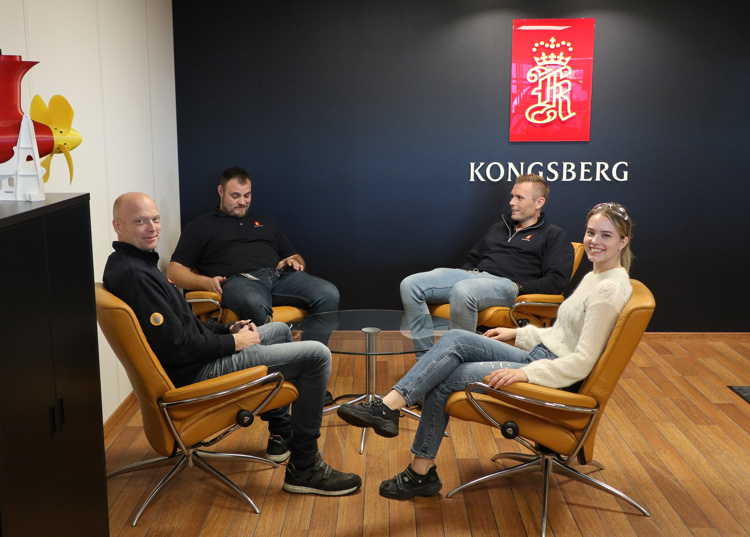
We go into the production hall’s control room. The room has a simple bridge system that is connected to the testing areas. The control room boasts Stressless chairs and has a brand-new KONGSBERG logo on the wall. On the screens on the bridge, we can see live monitoring of a Tunnel Thruster, which is in one of the testing halls.
“Would you like to test out the thruster?” one of the guys asks me.
Abruptly, William is on the phone, and seconds later the thruster is ready for testing.
“All you need to do is set it away,” one of the guys tells me, and I take the controls.
The Tunnel Thruster starts to spin faster and faster. There is a lot of power in that thruster. A Tunnel Thruster is designed to give a ship side force in order to improve its manoeuvring capability in port, or additional station-keeping power when dynamic positioning. This is just one of the many propellers and thrusters produced in Ulsteinsvik.
Suddenly, it’s lunchtime, and my visit is drawing to a close. As I board the express boat back to Ålesund, I am already looking forward to my next visit to the factory in Ulsteinsvik.
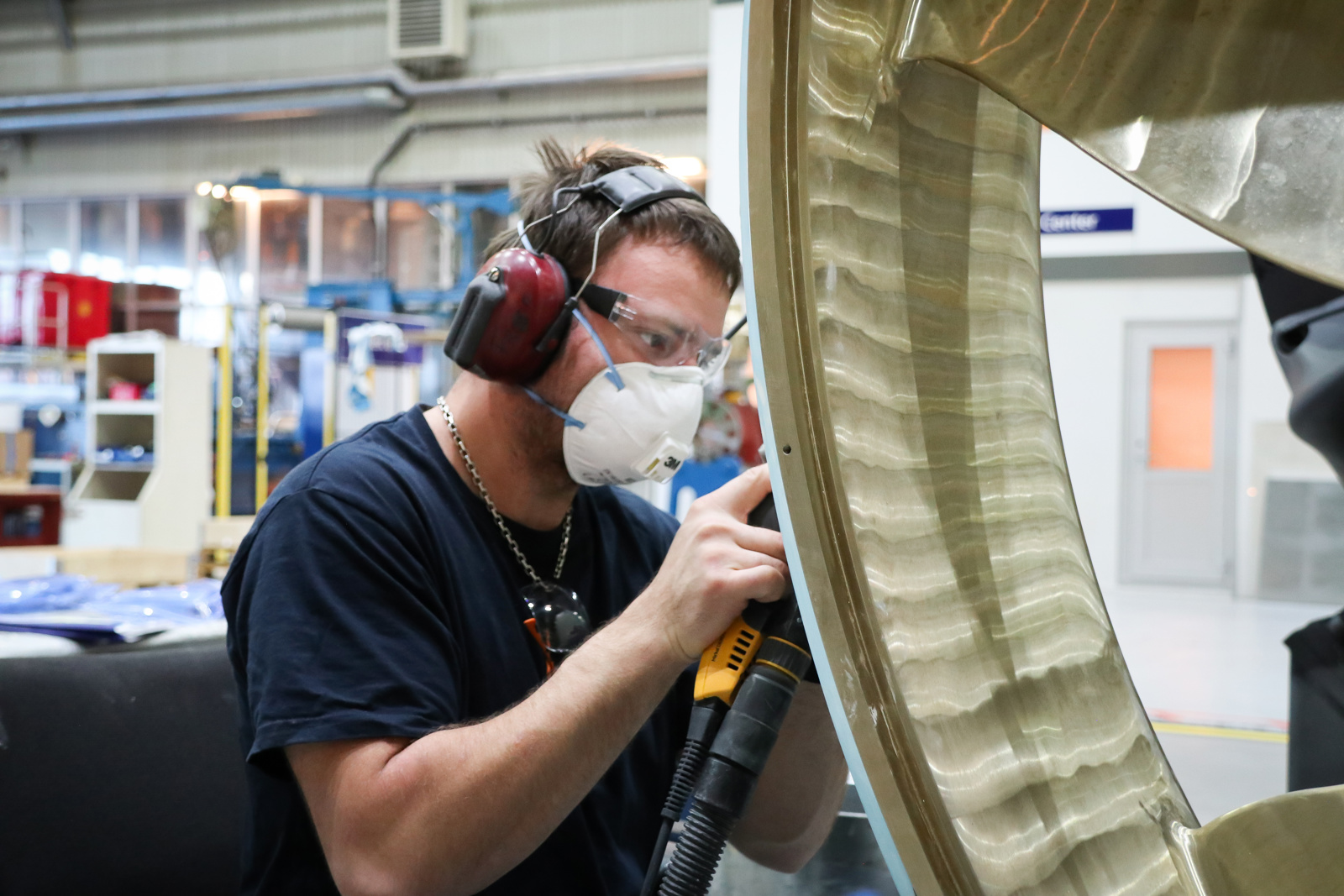
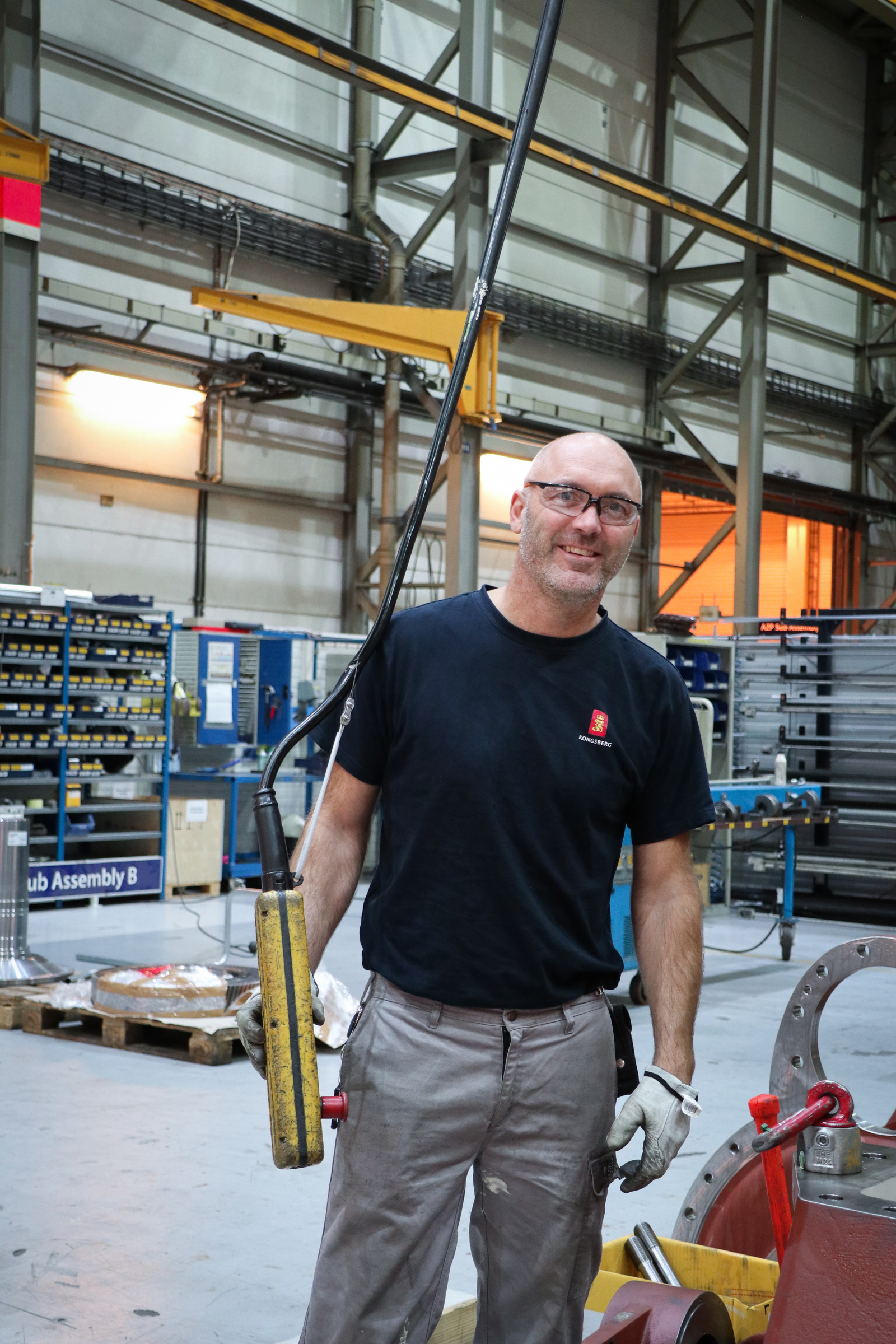
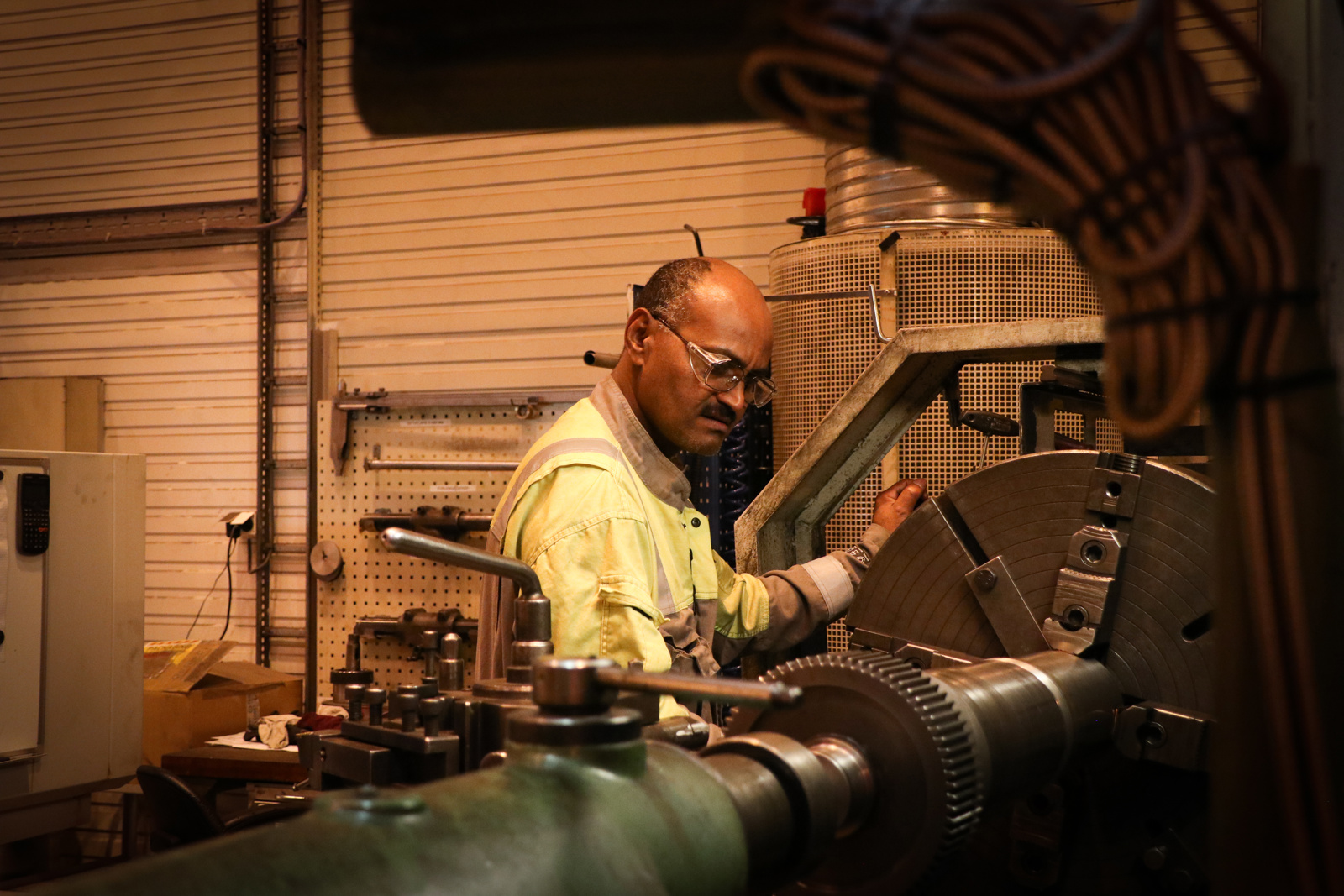
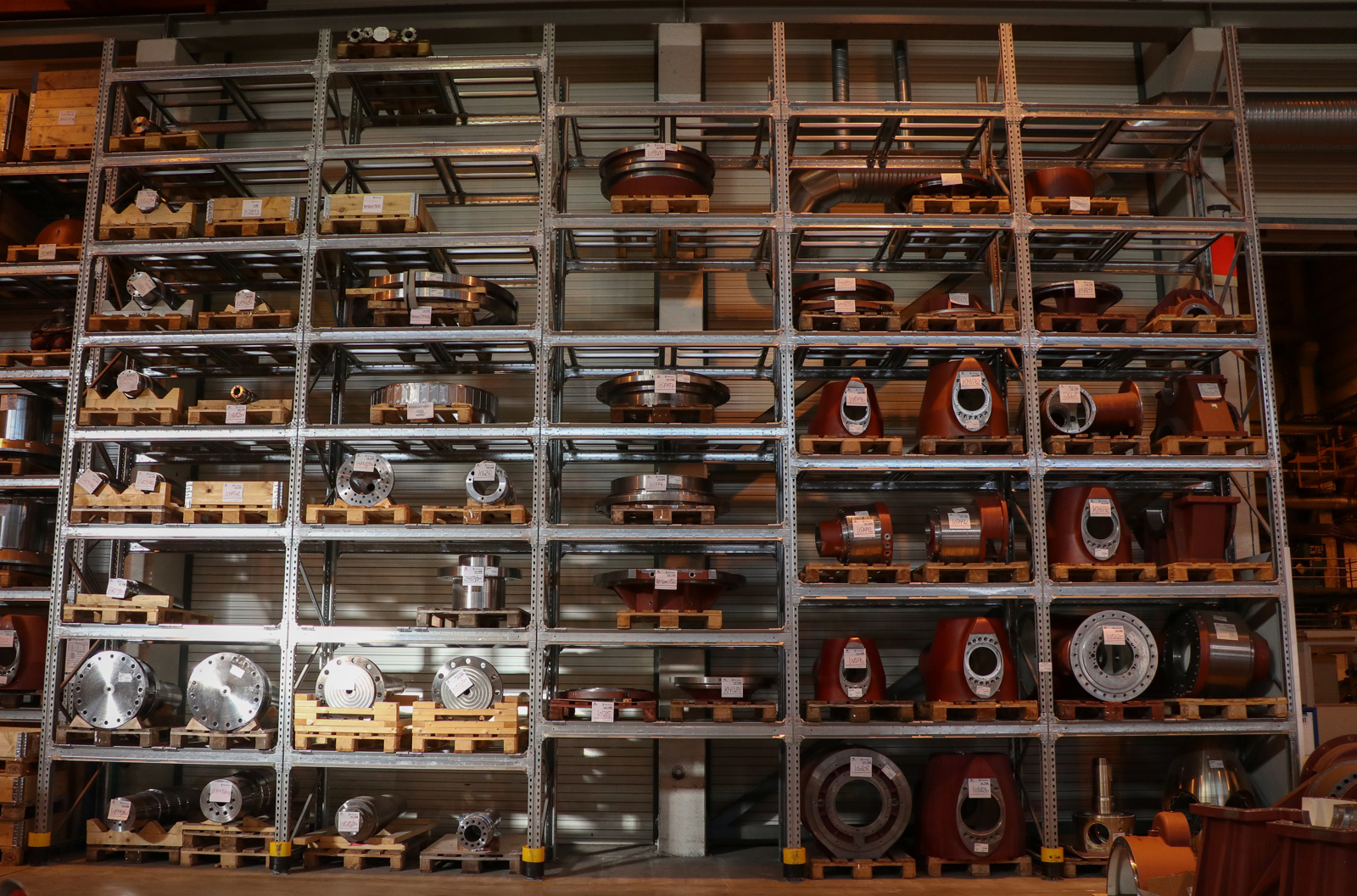
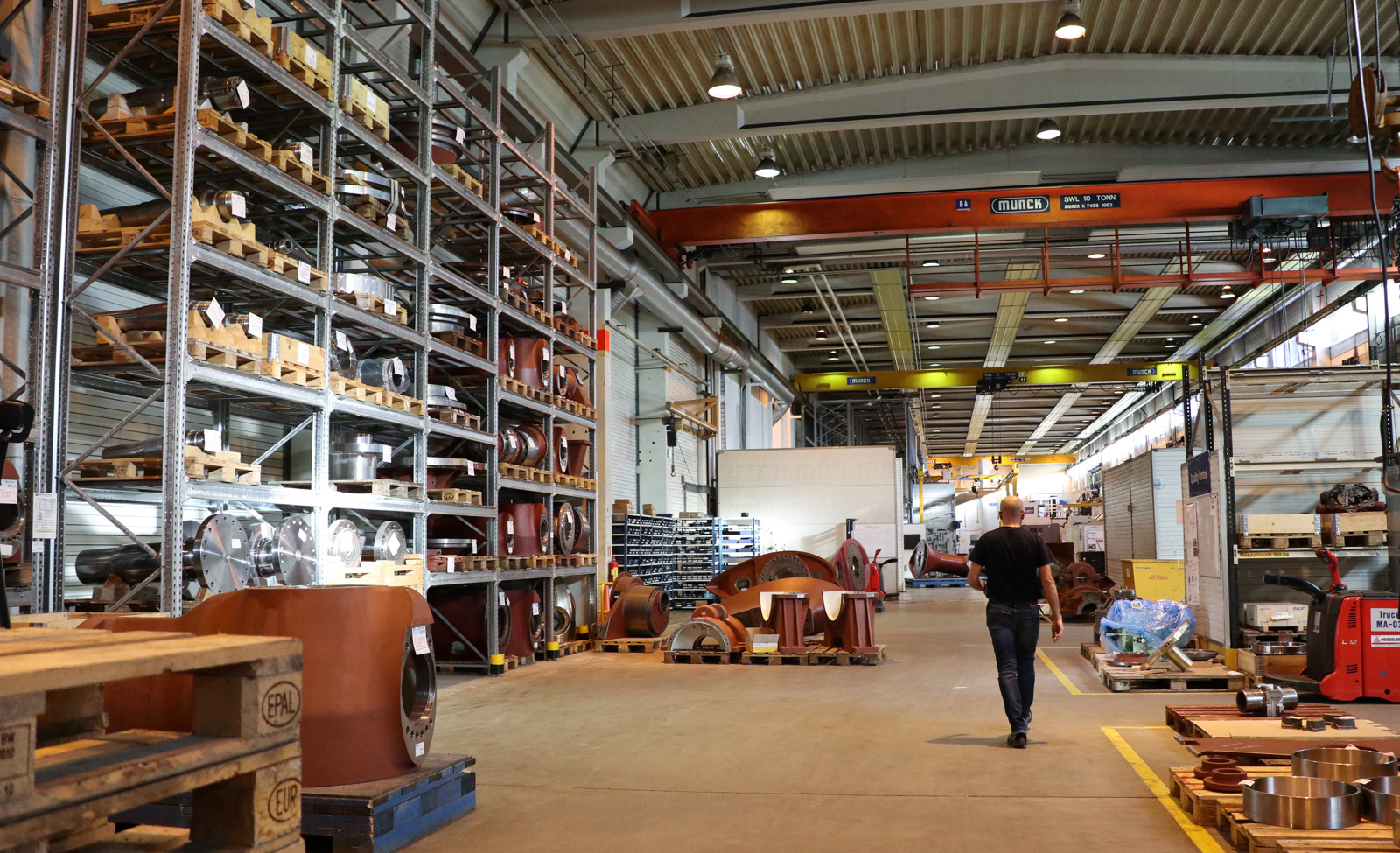
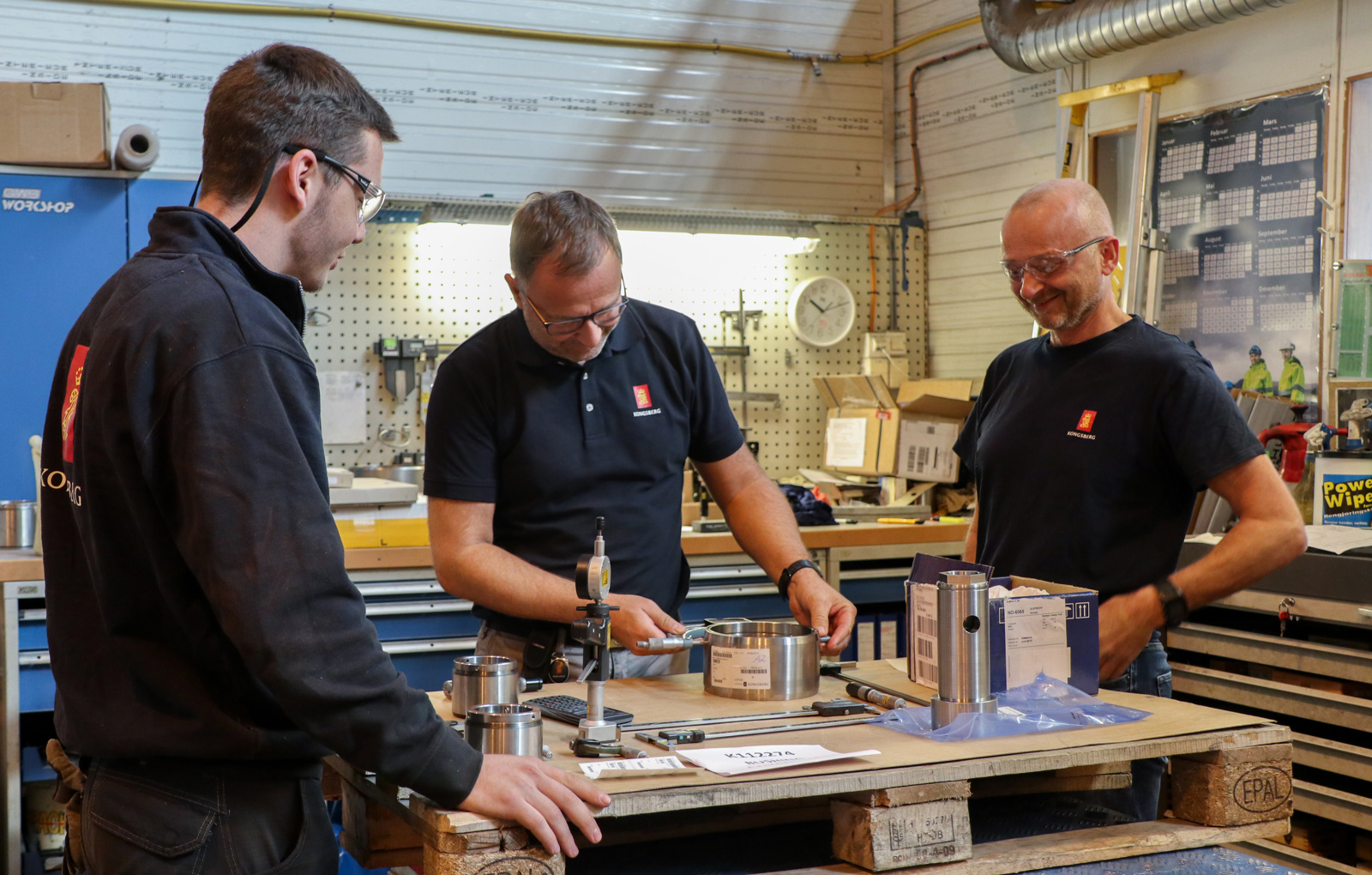
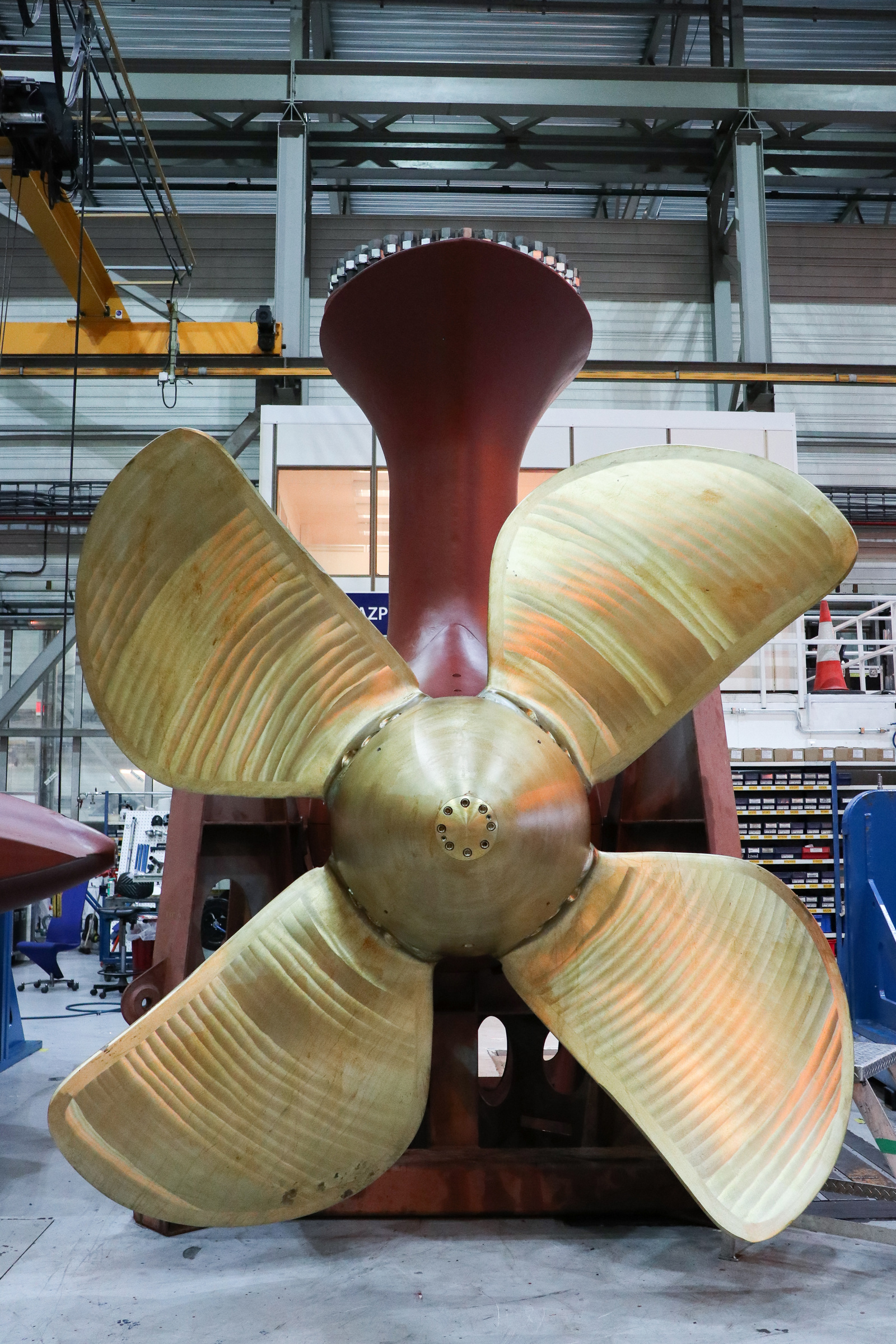
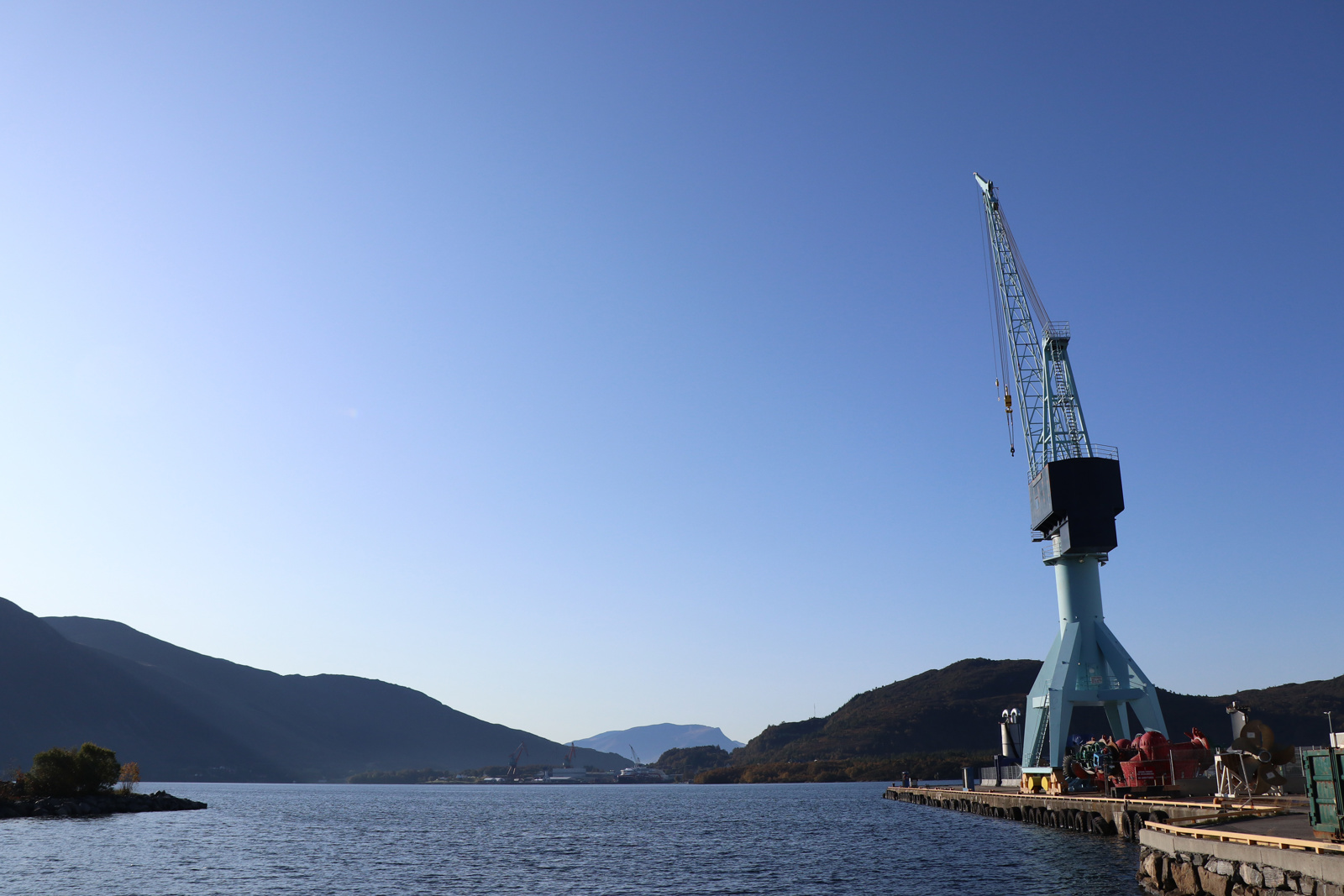
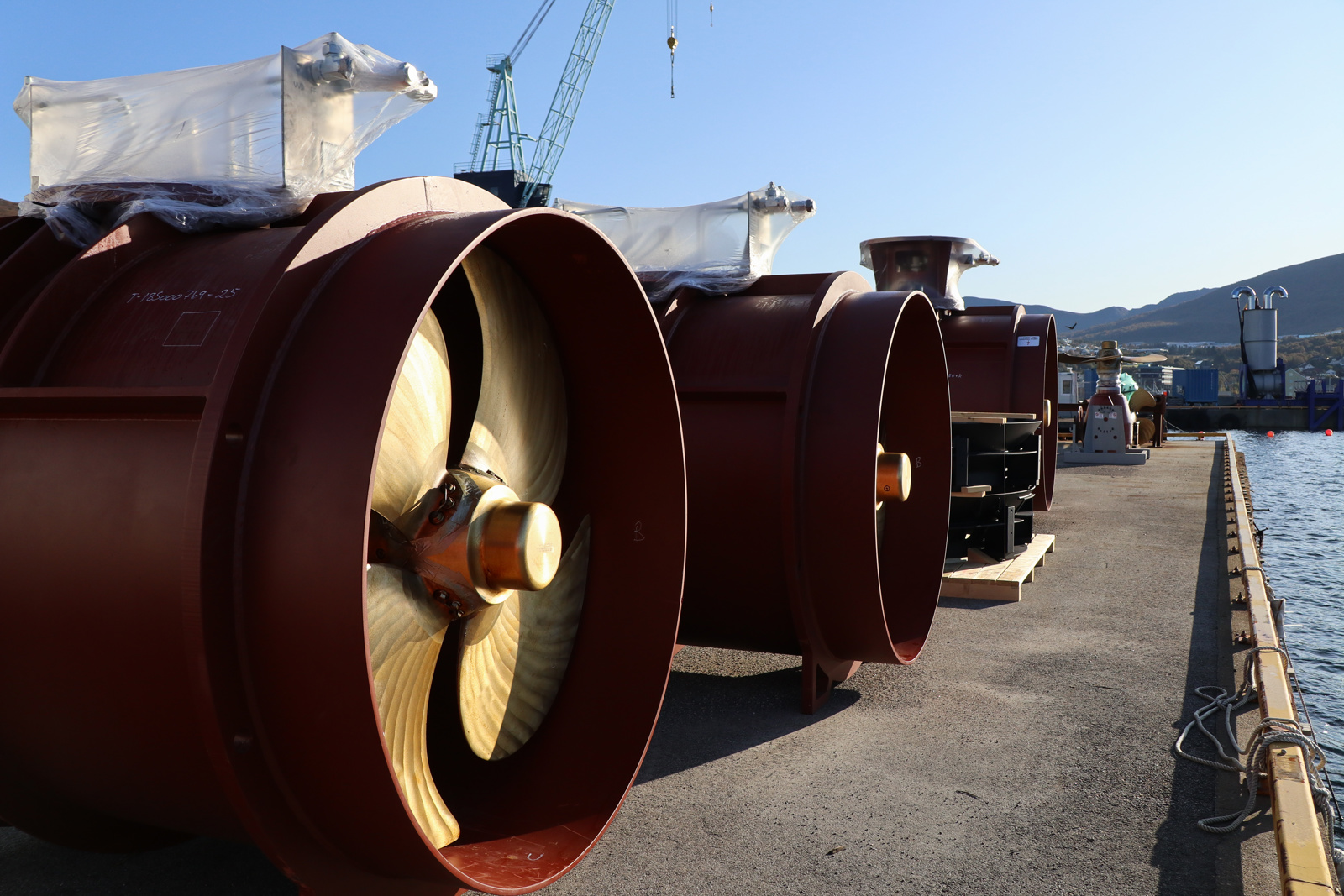
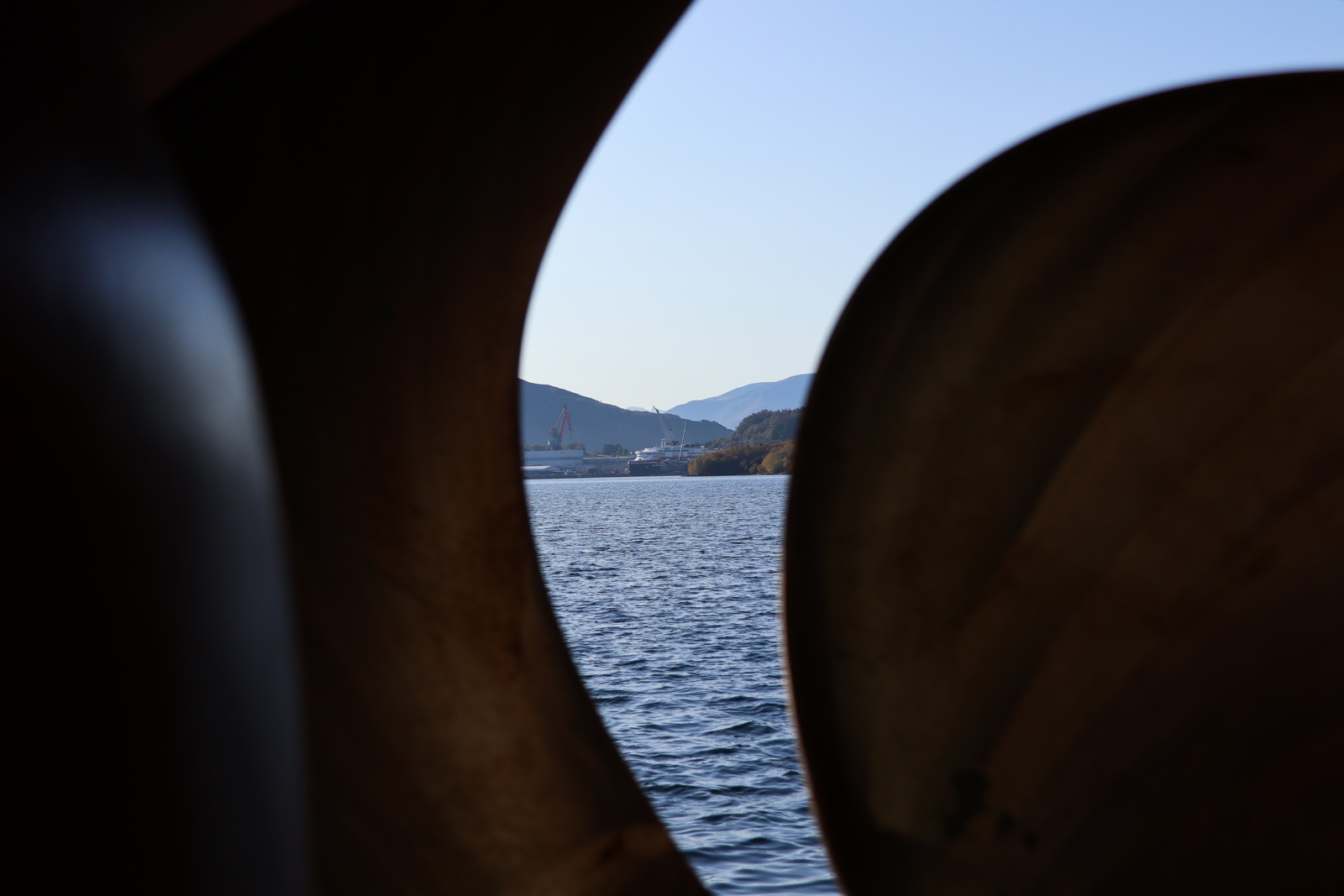
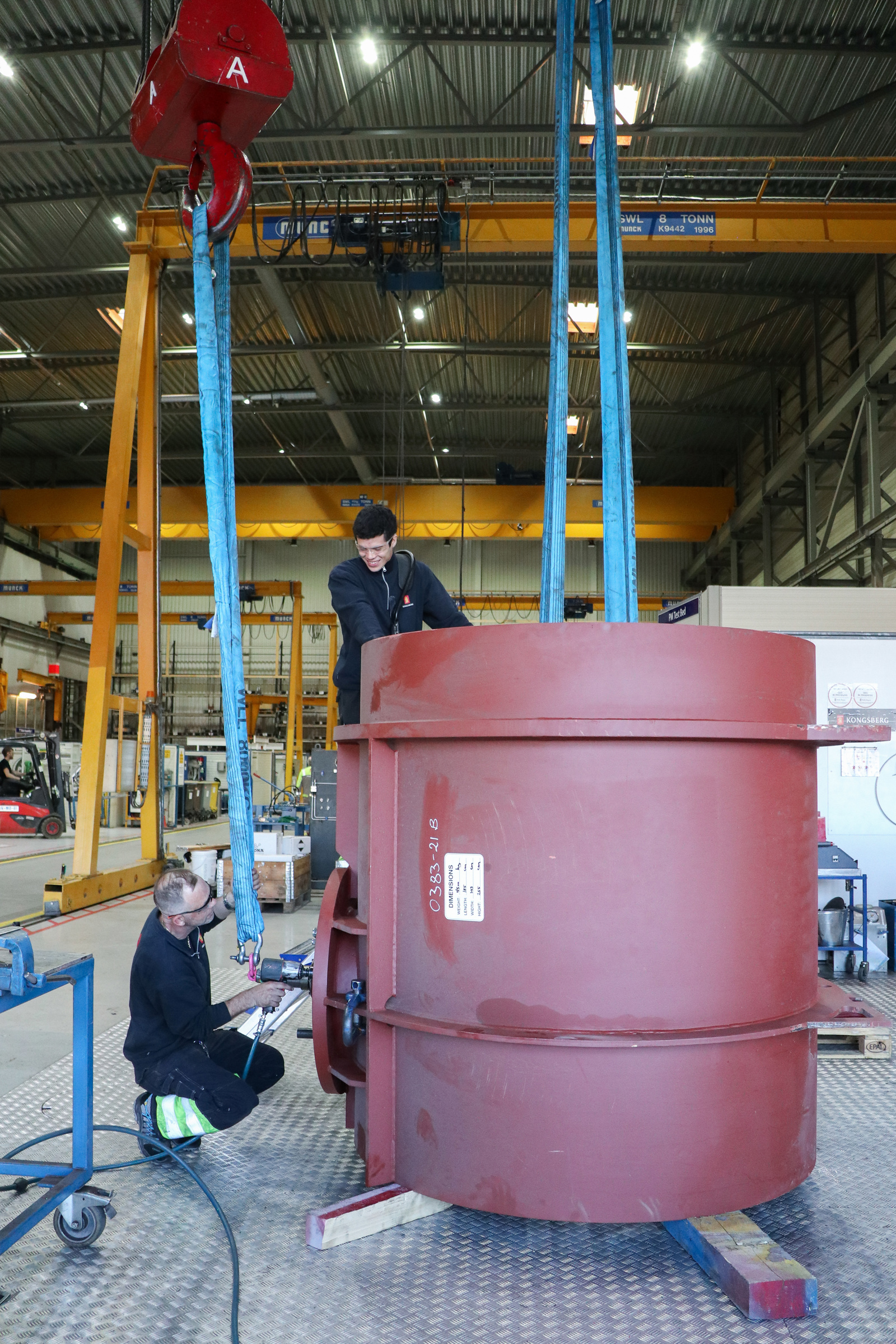
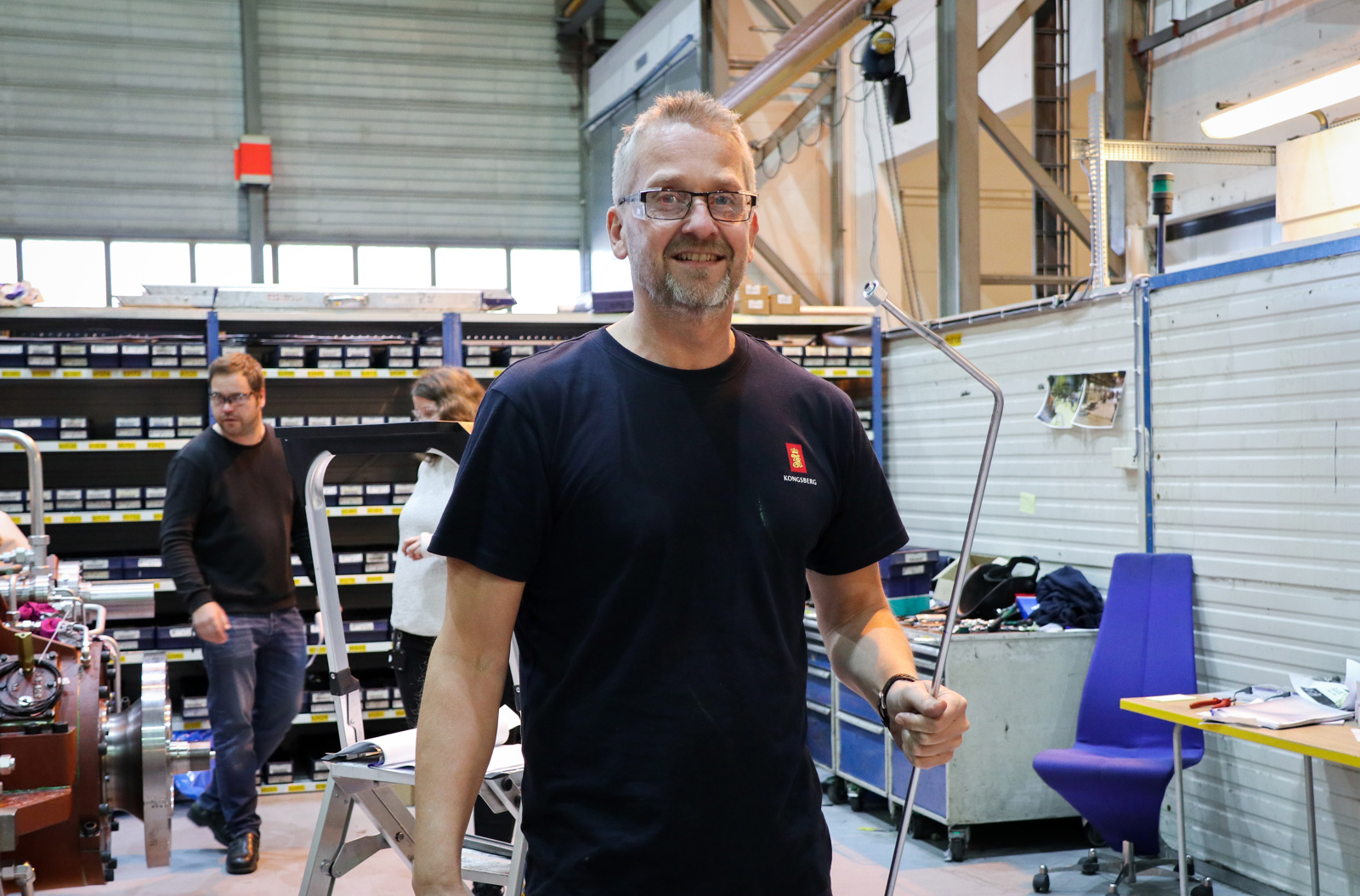
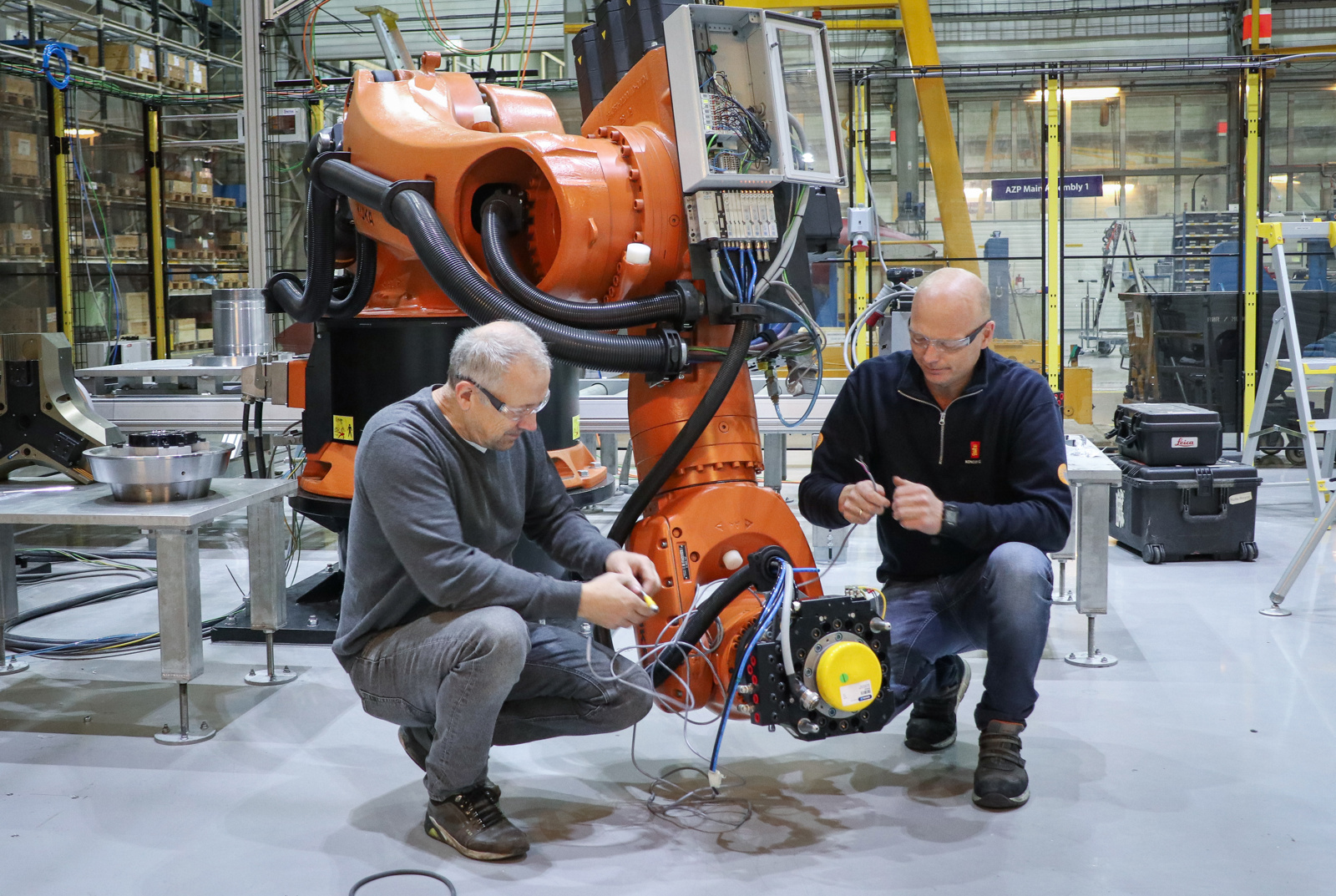
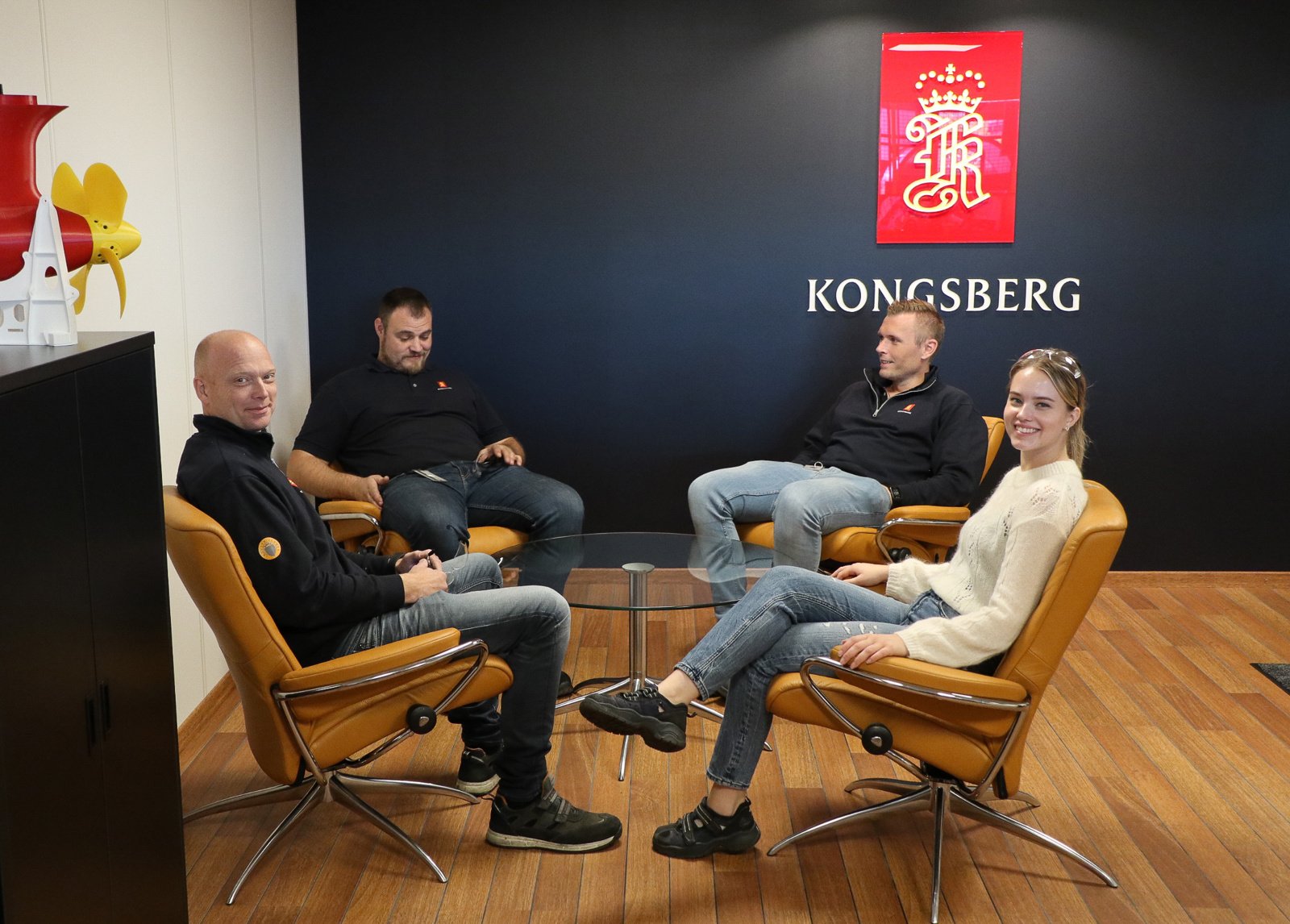
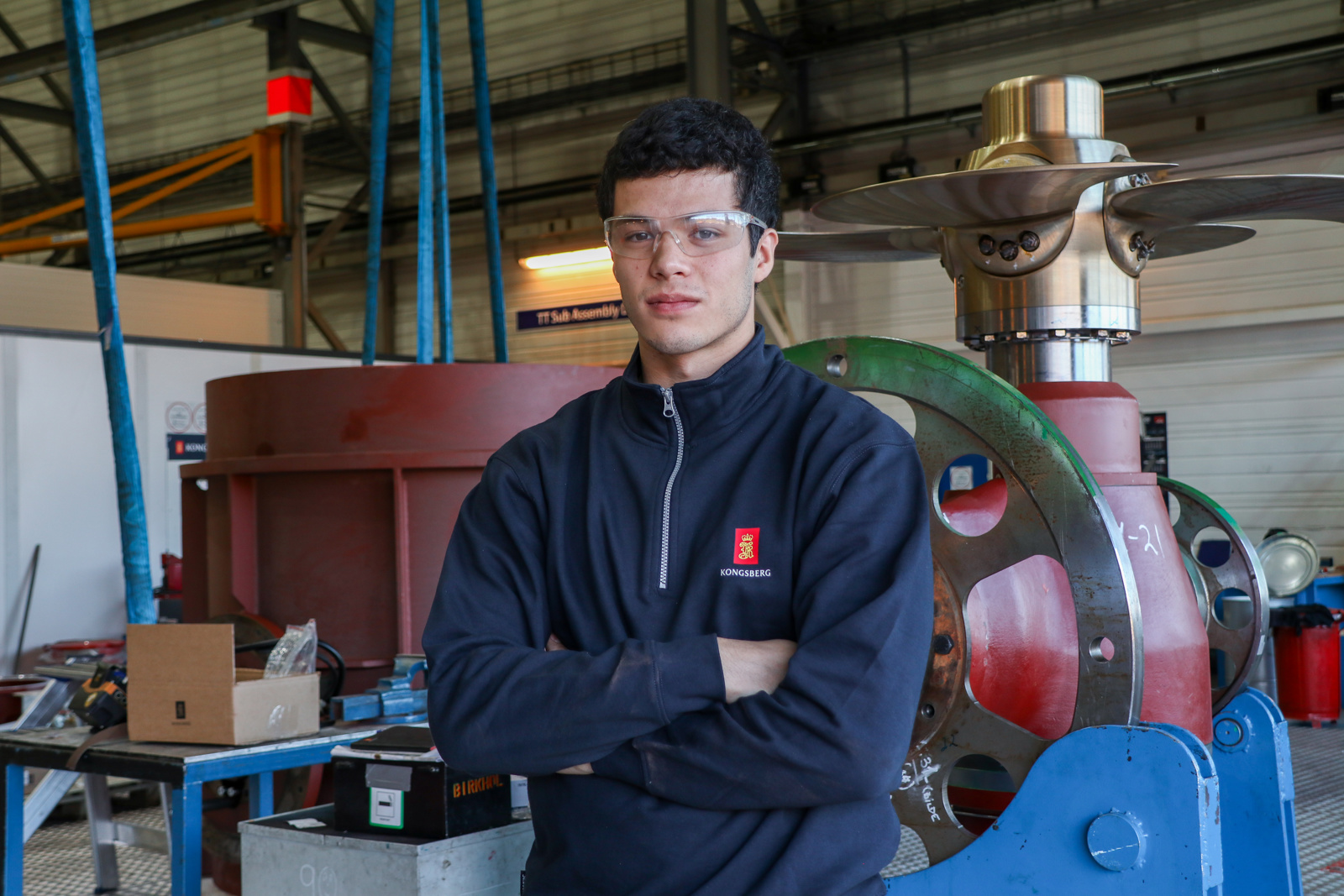
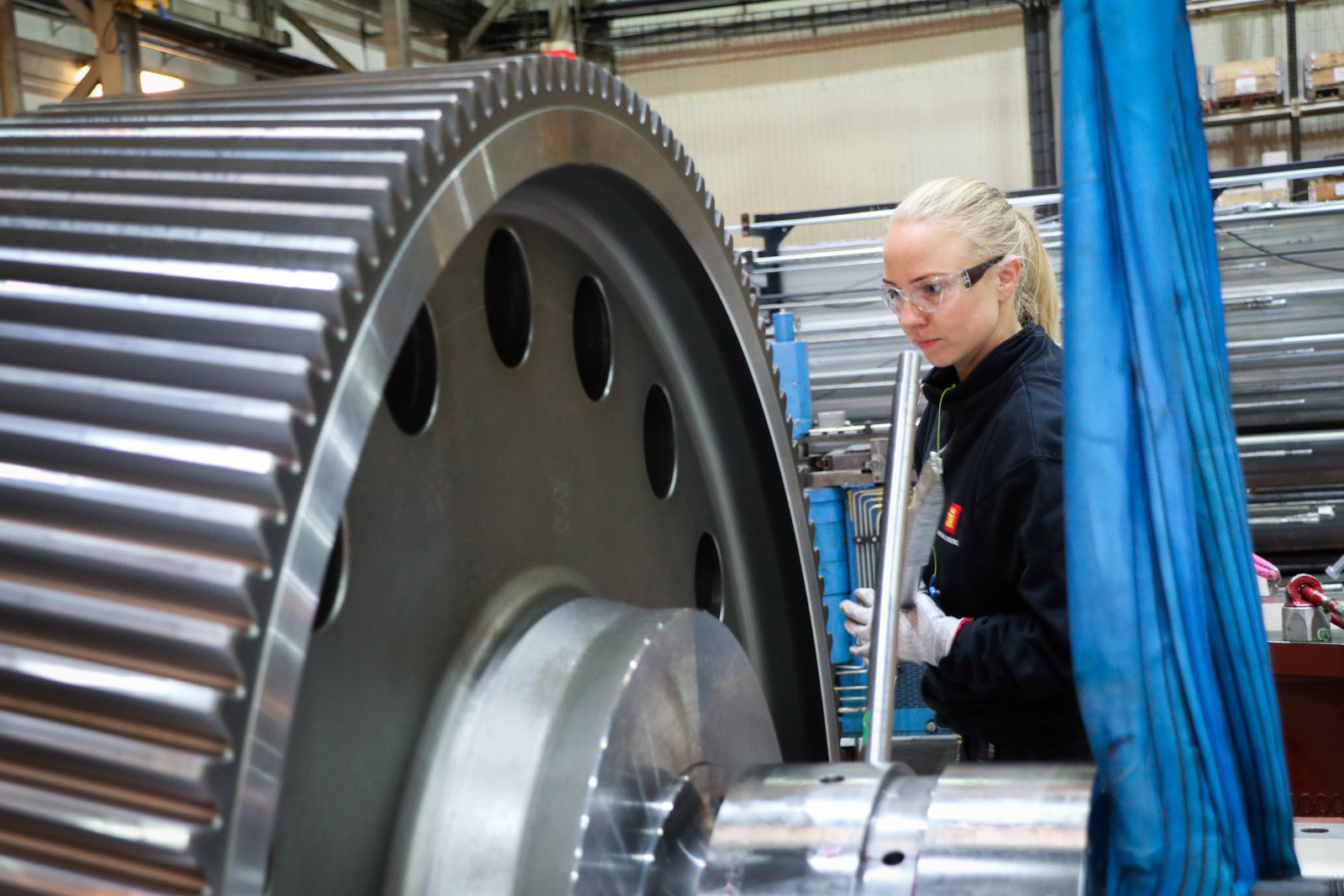