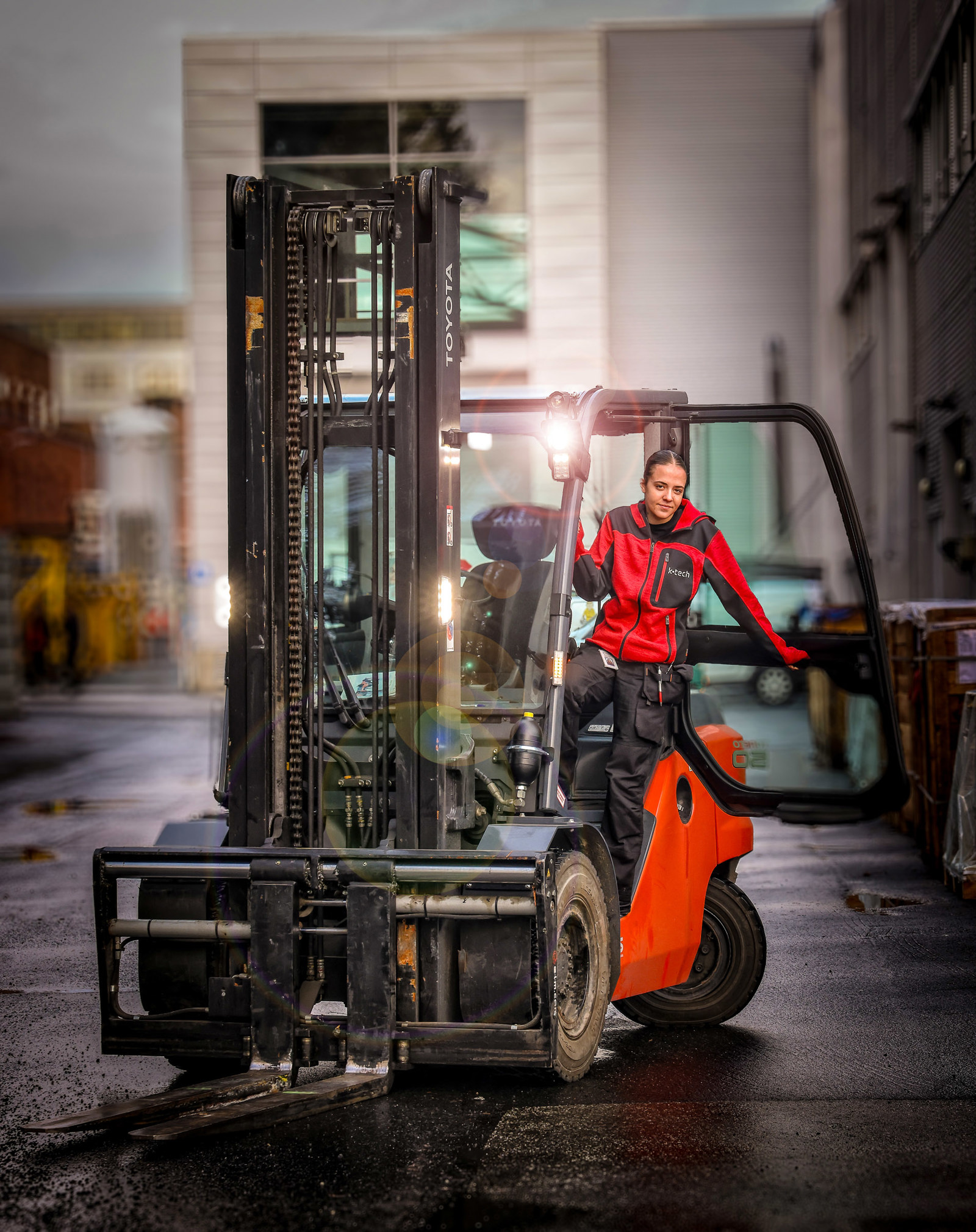
K-tech – A model for the future of vocational education
In 2008, three of Kongsberg’s leading technology companies – Kongsberg Defence & Aerospace, TechnipFMC, and GKN Aerospace – joined forces to establish a new and innovative education centre. The apprenticeship company K-tech was created to meet the growing demand for highly skilled workers in the region’s technology-intensive industries.
-
Text:Helene Strøm Bergset / KONGSBERG
Photo:Akari & K-Tech
Connecting education and industry
Since its inception, K-tech has pursued an ambitious vision: to create the world's leading model for vocational training. By integrating practical experience, theoretical instruction, and close mentorship, K-tech has developed a comprehensive training framework that equips future professionals with the skills and expertise the industry demands.
As a bridge between industry, secondary schools, and regional authorities, K-tech plays a crucial role in strengthening the link between education and the workforce. The company provides vocational training across a wide range of disciplines, from traditional trades such as welding and machining to modern fields like cyber security. Through K-tech, apprentices receive a well-rounded education that balances hands-on experience, theoretical learning, and access to specialized courses and laboratories.
"Our model is based on the Norwegian 2+2 apprenticeship system, where two years of schooling are followed by two years of on-the-job training. This provides apprentices with a unique opportunity to gain broad experience and access to expertise that individual companies often cannot offer alone," explains Stein Sandvold, General Manager of K-tech.
To ensure that apprentices are well prepared for future challenges, K-tech employs a dedicated monitoring system that includes monthly meetings and biannual evaluations. This structured follow-up provides both apprentices and companies with confidence that the training maintains high quality and is tailored to the needs of the industry.
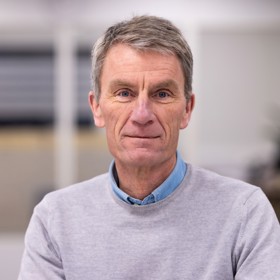
Stein Sandvold, CEO at K-tech“No one trains apprentices the way we do. In most companies with apprenticeship programs, apprentices follow a mentor, and their progress depends largely on the mentor’s expertise."
K-tech is a certified apprenticeship provider in no less than 15 different trades, offering classroom and laboratory instruction to ensure that theoretical learning objectives in the curriculum are met.
“The apprentices are employed by us, which means we have both the HR responsibility and the training responsibility. The apprentices then gain practical experience and expertise in the various owner companies during their apprenticeship period,” explains Sandvold.
This unique structure enables K-tech to support companies that would otherwise not qualify as apprenticeship providers.
“We have apprentices in companies that might not have been approved as apprenticeship providers on their own because they cannot meet all the requirements in the curriculum. That’s where we come in—we bring the apprentices to us for additional training and fill those gaps. This flexibility is one of the things that makes K-tech unique,” he explains.
“Our main role is to bring everything together and ensure that apprentices achieve all the learning objectives in the curriculum. We have a strong sense of responsibility for our apprentices, and our job isn’t done until every apprentice has secured a placement,” he concludes.
Historical roots and future growth
K-tech’s roots trace back to Kongsberg Våpenfabrikk, which trained an impressive 1,335 apprentices between 1957 and 1987.
At the time, a trade certificate from Kongsberg Våpenfabrikk was a highly sought-after qualification, opening doors to industrial jobs across the country. However, after the downturn in 1987, the structured apprenticeship programme disappeared.
By the 2000s, the demand for skilled workers had returned, prompting Kongsberg’s leading industrial companies to establish K-tech in 2008 as a long-term solution for vocational training.
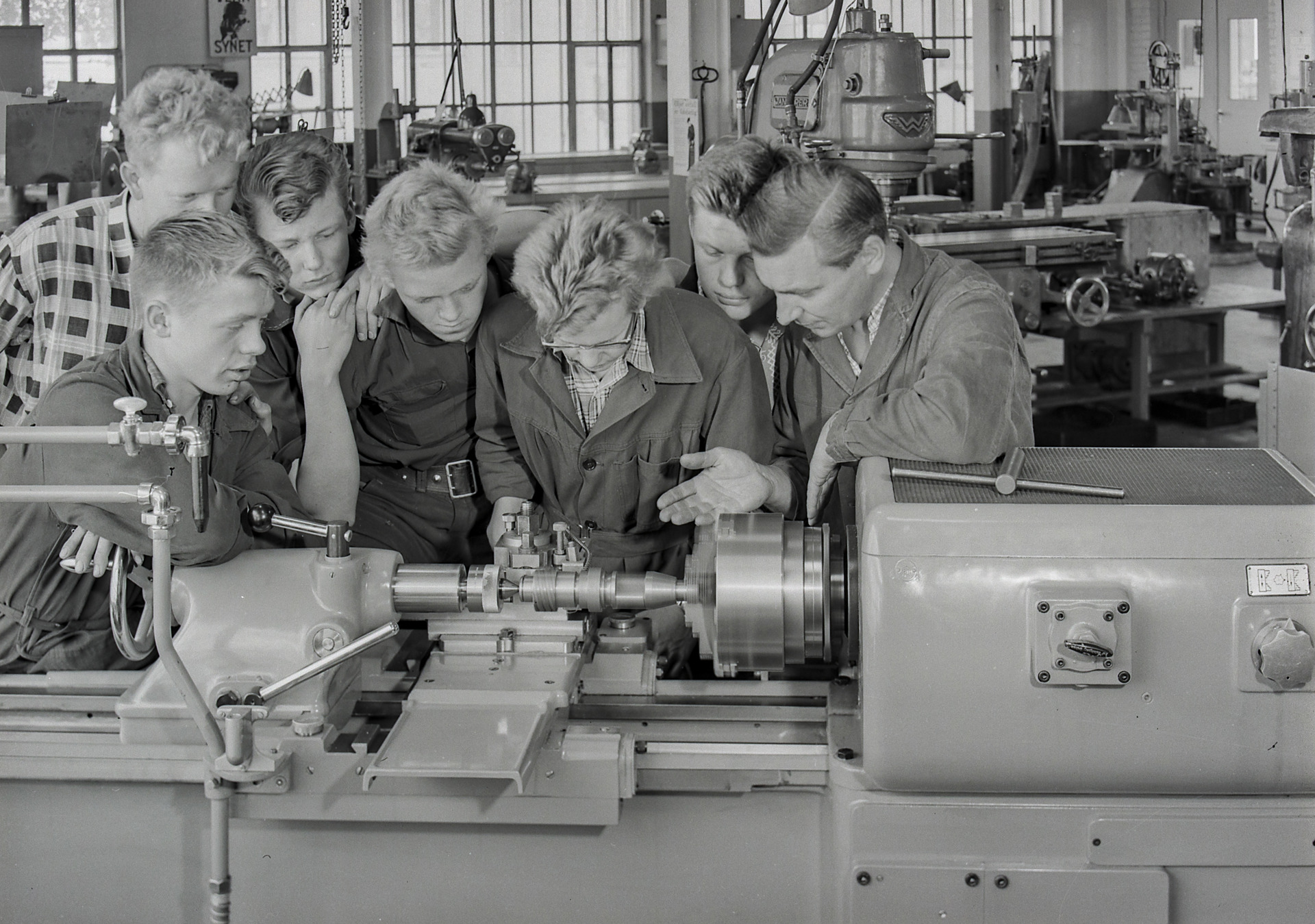
“The most critical factor in maintaining production in Norway today is educating production and skilled workers at a high level of quality,” says Terje Bråthen, Executive Vice President Aerostructures & MRO at Kongsberg Defence & Aerospace.
Bråthen heads the company’s production facility, Arsenalet, in Kongsberg, where the goal is to have apprentices make up 5–10 percent of the workforce at any given time.
“In recent years, the demand for defence-related products has increased significantly. We have gradually scaled up production, and we see that several of our products have shifted from being 30 percent production and 70 percent development to the opposite. Kongsberg Defence & Aerospace is experiencing tremendous growth, and the need for skilled workers is greater than ever,” he continues.
This growth is also reflected in the number of apprentices.
“Ten years ago, we took in around 20 apprentices per year. Last year, we welcomed more than 60, which directly correlates with the increase in production. Over the past decade, we have grown from 200 to 1,200 employees, and the expansion continues,” says Bråthen.
Last year, K-tech set a new record with 62 apprentices, and this year, they plan to increase that number to 65. Sandvold believes this growth highlights the crucial role of vocational training in Norwegian industry. With its innovative approach, close apprentice follow-up, and strong collaboration with the industry, K-tech has established itself as a leading provider of vocational training in Norway.
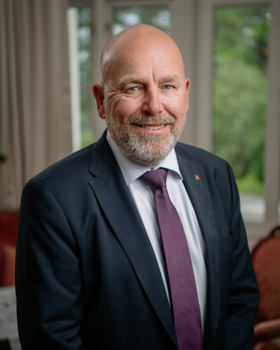
Terje Bråthen. Executive Vice President Aerostructures & MRO, Kongsberg Defence & Aerospace AS“K-tech is our training engine and will remain so for many years to come. They deliver high-quality skilled workers who help safeguard the competitiveness of Norwegian industry.”
A gateway for young talent
According to Sandvold, success as an apprentice is primarily about motivation and presence.
“It all starts with wanting to do it,” Sandvold emphasizes. “We often get questions from parents of first-year upper secondary students about what it takes to get into K-tech. The most important factors are motivation and attendance. If you have average grades and zero absences, you are guaranteed a place with us. The rest is about showing up, demonstrating interest, and making the most of the guidance and follow-up we provide,” he continues.
For K-tech, it is essential to tailor the training to both the individual needs of the apprentices and the demands of the industry.
“The most important factor is how the apprentices are welcomed into the companies. They come from different backgrounds and have had different upbringings. A key part of being an apprentice is learning how to become a good employee and colleague,” explains Sandvold.
Not all apprentices find the right path immediately, and K-tech sees it as their responsibility to guide them towards a career that suits them better.
“Occasionally – though rarely – apprentices become demotivated and underperform. This is often because they have chosen the wrong discipline. It’s okay to make mistakes, and when that happens, we are here to help them find a direction that is a better fit for both them and their employer,” he says.
At the same time, Sandvold highlights an important success factor: the attractiveness of K-tech’s owner companies.
“We shouldn’t underestimate the importance of having owners with strong brand names. Our apprentices get to work with world-leading products in oil and gas, aerospace, and defence."
“Apprentices are shaped by the culture they encounter, and this plays a crucial role in their professional and personal growth. Being an apprentice is much like taking part in the world’s longest job interview. If you show initiative, do a good job, and earn the respect of your colleagues, there’s a strong chance you’ll be offered a permanent position,” Sandvold concludes.
Career development and further education
K-tech not only opens doors to exciting jobs in the industry – it also provides a foundation for further development and career growth. Susanne Slettvik Dybvikstrand is a great example of how vocational training can offer a strong platform for the future. With a trade certificate in polymer composites and an advanced vocational diploma in mechanical engineering, she now works as a project engineer at Kongsberg Defence & Aerospace.
“Through my work experience at Kongsberg Defence & Aerospace, I discovered how exciting and rewarding this field could be. I had always envisioned becoming a mechanical engineer and considered taking an additional academic qualification, but after experiencing the workplace firsthand, I realised that the apprenticeship route through K-tech was a fantastic opportunity. That’s why I decided to apply,” says Dybvikstrand.
She describes her time as an apprentice with K-tech as a positive and educational experience.
“Starting at K-tech was incredibly exciting. For many of us, it was our first introduction to working life, and I felt very welcome. The fact that K-tech employs all its apprentices creates a strong sense of community – we are many in the same situation, which helps foster a close and inclusive environment,” she says.
After completing her apprenticeship, she chose to continue her education part-time with support from Kongsberg Defence & Aerospace.
“Being able to work and study at the same time was a unique opportunity that allowed me to develop both professionally and personally. The support I received from my employer was absolutely crucial. As long as you take initiative and show commitment, I find that the company is very supportive of further development. In addition, there are many internal courses and training modules that make it easy to build on your skills,” says Dybvikstrand.
Sandvold and Bråthen emphasise that a trade certificate is an excellent starting point for a career with many opportunities.
“With a trade certificate as a foundation, you gain a unique understanding of your field, providing a solid basis if you choose to further your education. At the same time, you acquire valuable work experience,” says Sandvold.
“As a skilled worker with us, you have many career paths to choose from. You can specialise within your trade and take on increasingly complex tasks, or you can continue your education. Many choose to attend vocational college, while others choose to complete a bachelor’s or master’s degree, for example, in engineering. We support both directions, allowing each individual to choose the path that best aligns with their ambitions,” Bråthen emphasises.
New opportunities
K-tech is also looking ahead, continuously expanding its offerings to meet the evolving needs of the industry. This includes specialisations in advanced technological fields such as computer electronics and Non-Destructive Testing. These areas reflect the future demands for expertise in an increasingly technology-driven industry.
“One of the things that makes K-tech unique is how the industry actively engages in vocational training already at the upper secondary level. Young people get the opportunity to be part of a real working environment at an early stage, while their education is tailored to market needs. This makes vocational training both attractive and relevant, opening up a world of opportunities after completing their apprenticeship,” concludes Bråthen.