New product!
We have just added this product to our product portfolio.
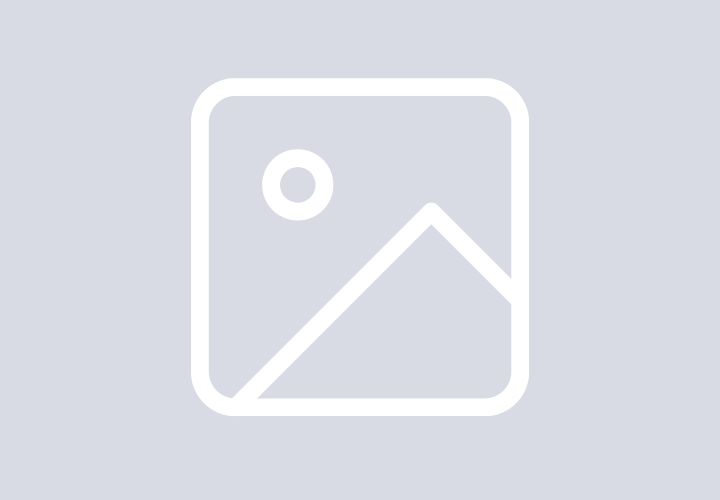
K-Sim® Engine Steam Propulsion Dual Fuel model
K-Sim® Engine Steam Propulsion Dual Fuel model
The K-Sim Engine Steam Propulsion Dual Fuel model simulates the steam propulsion plant of a typical modern, large LNG tanker machinery. The steam plant model is based on an actual LNG tanker, with performance and dynamic response closely matching that of the real vessel. This simulation emphasizes systems unique to dual fuel steam plants, including boilers, turbines, condensers, the condensate system, and both the fuel oil and fuel gas systems. In addition to sophisticated propulsion control and boiler management systems, the model also demonstrates how boil-off gas is utilized to ensure safe and economical operations on board.
Kongsberg Engine Room Simulators
Our engine room simulators offer realistic, hands-on training experiences in a ship-like environment, integrating vital components such as main engine remote controls, engine-room local panels, controllers, engine telegraphs, alarm systems, power supply switchboards, engine sounds, and more.
We have an extensive model library featuring various propulsion plants and engine types, all certified by the engine manufacturers as exact simulations. Our library includes models of diesel engines from renowned manufacturers like MAN B&W, Wärtsilä, Sulzer, Pielstick, MaK, and MTU, in addition to gas turbines, diesel-electric, water jet, and steam propulsion systems.
Furthermore, our systems are easily networked with our full ship’s bridge simulator for comprehensive, integrated ship training.
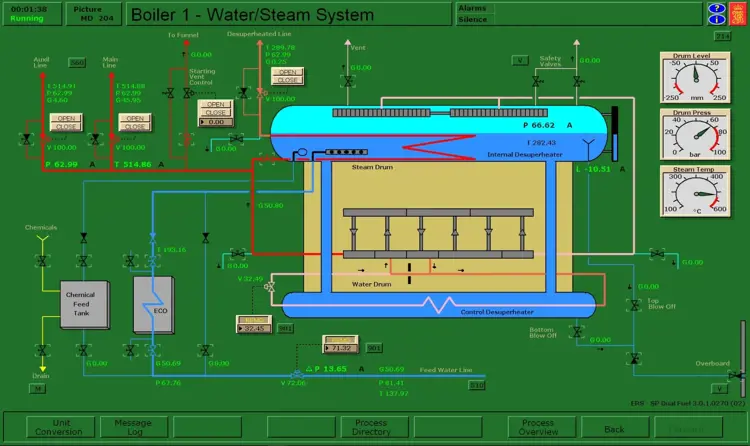
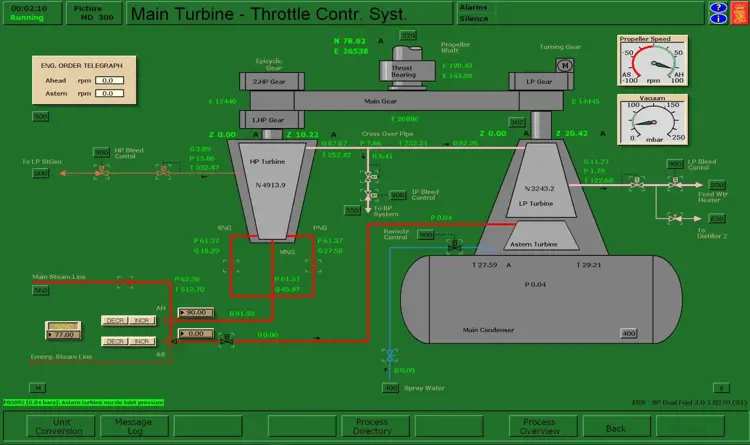
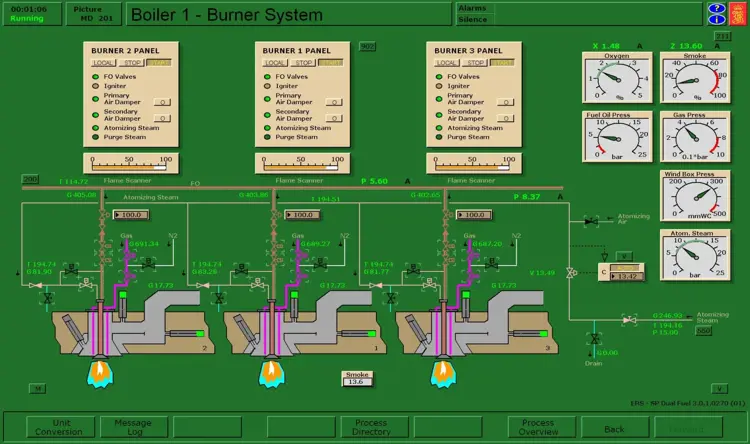
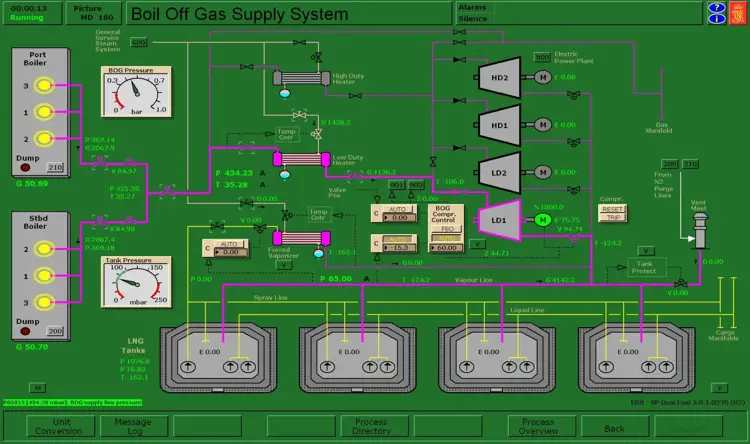
Training Objectives
The K-Sim Engine SP Dual Fuel model is designed to be a valuable tool in the basic and advanced training of marine steam engineers. The training objectives are:
-
To train junior engineers in basic engine room operations.
-
To train senior engineers in emergency operations and troubleshooting.
-
To train senior and chief engineers in optimal operation, fuel economy, and energy conservation.
This is achieved through controlled training, leading to a better understanding of the total plant operation, as a result of realistic simulation of a real engine room.
Compliant with Industry Requirements
Kongsberg Maritime simulator models exceed requirements in the STCW convention, Regulation 1/12, and fulfill DNV GL’s standard DNVGL-ST-0033 for Maritime Simulator Systems.
Lifecycle support for your vessel
-
24/7 Technical support
Our 24/7 technical support team is there to help at any time, day or night, wherever your vessel is.
-
Conversions, retrofit and refit
Upgrading and enhancing your vessel’s performance.
-
Training
Maximise crew efficiency and reduce downtime with expert training.