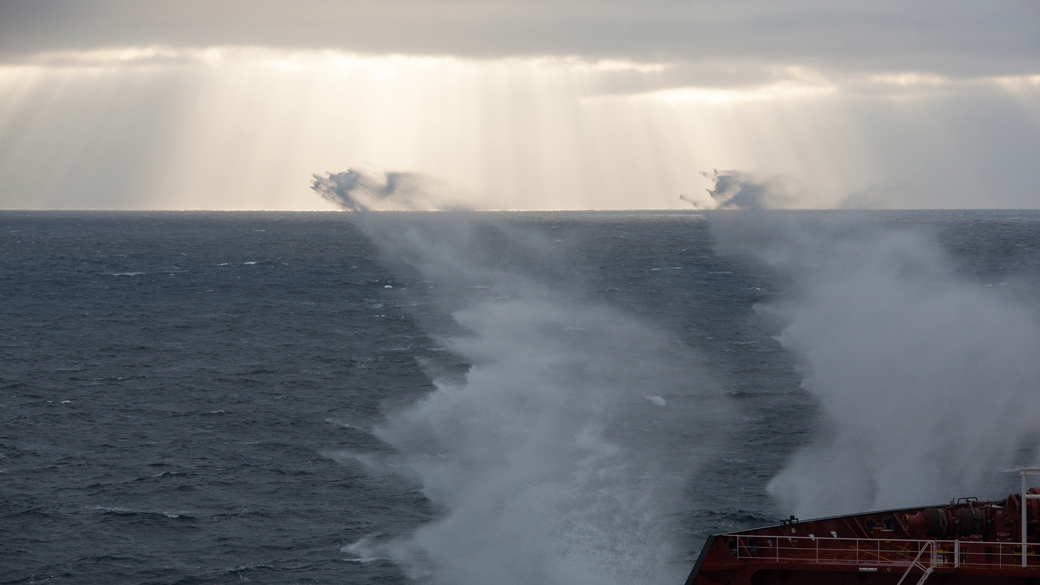
Heave compensation
Compact, robust solutions for any operational platform requiring Active Heave Compensation (AHC) e.g. offshore cranes, gangways, winches, launch and recovery systems (LARS), dynamic positioning and jackup vessels, increasing safety and operational window.
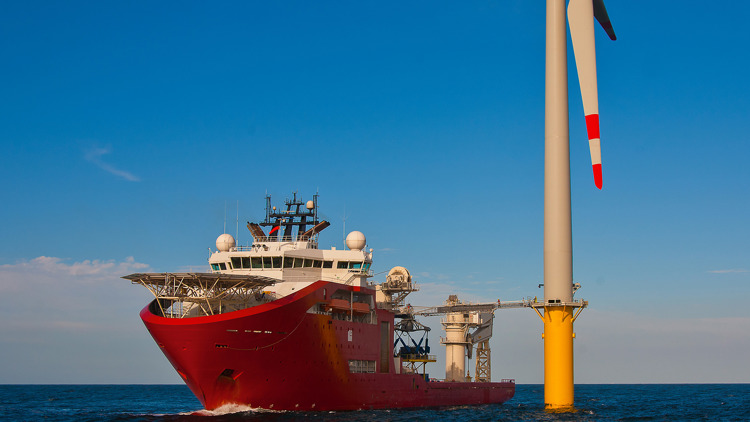
High accuracy
AHC is typically associated with on-board offshore cranes and winch control systems. Offshore cranes require precise data output on the roll and pitch motion of the crane tip. Real-time data output of heave amplitude, velocity and acceleration is essential for precise AHC during delicate offshore operations in often challenging conditions.
Roll and pitch measurements are used to transfer the heave motion from the MRU mounting location to the crane tip. The winch control system uses the crane tip heave measurement to adjust wire tension to keep the load in a steady state unaffected by the motion of the vessel. This ensures safe and efficient offshore crane and wire tensioning operations.
Kongsberg MRUs provide the "brain" embedded in AHC equipment that generates the data variables measuring heave values. These algorithms are used by the equipment processing unit to control and regulate electric or hydraulic motors that compensate for heave motions.
Kongsberg was the first technology company to industrialize inertial sensor technology for offshore applications at an affordable cost, replacing unwieldy, component- and maintenance-heavy human-operated mechanical compensation systems with a high damage risk factor due to the high forces involved.
Core benefits
The core benefits of MRU-based AHC solutions include increasing operational window in bad weather (within safety standards) and cost reduction, so improving the operational bottom line. Kongsberg MRUs are robust, maintenance-free and only require replacement after the 10-year guarantee period.
Other applications
Other offshore AHC applications that can benefit from MRU integration range from Launch and recovery systems (LARS) for Remotely Operated Vehicles (ROVs), Autonomous Underwater Vehicles (AUVs) and Unmanned Surface Vehicles (USVs) and offshore drilling draw works to helideck monitoring informing flight controllers of landing parameters.